回转窑的热效率是其性能的关键因素,影响着能源消耗、运营成本和环境影响。虽然电加热回转窑由于热损失最小,能效可达 95% 以上,但大多数回转窑的运行条件更为复杂,热效率受传热、材料特性和窑炉设计等因素的影响。热效率并不是一个固定值,而是根据窑炉设计、运行参数和加工材料的不同而变化。通过优化热回收、燃烧效率和物料停留时间等因素,可以显著提高热效率。本答案将探讨影响热效率的关键因素,以及如何优化这些因素以提高性能。
要点说明:
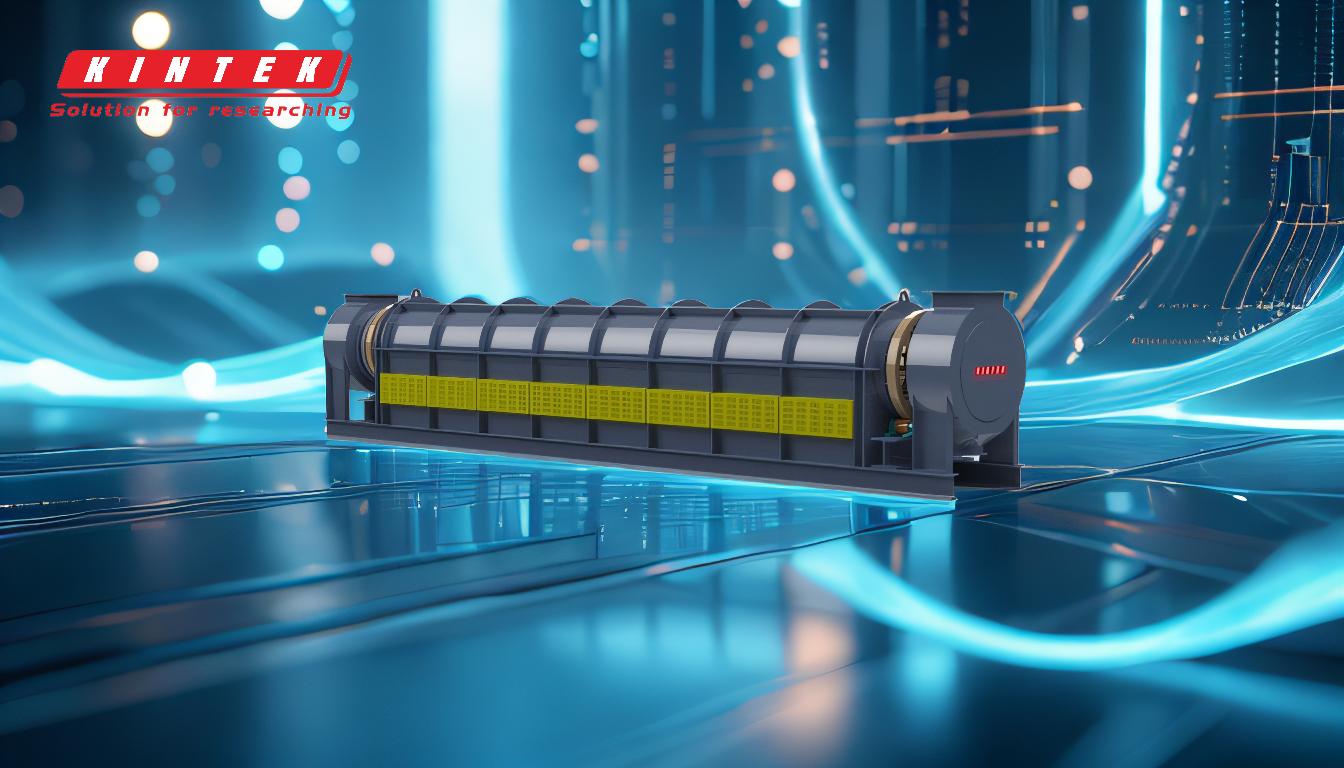
-
回转窑热效率的定义:
- 热效率是指工艺中利用的有用热能与供给窑炉的总热能之比。它是衡量窑炉如何有效地将输入能量转化为用于材料加工的生产热量的标准。
- 在电加热回转窑中,由于没有气体流动,热损失极小,热效率可超过 95%。然而,在大多数工业回转窑中,由于废气、辐射和对流造成的热损失,热效率较低。
-
影响热效率的因素:
- 传热机制:窑炉内部环境与被加工材料之间的高效热传导至关重要。材料特有的热量、热传导率和温度曲线等因素都会影响热传导率。
- 燃烧效率:在燃料燃烧窑中,燃料不完全燃烧会导致能源浪费。升级为多通道燃烧器或优化燃烧器设计可提高燃烧效率。
- 热量回收:预热器和冷却器分别用于回收废气和热产品中的热量。回收的热量可预热燃烧空气或进料,从而降低总体能耗。
- 保留时间:材料在窑炉中停留的时间会影响其加热的彻底程度。优化停留时间可确保完全吸收热量,避免不必要的能源消耗。
-
设计和运行参数:
- 窑炉尺寸和几何形状:窑的尺寸,包括长度和直径,影响热量分布和保温时间。大小合适的窑可确保热量得到最佳利用。
- 倾角和转速:这些参数控制物料在窑炉中的移动。适当的调整可确保加热均匀,防止能源浪费。
- 耐火衬:在窑衬中添加一层耐火陶瓷纤维,可通过更好的隔热效果减少热量损失并提高热效率。
-
材料特性:
- 粒度和体积密度:较小的颗粒和较高的体积密度可增加受热表面积,从而改善传热效果。
- 化学成分和反应热:具有放热反应的材料可促进窑炉的热平衡,减少对外部能源输入的需求。
- 磨蚀性和腐蚀性:这些特性会影响窑衬和部件的耐用性,间接影响长期效率。
-
提高热效率的策略:
- 定期维护和监测:通过日常检查和调整确保窑炉在最佳条件下运行,防止因故障或磨损造成能源损失。
- 升级辅助设备:对燃烧器、预热器和冷却器进行现代化改造可提高燃烧和热回收效果,从而直接提高热效率。
- 运输现象定量分析:了解窑床内的动量和能量传输,可精确控制颗粒运动和加热速率,优化能源使用。
-
对环境和经济的影响:
- 高热效率可减少燃料消耗、降低运营成本并最大限度地减少温室气体排放。
- 在提高效率方面的投资,如先进的耐火材料或热回收系统,通常会产生显著的长期节约和环境效益。
通过解决这些因素,回转窑运营商可以获得更高的热效率,从而实现更具可持续性和成本效益的运营。
汇总表:
因素 | 对热效率的影响 |
---|---|
传热机制 | 高效的热传递可确保均匀加热,减少能源浪费。 |
燃烧效率 | 优化燃烧器设计可提高燃料利用率并减少能量损失。 |
热量回收 | 回收废气和产品中的热量可降低总体能耗。 |
停留时间 | 适当的停留时间可确保完全吸收热量,而不会产生不必要的能量消耗。 |
窑炉尺寸和几何形状 | 适当的尺寸可确保最佳的热量分布和利用。 |
耐火衬里 | 隔热内衬可减少热量损失并提高效率。 |
材料特性 | 粒度、密度和化学成分会影响传热和能源需求。 |
准备好提高回转窑的热效率了吗? 立即联系我们的专家 获取量身定制的解决方案!