吹膜挤出虽然广泛用于塑料薄膜的生产,但也有一些缺点,会影响其效率和对某些应用的适用性。由于工艺复杂,很难精确控制薄膜厚度,而且容易出现各种生产问题。此外,与流延膜相比,吹膜的生产率通常较低,这会影响生产效率。这些挑战可能导致成本增加和质量下降,因此制造商在选择薄膜生产方法时必须仔细考虑这些缺点。
要点说明:
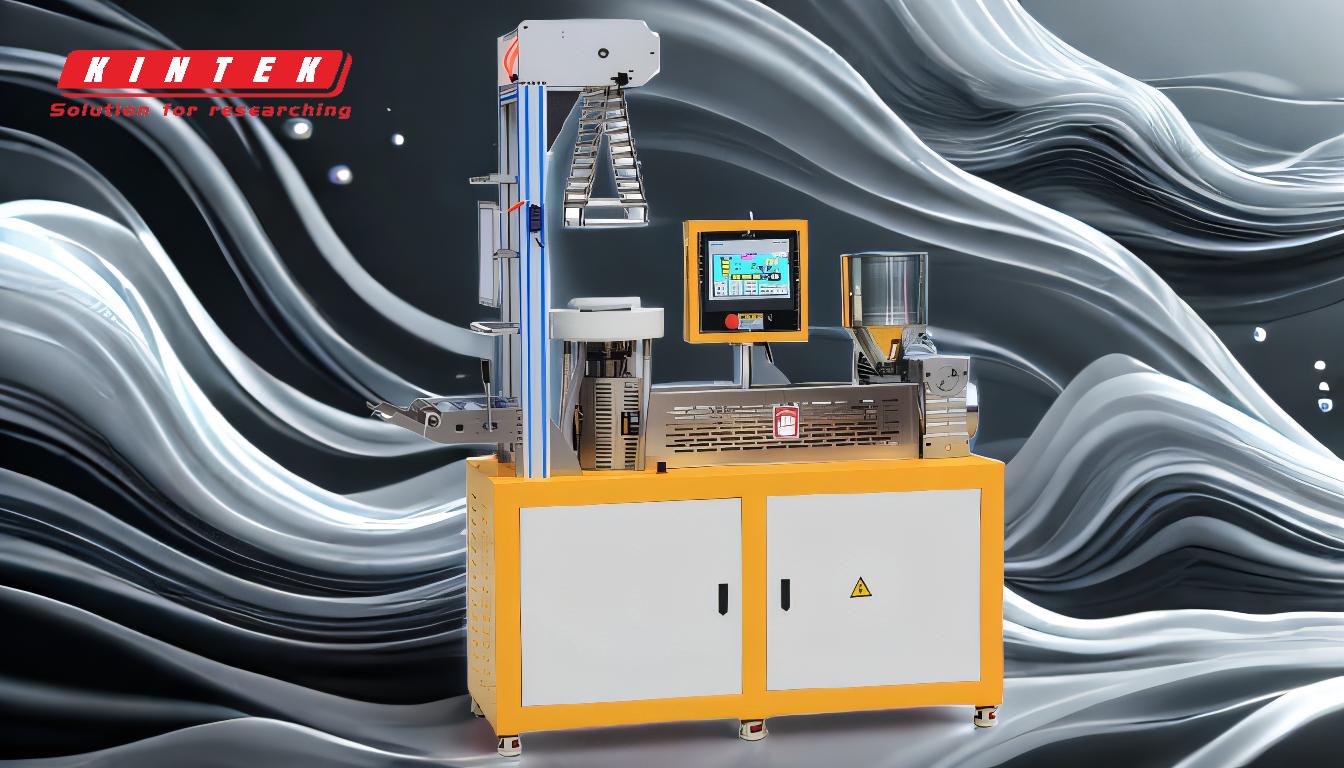
-
难以控制薄膜厚度:
- 解释: 吹膜挤出法的主要缺点之一是难以精确控制薄膜厚度。该工艺是将熔融聚合物通过一个圆形模头挤出,然后使其膨胀成气泡并冷却。由于挤压过程中的波动,如温度、压力或挤压速度的变化,薄膜的厚度会发生变化。这种不精确会导致薄膜厚度不均匀,从而影响薄膜的性能和对特定应用的适用性。
-
工艺复杂:
- 解释: 吹膜挤压是一种非常复杂的方法,涉及多个步骤和变量。这一过程需要仔细协调各种因素,包括挤出速度、冷却速度和气泡膨胀。这些参数的任何偏差都可能导致薄膜出现缺陷,如皱纹、凝胶或表面不平。工艺的复杂性还意味着需要熟练的操作人员和精密的设备,这可能会增加总体生产成本。
-
出现生产问题的风险更高:
- 解释: 由于吹膜挤出的复杂性,遇到生产问题的风险较高。常见问题包括气泡不稳定(可能导致薄膜撕裂或塌陷)和薄膜性能变化(如拉伸强度或阻隔性能)。这些问题会导致浪费增加和产量降低,进一步影响工艺的成本效益。
-
制造率低于铸膜:
- 解释: 与流延膜挤出法相比,吹膜挤出法的生产率通常较低。流延膜挤出是将聚合物通过平模挤出到冷冻辊上,冷却速度更快,生产速度更高。与此相反,吹膜挤出需要在薄膜膨胀成气泡时逐渐冷却,从而减慢了生产流程。这种生产速度上的差异会降低吹膜挤出法的大批量生产效率。
-
对成本和质量的影响:
- 解释: 难以控制薄膜厚度、工艺复杂、生产问题风险较高、生产率较低,这些因素结合在一起会导致成本增加和质量下降。制造商可能需要投资额外的质量控制措施或更先进的设备来缓解这些问题,这可能会进一步推高生产成本。此外,薄膜中可能存在的缺陷和不一致性也会影响其性能和适销性。
总之,虽然吹膜挤出是一种用途广泛的塑料薄膜生产方法,但它也有一些缺点,会影响生产效率、成本效益和最终产品的质量。制造商在决定最适合其特定需求的方法时,必须仔细权衡这些缺点和工艺的优点。
汇总表:
缺点 | 说明 |
---|---|
难以控制薄膜厚度 | 由于温度、压力或挤出速度的波动导致厚度不均匀。 |
工艺复杂 | 需要熟练的操作人员和先进的设备,增加了生产成本。 |
生产问题风险更高 | 气泡不稳定和褶皱或撕裂等缺陷会导致浪费增加。 |
生产率较低 | 与流延膜相比,生产速度较慢,影响大批量生产的效率。 |
对成本和质量的影响 | 更高的成本和潜在的缺陷会降低整体质量和市场竞争力。 |
正在为吹膜挤出难题而苦恼? 立即联系我们的专家 获取量身定制的解决方案!