溅射产率的定义是每个入射离子从目标材料中射出的原子的平均数量,它受几个关键因素的影响。这些因素包括入射离子的能量和质量、靶原子的质量和结合能、离子与表面碰撞的角度以及靶材料的晶体结构(如适用)。此外,腔室压力和电源类型(直流或射频)等外部因素也会间接影响溅射过程。了解这些依赖关系对于优化溅射沉积过程至关重要,因为溅射产量直接影响沉积速率和薄膜质量。
要点说明:
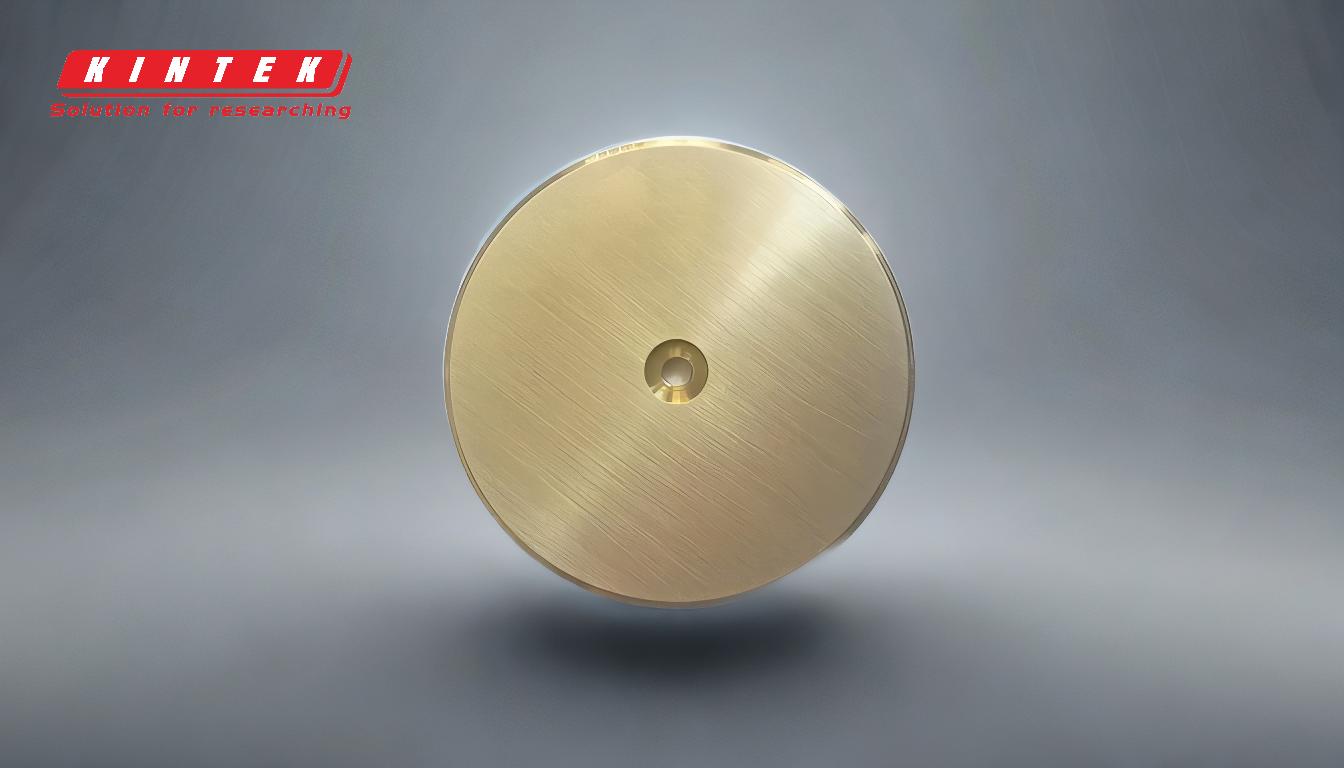
-
入射离子的能量:
- 溅射产率随入射离子能量的增加而增加,但只增加到一定程度。在 10 到 5000 eV 的能量范围内,产量随着离子能量的增加而增加。然而,在能量非常高的情况下,由于离子深入靶材料,降低了表面抛射效率,产量可能会趋于平稳甚至下降。
-
入射离子和靶原子的质量:
- 入射离子和靶原子的质量起着关键作用。较重的离子会将更多的动量传递给靶原子,从而增加了抛射的可能性。同样,由于结合能和质量较低,较轻的靶原子比较重的靶原子更容易被溅射。
-
靶原子的表面结合能:
- 目标材料中原子的结合能决定了它们能多容易被射出。表面结合能较低的材料溅射产量较高,因为将原子从表面移开所需的能量较少。
-
离子入射角:
- 离子撞击靶面的角度会影响溅射产率。在斜角(通常为 60 度左右)时,由于动量传递效率更高,因此产量最大。然而,在角度很浅或垂直的情况下,产量会降低。
-
目标物的晶体结构:
- 对于晶体材料,晶体轴相对于表面的取向会影响溅射成品率。某些取向可能使原子更容易沿着特定的晶体平面喷射,从而导致成品率的变化。
-
腔室压力:
- 腔室压力虽然不是影响溅射成品率的直接因素,但可通过改变粒子的平均自由路径和改善覆盖均匀性来影响工艺。较高的压力可能会降低入射离子的能量,从而间接影响产量。
-
电源类型:
- 电源(直流或射频)的选择会影响溅射过程。射频溅射通常用于绝缘材料,而直流溅射则优先用于导电目标。电源会影响沉积速率、材料兼容性和整体工艺效率。
-
发射粒子的动能:
- 溅射粒子的动能决定了它们的方向和在基底上的沉积。较高的动能可提高表面流动性和附着力,从而改善薄膜质量。
-
金属离子的过剩能量:
- 在沉积过程中,金属离子的过剩能量可提高表面流动性,从而改善薄膜的均匀性并减少缺陷。这将影响工艺的整体效率,从而间接影响溅射产量。
-
对设备和耗材采购商的实际影响:
- 了解这些因素对于选择合适的靶材料、离子源和电源至关重要。例如,选择结合能较低的靶材或优化离子入射角可显著提高沉积速率和薄膜质量。此外,选择合适的电源和腔室压力设置也能提高工艺效率并降低成本。
通过考虑这些因素,设备和耗材采购人员可以做出明智的决定,针对其特定应用优化溅射工艺。
总表:
因素 | 对溅射产量的影响 |
---|---|
入射离子的能量 | 在一定程度上提高产量;能量过高可能会降低效率。 |
离子和目标原子的质量 | 较重的离子和较轻的靶原子可提高产量。 |
表面结合能 | 结合能越低,产量越高。 |
离子入射角 | 约 60° 时产量最大;浅入射角或垂直入射角时产量减少。 |
晶体结构 | 取向会影响产量;某些平面更容易弹射。 |
腔室压力 | 通过改变离子能量和覆盖均匀性间接影响产量。 |
电源(直流/射频) | 影响材料兼容性和工艺效率。 |
微粒动能 | 更高的能量可提高附着力和流动性,从而改善薄膜质量。 |
金属离子的过剩能量 | 提高表面流动性,改善薄膜均匀性并减少缺陷。 |
准备好优化您的溅射工艺了吗? 立即联系我们的专家 获取量身定制的解决方案!