溅射虽然是一种广泛使用的薄膜沉积技术,但也有几个明显的缺点,会影响其效率、成本和对某些应用的适用性。这些缺点包括沉积速率低、基底加热高、难以与升离工艺相结合、污染风险大以及资本支出高。此外,溅射对绝缘材料和有机固体的效果较差,而且通常需要复杂的设备和对工艺参数的严格控制。了解这些局限性对于设备和耗材采购人员做出明智决策至关重要。
要点说明:
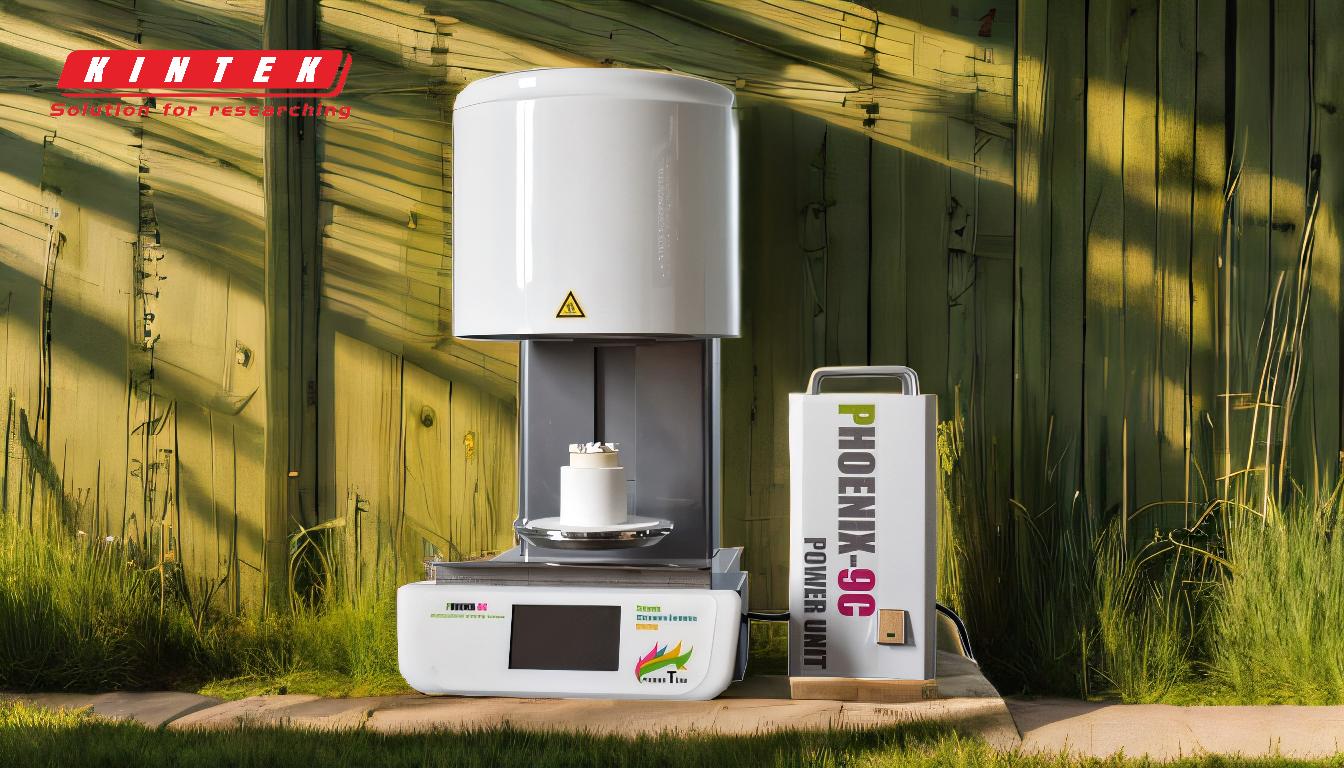
-
低沉积率:
- 与热蒸发等其他方法相比,溅射法的沉积率通常较低。当需要高产量时,这可能是一个很大的缺点。
- 例如,二氧化硅等材料的沉积率特别低,会导致生产过程放缓。
-
高基底加热效应:
- 溅射过程会产生大量热量,从而导致基底温度过高。这对于温度敏感的材料或需要精确热控制的情况下可能会造成问题。
- 基底温度过高也会造成热应力,影响沉积薄膜的质量。
-
使用绝缘材料的困难:
- 溅射并不适合绝缘材料,因为它们会积累电荷,导致电弧和其他问题,从而破坏沉积过程。
- 受此限制,必须使用其他方法或额外设备来有效处理绝缘材料。
-
与吊装工艺相结合的挑战:
- 溅射的弥散传输特性使其难以实现全阴影,而这对于薄膜成型中使用的升华过程至关重要。
- 这可能会导致污染问题,并使薄膜的图案化复杂化。
-
污染风险:
- 与蒸发法相比,溅射法的真空度较低,这增加了将杂质带入基底的风险。
- 气体污染物可能会在等离子体中被激活,进一步增加薄膜污染的风险。
-
资本支出高:
- 溅射所需的设备通常既复杂又昂贵,因此初始资本成本很高。
- 维护和运行成本也可能很高,从而增加了总支出。
-
材料退化:
- 在溅射过程中,有机固体和其他敏感材料很容易被离子轰击降解。
- 这就限制了利用溅射技术有效沉积的材料范围。
-
复杂的设备和过程控制:
- 溅射系统通常需要高压设备和对工艺参数(如反应溅射沉积中的气体成分)的精心控制。
- 设备的复杂性和精确控制的需要会增加操作的难度和成本。
-
材料使用效率低:
- 溅射靶材通常价格昂贵,而且就材料使用而言,该工艺可能效率低下。
- 入射到靶材上的大部分能量都会变成热量,而热量必须被移除,这进一步加剧了效率低下的问题。
-
均匀性问题:
- 溅射法的沉积流量分布通常不均匀,需要使用移动夹具来实现均匀的薄膜厚度。
- 这会使沉积过程复杂化,并影响最终薄膜的质量。
通过了解这些缺点,购买者可以更好地评估溅射是否是满足其特定需求的正确选择,并在必要时探索替代方法。
汇总表:
缺点 | 说明 |
---|---|
沉积速率低 | 与热蒸发等方法相比速度较慢,尤其是对于二氧化硅等材料。 |
基底温度高 | 产生大量热量,造成热应力并影响对温度敏感的材料。 |
绝缘体的困难 | 绝缘材料会积累电荷,导致电弧和工艺中断。 |
提升工艺挑战 | 扩散传输使薄膜结构变得复杂,并增加了污染风险。 |
污染风险 | 较小的真空范围会增加杂质;等离子体会激活气体污染物。 |
资本支出高 | 设备复杂昂贵,维护和运营成本高昂。 |
材料降解 | 有机固体和敏感材料会因离子轰击而降解。 |
复杂的设备和控制 | 需要高压设备和精确的参数控制,增加了操作难度。 |
材料使用效率低 | 目标昂贵,能源效率低,因为大部分能源都变成了热能。 |
均匀性问题 | 不均匀的沉积流量要求移动夹具以获得均匀的薄膜厚度。 |
需要帮助选择正确的薄膜沉积方法? 立即联系我们的专家 获取量身定制的解决方案!