制药业中的研磨是一种关键工艺,用于减小粒度、提高溶解率和确保药物制剂的均匀性。研磨技术的选择取决于材料特性、所需粒度和具体应用。常见的研磨类型包括冲击研磨、剪切研磨和压缩研磨,每种类型都有独特的机理和应用。了解这些方法有助于制药商优化药物性能,确保符合法规要求,并获得稳定的产品质量。
要点说明:
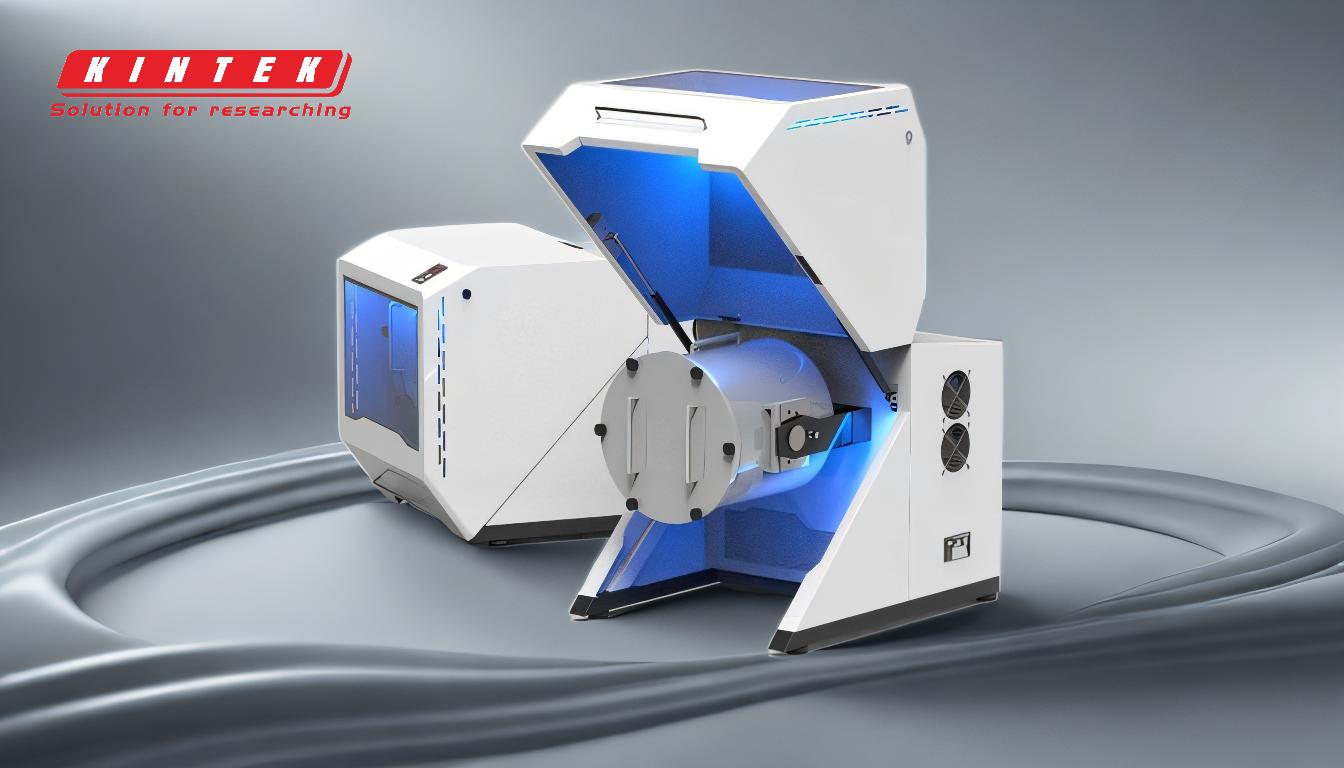
-
冲击研磨:
- 机制:冲击研磨是指颗粒与高速旋转的转子或锤子碰撞,通过冲击力将颗粒破碎成更小的尺寸。
- 应用:适用于脆性材料和粗磨,通常用于粒度减小的初始阶段。
- 设备:锤式粉碎机和针式粉碎机通常用于冲击粉碎。
- 优点:产量高,粗磨效率高,由于发热量极低,适用于热敏性材料。
- 局限性:可能产生较宽的粒度分布,对精细研磨效果较差。
-
剪切研磨:
- 机制:剪切研磨:剪切研磨通常使用刀片或旋转盘,依靠切割或剪切力来破碎颗粒。
- 应用领域:适用于纤维或坚硬材料,与冲击研磨相比,可获得更细的颗粒尺寸。
- 设备:刀磨机和切割机就是典型的例子。
- 优点:适用于冲击法难以研磨的材料,可产生较窄的粒度分布。
- 局限性:可能会产生热量,这对热敏材料来说可能是个问题。
-
压缩铣削:
- 机制:压磨是对颗粒施加压力,使其在压缩力作用下断裂或变形。
- 应用:通常用于硬脆材料和实现极细的颗粒尺寸。
- 设备:辊磨机和球磨机通常用于压缩研磨。
- 优点:产生均匀的颗粒大小,可有效进行精细研磨。
- 局限性:可能需要大量能源,并可能产生热量,因此需要冷却装置。
-
其他铣削技术:
- 喷射铣削:利用高速喷射的空气或气体碰撞颗粒,产生细微和超细颗粒。适用于热敏性材料,可获得微米大小的颗粒。
- 低温研磨:在研磨前将材料冷却到极低的温度(使用液氮),使脆性材料更容易研磨。非常适合热敏性或弹性材料。
- 湿铣:使用液体介质帮助减小粒度,通常用于在干燥条件下难以研磨的材料。
-
研磨技术的选择标准:
- 材料特性:考虑材料的硬度、脆性和热敏性。
- 所需的颗粒大小:选择可达到所需粒度分布的方法。
- 操作规模:确保设备能够处理所需的吞吐量。
- 遵守法规:验证制粉过程是否符合质量和安全方面的制药标准。
-
研磨在制药中的重要性:
- 提高溶解率:较小的颗粒尺寸可增加表面积,提高活性药物成分 (API) 的溶解率。
- 均匀性:确保一致的药物性能和剂量准确性。
- 工艺效率:优化下游工艺,如混合、制粒和压片。
- 符合法规要求:遵守粒度规格对于满足监管标准至关重要。
通过了解不同类型的研磨及其应用,制药商可以根据自己的具体需求选择最合适的方法,从而确保药物的最佳性能和符合法规要求。
汇总表:
铣削技术 | 机制 | 应用 | 设备 | 优势 | 局限性 |
---|---|---|---|---|---|
冲击铣削 | 颗粒与高速转子碰撞 | 脆性材料,粗磨 | 锤磨机、针磨机 | 产量高,发热量小 | 粒度分布广 |
剪切铣削 | 切削力或剪切力 | 纤维或坚硬材料,精细研磨 | 刀磨机、切割磨机 | 粒度分布窄 | 发热 |
压缩铣削 | 压碎颗粒 | 硬脆材料的精细研磨 | 辊磨机、球磨机 | 颗粒大小均匀 | 能源密集型,发热 |
喷射铣削 | 高速空气/气体碰撞 | 热敏材料、微米级颗粒 | 喷射研磨机 | 精细和超细颗粒 | 需要专用设备 |
低温铣削 | 用液氮冷却 | 热敏性或弹性材料 | 低温碾磨机 | 适用于脆性材料 | 需要冷却装置 |
湿法研磨 | 用于减少颗粒的液体介质 | 难以研磨的材料 | 湿磨 | 对特定材料有效 | 需要液体处理 |
需要帮助选择适合您制药需求的制粉技术? 立即联系我们的专家 获取量身定制的解决方案!