间歇式反应器虽然用途广泛,并广泛应用于实验室和小规模生产环境,但也存在一些明显的缺点。这些缺点包括劳动力成本高、扩大生产规模面临挑战、操作过程中闲置时间长、仪器设备有限、产品质量不稳定以及爆炸等安全风险。此外,间歇式反应器通常更适用于均质反应,从而限制了其在更复杂的工业流程中的适用性。与产量更高、控制更好、制造成本更低的连续流动反应器相比,这些缺点使其效率和成本效益更低。
要点说明:
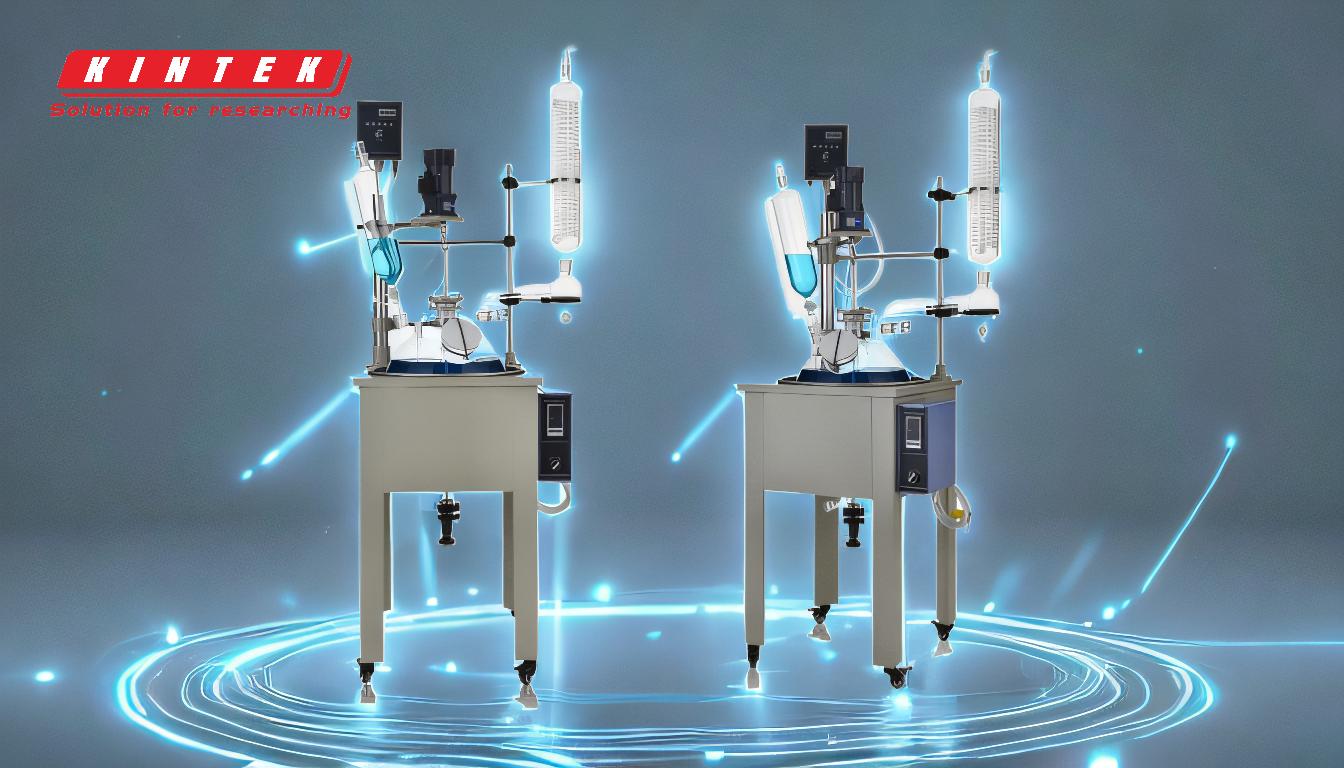
-
单位产量人工成本高
- 间歇式反应器需要大量人工干预加料、卸料和清洗等工作。这增加了人工成本,尤其是与连续流动反应器相比,后者自动化程度更高,需要的人工监督更少。
- 批量工艺的重复性也会导致效率低下,因为工人必须为每批产品多次执行相同的任务。
-
难以维持大规模生产
- 间歇式反应器的容量有限,而且需要频繁地启动-停止循环,因此不适合大规模工业生产。
- 使用间歇式反应器扩大生产规模通常需要使用多个反应器,这增加了成本和复杂性。相比之下,连续流反应器专为大批量生产而设计,可以不间断地连续运行。
-
加料和卸料期间闲置时间长
- 间歇式反应器生产周期的很大一部分时间都花在了非生产任务上,如装载反应物、加热或冷却系统以及卸载产品。
- 这些闲置时间会降低整体效率和产量,使间歇式反应器不适合时间敏感或高要求的生产工艺。
-
缺乏仪表和控制
- 间歇式反应器通常缺乏先进的仪表和控制系统,因此难以实时监控和优化反应条件。
- 由于操作员对温度、压力和混合等变量的控制能力较弱,这可能会导致产品质量不一致和工艺可靠性降低。
-
产品质量和一致性差
- 由于缺乏精确控制以及批次之间固有的可变性,间歇式反应器生产的产品质量往往不稳定。
- 在制药或特种化学品等对产品均匀性要求较高的行业,这种问题尤为突出。
-
清空过程中的爆炸风险
- 间歇式反应器可能会带来安全风险,尤其是在清空阶段,此时残留的反应物或副产品可能会发生不可预知的反应。
- 间歇式反应器的设计没有针对处理强烈爆炸进行优化,因此与连续流动反应器相比安全性较低,而连续流动反应器的设计可以更有效地管理高压和高温条件。
-
对均相反应的适用性有限
- 间歇式反应器主要适用于均相反应,即反应物和生成物处于单相(如液相或气相)。
- 对于涉及多相(如固液或气液)的异相反应,批式反应器的效果较差,这进一步限制了其在工业应用中的通用性。
-
制造和运行成本较高
- 虽然间歇式反应器由于设计简单,可以节省初始制造成本,但其运行效率低、劳动力要求高,往往会导致长期成本增加。
- 连续流反应器尽管初始投资较高,但随着时间的推移,其制造成本更低,产出价值比(VTO)更高。
-
无法达到稳态条件
- 间歇式反应器无法达到稳定状态,这意味着反应条件(如温度、压力和浓度)会随着时间的推移而变化。
- 这给控制和优化反应带来了挑战,导致潜在的效率低下和产品产量不理想。
-
过时的设计和技术
- 随着时间的推移,间歇式反应器的设计变化极小,依靠的是传统方法,缺乏连续流反应器的先进性。
- 这限制了它们与现代反应器技术竞争的能力,因为现代反应器技术具有更好的性能、更高的产量和更完善的安全功能。
总之,虽然间歇式反应器简单且用途广泛,但其缺点--从劳动力成本高、可扩展性差到安全风险和产品质量不稳定--使其不太适合现代工业应用。连续流反应器凭借其先进的技术和卓越的效率,越来越受到大规模和高要求生产工艺的青睐。
汇总表:
缺点 | 说明 |
---|---|
人工成本高 | 需要大量人工干预,增加了运营成本。 |
可扩展性差 | 由于频繁的启停周期,不适合大规模生产。 |
闲置时间长 | 充放电等非生产性工作降低了效率。 |
仪表有限 | 缺乏实时监控导致结果不一致。 |
产品质量不一致 | 批次之间的差异会影响产品的一致性。 |
安全风险 | 由于反应难以预测,清空过程中存在爆炸风险。 |
仅限于均相反应 | 对复杂的多相反应效果较差。 |
运营成本较高 | 长期低效超过初期节省的成本。 |
无稳态条件 | 反应条件会随着时间的推移而改变,因此很难进行优化。 |
技术落后 | 缺乏现代连续流反应器的先进性。 |
了解连续流反应器如何解决您的生产难题 立即联系我们 !