锂离子电池的应用现状
环境和能源危机
不断升级的环境问题和迫在眉睫的能源危机推动了全球向可持续能源解决方案的转变。这一转变凸显了新能源汽车和先进储能技术在缓解这些紧迫挑战方面的关键作用。减少碳排放和对化石燃料的依赖是当前环境和能源危机的核心,而减少碳排放和对化石燃料的依赖则进一步加剧了这一转变的紧迫性。
新能源汽车,特别是以锂离子电池为动力的汽车,为减少温室气体排放和应对气候变化提供了一条大有可为的途径。这些车辆不仅能减少对石油的依赖,还能通过最大限度地减少尾气排放来改善空气质量。此外,高容量锂离子电池等先进储能技术的开发对于平衡太阳能和风能等可再生能源的间歇性至关重要。
在锂离子电池中集成硅基负极材料代表了这一领域的重大进展。硅具有很高的理论比容量,与传统的石墨负极相比有很大改进。然而,与硅相关的挑战,如在锂化/退锂过程中体积变化大和导电性差,需要创新的解决方案。例如,碳涂层已成为提高硅负极导电性和稳定性的可行策略,从而改善锂离子电池的整体性能。
总之,全球能源转型不仅仅是应对环境和能源危机,而是建设可持续未来的积极战略。新能源汽车和储能技术的进步,特别是涉及硅基材料的技术,在这一努力中至关重要。随着研发工作不断突破极限,创造一个更具可持续性和复原力的能源生态系统的可能性也越来越大。
锂离子电池的优势
锂离子电池已成为现代能源存储系统的基石,这主要归功于它们的众多优点。其中最显著的优点是 对环境影响小 .与传统的铅酸电池不同,锂离子电池不含有毒重金属,从而降低了生产、使用和处理过程中的污染风险。这种环保特性使其成为从消费电子产品到电动汽车等各种应用的理想选择。
此外,锂离子电池还拥有 超长循环寿命 .它们可以经历数百次(甚至数千次)充放电循环,而不会出现明显的性能下降。锂离子电池的超长寿命可确保使用锂离子电池供电的设备长期保持功能,从而降低更换频率和相关成本。
高能量密度 高能量密度 锂离子电池的高能量密度是推动其广泛应用的另一个关键因素。这些电池可以在紧凑的空间内存储大量能量,因此非常适合便携式电子产品和电动汽车,因为空间和重量是这些产品的关键考虑因素。这种高能量密度可带来更长的运行时间和更大的行驶范围,从而提升用户体验和便利性。
除了这些核心优势外,锂离子电池还具有以下特点 快速充电功能 和 低自放电率 .快速充电可让用户快速补充电池电量,而低自放电则可确保电池在长时间闲置时仍能保持电量。这些特点加上轻巧的设计和高效率,使锂离子电池适用于从智能手机和笔记本电脑到可再生能源存储系统和电动汽车等众多应用领域。
石墨负极的局限性
石墨是商业上最常见的负极材料,但它也面临着一些固有的限制,这些限制阻碍了它在锂离子电池中的表现。主要缺点之一是理论比容量相对较低,这限制了可储存的锂离子数量,从而限制了电池的整体能量密度。在对更高能量存储解决方案(如电动汽车和便携式电子产品所需的解决方案)的需求不断增长的背景下,这一限制尤为重要。
此外,石墨的嵌入锂电位较低,存在潜在的安全隐患。这种特性会导致镀锂等问题,即充电时金属锂不均匀地沉积在负极表面的现象。锂镀层不仅会降低电池的效率,还会带来严重的短路风险,从而导致热失控,在极端情况下甚至会导致电池故障或爆炸。
总之,尽管石墨仍是锂离子电池行业的基石,但由于其在容量和安全性方面的局限性,有必要探索和采用替代材料,如硅基负极,它们有望解决这些缺陷,并为下一代电池技术铺平道路。
硅基阳极材料
硅阳极的优势
硅作为一种极具潜力的锂离子电池负极材料脱颖而出,主要是因为它具有优异的理论比容量。与理论容量约为 372 mAh/g 的石墨不同,硅的理论容量要高得多,约为 4200 mAh/g。容量的大幅增加意味着更长的电池寿命和更高的能量密度,这使得硅基阳极在需要延长工作时间和紧凑设计的应用中非常受欢迎。
此外,硅的安全性能也优于石墨。石墨阳极由于内含锂电势较低,容易出现安全问题,尤其是在锂化过程中。相比之下,硅阳极的电化学性能更稳定、更安全,可降低热失控风险以及与锂离子电池相关的其他安全隐患。这种安全性的提高对于确保电池系统的可靠性和使用寿命至关重要,尤其是在电动汽车和便携式电子产品等高需求应用领域。
总之,在开发新一代锂离子电池的过程中,高理论比容量和更好的安全性能使硅成为石墨的最佳替代品。
硅负极面临的挑战
硅负极在锂离子电池中的应用面临几个重大挑战。其中最重要的一个问题是硅在脱锂离子过程中会发生巨大的体积变化。这种体积膨胀和收缩会导致材料的机械降解,从而导致性能低下和容量快速衰减。
此外,硅的导电性较差,进一步加剧了其性能限制。为了解决这些问题,研究人员探索了各种策略,例如通过纳米结构改变硅的尺寸。这种方法开发出了复合分层硅阳极,成为未来应用的主要焦点。
2020 年代初,技术的进步使这些复合阳极濒临商业化,美国已建立了大规模生产设施。尽管发展前景广阔,但人们仍在继续寻找最佳的负极材料。例如,金属锂比硅具有更高的比容量,但也面临一系列挑战,包括金属锂的不稳定性和形成枝晶的风险。
固体电解质相间层(SEI)仍然是一个关键的设计挑战,尤其是在金属锂阳极方面。如果能成功稳定金属锂,它就能在保持轻质外形的同时提供最高的充电容量,从而彻底改变电池技术。
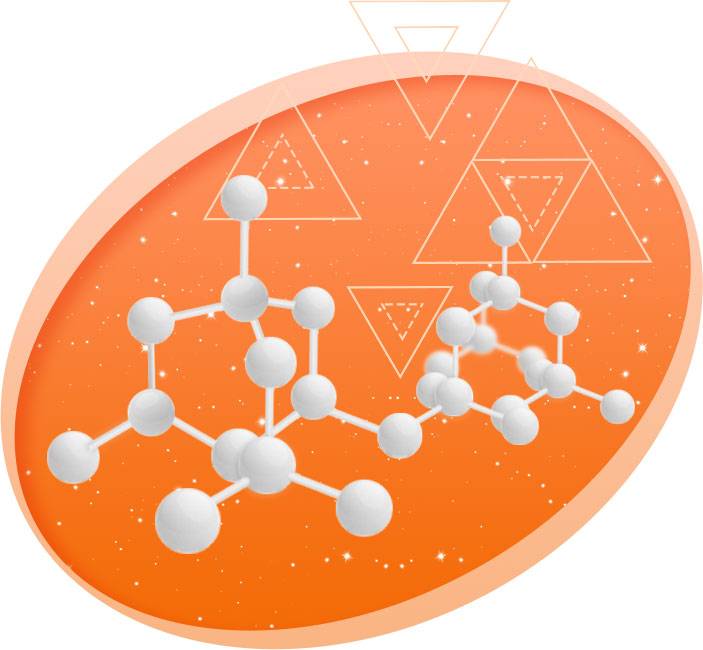
应对挑战的策略
针对硅作为锂离子电池负极材料所面临的固有挑战,研究人员实施了多种创新策略。这些策略旨在提高硅的导电性,减轻其在循环过程中的体积膨胀,并改善其整体电化学性能。
主要方法之一包括 纳米结构 这种方法是将硅颗粒的尺寸减小到纳米级。这种方法充分利用了纳米级表面积的增加和扩散长度的减少,从而改善了锂离子插入和提取的动力学性能。此外,纳米结构硅能更有效地适应与锂化和脱锂相关的大体积变化,从而减少机械应力和颗粒断裂的风险。
另一个关键策略是 表面涂覆导电元素 .碳具有出色的电子导电性和机械稳定性,是最常用的导电涂层。碳涂层可采用化学气相沉积(CVD)、高能球磨和喷雾干燥等多种技术。这些涂层可作为保护层,防止硅与电解质直接接触,从而减少不良固态电解质相间层(SEI)的形成,并提高阳极的循环稳定性。
此外,使用 刚性矩阵结构 在循环过程中提供机械支撑并缓冲硅的体积变化。这些基质结构通常由碳或其他刚性材料组成,可以封装硅颗粒,提供一个稳定的框架,保持结构的完整性,防止阳极材料解体。
策略 | 描述 | 优势 |
---|---|---|
纳米结构 | 将硅颗粒尺寸减小到纳米级 | 提高动力学性能,更好地适应体积变化,减少断裂 |
表面涂层 | 在硅表面涂覆导电涂层(如碳涂层 | 增强导电性,减少 SEI 的形成,提高循环稳定性 |
刚性基质 | 使用刚性结构封装硅 | 机械支撑、保持结构完整性、防止分解 |
这些策略共同旨在利用硅的高理论比容量,同时克服其局限性,从而为其在下一代锂离子电池中的实际应用铺平道路。
硅碳复合材料的制备方法
化学气相沉积(CVD)
化学气相沉积(CVD)是一种复杂的真空沉积技术,用于生成高质量、高性能的固体材料。这种工艺广泛应用于半导体行业的薄膜沉积,对提高设备性能至关重要。在典型的 CVD 设置中,基底(通常是硅晶片)暴露在一种或多种挥发性前体中。这些前驱体在基底表面发生化学反应或分解,形成所需的涂层。同时会产生挥发性副产品,这些副产品随后会通过反应腔内的气流排出。
CVD 尤其适用于为硅涂覆碳,这种工艺可显著提高锂离子电池中硅基材料的循环特性。碳涂层不仅能提高硅的导电性,还能在锂化和脱锂循环过程中缓冲其巨大的体积变化。尽管具有这些优点,但 CVD 的特点是复杂性高、成本高,这可归因于复杂的设置和对各种工艺参数的精确控制。
CVD 的多功能性进一步体现在它能够沉积各种不同形式的材料,包括单晶、多晶、非晶和外延结构。这些材料包括二氧化硅、碳化物、氮化物和氧氮化物等硅化合物,以及碳纤维、纳米纤维、纳米管、金刚石和石墨烯等先进碳材料。此外,CVD 还能沉积钨和氮化钛等金属以及高κ电介质,使其成为微加工过程中的多功能工具。
CVD 的发展可追溯到 1960 年,当时小约翰-M-布洛赫(John M. Blocher)创造了这一术语,以区别于物理气相沉积(PVD)。多年来,人们开发了各种形式的 CVD,每种形式的化学反应启动方式都不尽相同。例如,热壁热化学气相沉积以批量模式运行,而等离子体辅助化学气相沉积则利用等离子体来增强沉积过程。这些变化凸显了 CVD 的适应性,使其成为生产先进材料的基石,可用于多种应用,包括锂离子电池等储能技术。
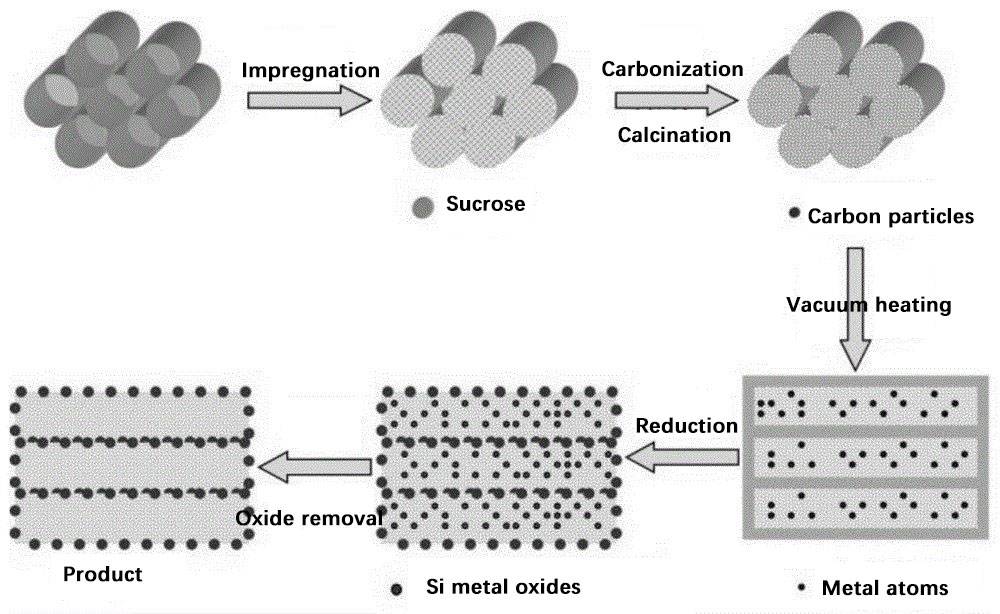
高能球磨
高能球磨是制备硅碳复合材料(尤其是用于锂离子电池)的一种稳健而高效的方法。这种技术利用研磨球或研磨珠的高动能来粉碎和混合材料,有利于快速减小尺寸和机械合金化。该工艺对金属、合金、陶瓷和矿物等硬脆材料特别有效,是硅基负极材料的理想选择。
主要优势
- 生产周期短:高能球磨的突出特点之一是其快速加工能力。高速、高强度的研磨作用可快速产生细小颗粒,从而大大缩短材料制备所需的时间。
- 成本效益高:与化学气相沉积(CVD)等其他方法相比,高能球磨更经济。所需的设备不那么复杂,操作成本也较低,因此对工业应用来说是一种具有经济吸引力的选择。
局限与挑战
- 硅含量:尽管高效,高能球磨法在硅含量方面仍有局限性。该工艺会导致硅颗粒的结构损坏和降解,从而影响阳极材料的整体性能。
- 结构损伤:高能冲击会产生巨大的机械应力,导致硅颗粒中形成缺陷和裂缝。这种结构性损坏会损害最终产品的完整性和电化学性能。
在锂离子电池中的应用
高能球磨法在锂离子电池中特别有用,因为在锂离子电池中最需要的是研磨精细、混合均匀的材料。这种方法可以生产出具有高表面积和高活性位点的硅碳复合材料,这对提高电池性能至关重要。然而,由于硅含量和结构损伤方面的固有挑战,有必要对其进行仔细优化,并在可能的情况下整合额外的表面改性技术,以缓解这些问题。
总之,虽然高能球磨为快速、经济地制备硅碳复合材料提供了一条前景广阔的途径,但要充分发挥其在锂离子电池先进负极材料生产中的潜力,必须解决其局限性。
喷雾干燥
喷雾干燥是制备硅碳(Si/C)复合材料的关键方法,尤其是在将其用作锂离子电池的负极材料时。这种技术有几个明显的优点,有助于提高负极的整体性能和稳定性。
喷雾干燥的主要优点之一是能够生产出具有以下特性的复合材料 高容量保持率 .这对于确保阳极在多次循环中保持其电荷携带能力至关重要,而这正是锂离子电池寿命的关键因素。该方法通过仔细控制复合结构的形成来实现这一目标,这有助于最大限度地减少容量衰减。
此外,喷雾干燥还有助于形成 合适的孔隙结构 孔隙结构。这种孔隙结构对阳极材料至关重要,因为它能增强材料内部的电解质渗透和离子传输。更好的离子传输可提高电化学性能,包括更快的充电时间和更高效的能量存储。
该工艺包括将前驱体溶液雾化成细液滴,然后将其干燥形成固体颗粒。这些颗粒随后经过热处理,形成最终的硅/碳复合材料。喷雾干燥过程中的可控环境允许对颗粒大小和形态进行精确调整,这对优化材料性能至关重要。
总之,喷雾干燥是生产 Si/C 复合材料的一种通用而有效的方法,这种复合材料具有高容量保持率和理想的孔隙结构,非常适合用作锂离子电池的负极材料。
水热法
水热法是一种用于合成硅碳复合材料的复杂技术,涉及高温水热蒸发过程。这种方法利用水热条件的独特特性,制造出具有优异循环稳定性的复合材料,特别是在加入碳化钒(VC)添加剂后。
在水热过程中,高温环境有利于硅和碳之间形成稳定的化学键,从而产生一种非常适合用于锂离子电池的复合材料。VC 添加剂的加入进一步增强了这些复合材料的循环稳定性,使其结构更加坚固,能够承受反复的充放电循环而不会出现明显的降解。
这种方法尤其具有优势,因为它能够生产出具有高度均匀性和结构完整性的复合材料。高温条件可确保复合材料无缺陷,这对于保持锂离子电池负极材料的长期性能至关重要。此外,使用水热蒸发法可以精确控制复合材料的微观结构,这对优化其电化学性能至关重要。
总之,水热法为制备具有优异循环稳定性的硅碳复合材料提供了一条前景广阔的途径,使其成为目前开发先进锂离子电池负极材料的一项重要技术。
溶胶-凝胶法
溶胶-凝胶法是一种用途广泛的薄膜和其他材料制备技术,尤其适用于锂离子电池的硅基负极。这种方法包括形成胶体悬浮液,即所谓的 "溶胶",然后过渡到固态的凝胶体相。一系列水解和聚合反应促进了这一转变,从而形成了浸入溶剂中的稳定固态大分子。
溶胶-凝胶法的主要优点之一是能在相对较低的实验温度下操作,因此是研究人员的实用选择。此外,该过程简单明了,易于管理,只需极少的专用设备。然而,这些优点也是有代价的。众所周知,溶胶-凝胶法的合成成本较高,加工时间较长,这可能是一个很大的缺点,尤其是在工业应用中,效率和成本效益是最重要的。
优点 | 缺点 |
---|---|
实验温度低 | 合成成本高 |
操作简单 | 加工时间长 |
尽管存在这些挑战,溶胶-凝胶法仍然是制备硅碳复合材料的重要工具,它兼顾了其他方法难以实现的控制性和灵活性。
微波法
微波合成已成为生产石墨烯涂层硅材料的一种前景广阔的技术,这种材料具有卓越的电化学特性。这种方法利用微波快速加热材料的独特能力,在硅基底上形成高质量的石墨烯层。由此产生的石墨烯涂层硅材料具有很高的可逆比容量,这对于提高锂离子电池的储能能力至关重要。
微波法的主要优势之一是能够生产出具有卓越循环稳定性的材料。这是通过微波提供的均匀而快速的加热来实现的,这种加热促进了稳定的导电石墨烯涂层的形成。这种涂层不仅能提高硅基阳极的整体导电性,还能缓解硅在锂化和脱锂过程中常见的体积膨胀问题。
优势 | 描述 |
---|---|
高可逆容量 | 石墨烯涂层可提高硅的比容量,从而改善能量存储。 |
良好的循环稳定性 | 均匀加热可确保石墨烯层的稳定性,从而提高循环性能。 |
减缓体积膨胀 | 导电涂层有助于缓冲硅的体积变化,减少容量衰减。 |
微波法因其相对较短的合成时间和生产质量稳定的材料的能力而特别具有吸引力。这些特性使其成为化学气相沉积 (CVD) 和高能球磨等其他碳涂层技术的竞争性替代品,而这些技术通常涉及更复杂、更耗时的过程。
总之,微波合成法提供了一种简化的方法来制造石墨烯涂层硅材料,非常适合先进的锂离子电池应用。通过将硅的高容量与石墨烯的导电和保护特性相结合,这种方法为开发具有更高性能和稳定性的下一代负极材料铺平了道路。
原位合成
原位合成是一种直接在硅纳米粒子上催化碳层生长的复杂方法。这种技术对于增强硅和碳之间的界面结合强度特别有利,而界面结合强度对于提高锂离子电池中硅基阳极的整体电化学性能至关重要。
该工艺包括在硅表面可控地沉积碳原子,从而形成一个坚固的导电界面。这种界面不仅能缓解硅在锂化和脱锂循环过程中发生的体积变化,还能显著增强材料的导电性。因此,与传统的硅阳极相比,硅碳复合材料具有卓越的循环稳定性和更高的容量保持率。
此外,原位合成法还可以精确调整碳层厚度和结构,从而进一步提高阳极的性能。这种定制水平尤其有利于解决与硅阳极相关的特殊难题,如导电性差和容量衰减快等。
总之,原位合成为开发高性能硅碳复合阳极提供了一条前景广阔的途径,为解决传统硅基材料在锂离子电池中的局限性提供了强有力的解决方案。
联系我们获取免费咨询
KINTEK LAB SOLUTION 的产品和服务得到了世界各地客户的认可。我们的员工将竭诚为您服务。如需免费咨询,请与我们的产品专家联系,以找到最适合您应用需求的解决方案!