Introduction to Cold Isostatic Pressing
Cold Isostatic Pressing (CIP) is a process used to compact powders into a specific shape or size. This method involves subjecting the powders to high pressure, typically between 100 and 200 MPa, in a liquid medium. The liquid medium ensures that the pressure is applied uniformly in all directions, resulting in a product that is dense and free of voids. CIP is a versatile technique that can be used to produce a wide range of products, from simple shapes to complex components with intricate geometries. The process is widely used in industries such as powder metallurgy, refractory metals, and automobiles, where it is valued for its ability to produce components with excellent mechanical properties and corrosion resistance.
Table of Contents
Isostatic vs. Cold Pressing
When it comes to compacting powders, two popular methods are isostatic pressing and cold pressing. While both methods can produce high-quality materials, they differ in several ways.
Isostatic Pressing
Isostatic pressing involves applying equal pressure to a compacted powder to achieve optimal density and microstructure uniformity. The press uses a gas or liquid to deliver force to a hermetically sealed container filled with the metal powder using either elevated or ambient temperatures. These processes are known as hot and cold isostatic pressing, respectively.
Isostatic pressing has several advantages over other methods, such as low distortion on firing and consistent shrinkage on firing. Additionally, parts can be fired without drying, most green (unfired) compacts can be machined, and there are low internal stresses in compact as pressed. Isostatic pressing can also be used to press compacts of very high length-diameter ratio (> 200), parts with internal shapes, including threads, splines, serrations, and tapers, and long thin-walled parts. Weak powders can also be pressed using isostatic pressing, and it is possible to press a compact having two or more layers of powder possessing different characteristics.
However, isostatic pressing also has some disadvantages. For example, there is lower accuracy of pressed surfaces adjacent to the flexible bag, compared with mechanical pressing or extrusion, usually necessitating subsequent machining. Additionally, relatively expensive spray-dried powder is normally required for fully automatic dry bag presses, and there are lower production rates than for extrusion or die compaction.
Cold Pressing
Cold pressing is a process of compressing a powder into a solid shape without the use of heat. This method is often used to produce simple-shaped powder compacts with a uniform green density. It is also an effective method for powders that are difficult to press, such as hard metals.
One of the advantages of cold pressing is that it can produce parts with high dimensional accuracy and a consistent density throughout the part. Additionally, cold pressing allows for the production of complex shapes, and the process is relatively fast and inexpensive.
However, cold pressing also has some disadvantages. For example, the density of the final part is lower than that of isostatic pressing, and there can be internal voids or defects in the part. Additionally, the process may not be suitable for all types of powders, and subsequent machining may be necessary to achieve the desired shape.
Isostatic Pressing vs. Cold Pressing
In comparison, isostatic pressing can produce parts with higher density and more uniform density distribution than cold pressing. Isostatic pressing can also produce parts with complex shapes and high length-diameter ratios, while cold pressing is best suited for simple-shaped parts. Additionally, isostatic pressing may be more expensive and slower than cold pressing, but it is more accurate and produces fewer defects. Ultimately, the choice between isostatic pressing and cold pressing will depend on the specific requirements of the application.
Uniform Strength and Versatility
Cold Isostatic Pressing (CIP) is a versatile manufacturing process that can produce objects with uniform strength and density. The process involves placing a material, such as a metal powder or ceramic, into a flexible mold and then subjecting it to high-pressure fluids from all sides. This results in a product that has uniform strength, density, and no porosity.
Uniform strength
The pressure used to compact the materials is equal in all directions, resulting in a material with uniform strength. This uniform strength of the cold isostatic pressed material makes it more efficient than those without uniform strength.
Versatility
CIP can be used to produce difficult shapes that cannot be produced by other methods, making it more versatile. The process can be used to produce large-sized materials, and the only limitation to the size of materials produced by this method is the size of the pressure vessel. This makes it possible to produce complex shapes and dimensions with high accuracy.
Corrosion Resistance
Cold isostatic pressing improves the corrosion resistance of a material. Thus materials that undergo this process have a longer lifespan than most other materials.
Powder Metallurgy
Cold isostatic pressing is used in powder metallurgy to produce complex shapes and dimensions with high accuracy. It is used for the compacting step of powder metallurgy that comes just before the sintering step. CIP is often used to produce difficult shapes and dimensions that cannot be produced by other methods.
Refractory Metals
CIP is used to produce refractory metals such as tungsten, molybdenum, and tantalum. Tungsten, for example, is used to manufacture wires for filaments in the lamp industry. Generally, refractory metals have a high melting point and are resistant to wear and tear.
Sputtering Targets
Cold Isostatic Pressing (CIP) can press indium tin oxide (ITO) powder into large ceramic preforms, which are then sintered under certain conditions. This method can theoretically produce ceramic targets with a density of 95%.
Automobiles
Cold isostatic pressing is used in manufacturing automobile components such as bearings and oil pump gears. This results in high-quality components with excellent mechanical properties.
In conclusion, the uniform strength and versatility offered by Cold Isostatic Pressing makes it an attractive option for manufacturers looking to produce high-quality, complex components with excellent mechanical properties. CIP has various applications, including powder metallurgy, refractory metals, sputtering targets, and automobile components. The uniform strength achieved through the CIP process makes it more efficient, while its versatility makes it possible to produce complex shapes and dimensions with high accuracy.
Corrosion Resistance and Improved Mechanical Properties
Cold Isostatic Pressing (CIP) is a manufacturing process used to produce high-density, homogeneous materials that are resistant to corrosion and have improved mechanical properties. This process is particularly useful for producing parts and components that require high strength, durability, and resistance to wear and tear.
Corrosion Resistance
One of the key benefits of CIP is its ability to improve the corrosion resistance of materials, making them ideal for use in harsh environments where exposure to chemicals, moisture, and other corrosive agents can cause damage. The high-pressure fluids applied during the CIP process compress the material and close any gaps or pores that may otherwise allow corrosive agents to penetrate the surface.
Improved Mechanical Properties
CIP can enhance the mechanical properties of materials, including their tensile strength, hardness, and ductility, enabling them to withstand greater stress and strain. This makes CIP an ideal choice for producing complex parts and components that require high precision and accuracy.
CIP vs. Traditional Methods
Compared to traditional manufacturing methods, CIP offers superior corrosion resistance and improved mechanical properties. For example, parts made using CIP have a higher density and are more homogeneous than those produced using other methods, resulting in improved mechanical properties. Additionally, CIP can produce parts in complex shapes that would be difficult or impossible to make using other methods.
Materials Used in CIP
Common materials used in CIP include ceramic powders, graphite, refractory materials, electrical insulators, and advanced ceramics such as silicon nitride, silicon carbide, boron nitride, boron carbide, and spinel.
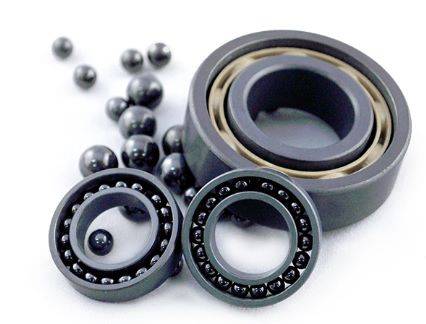
Applications of CIP
The benefits of CIP make it ideal for a wide range of applications. It is widely used in the manufacturing of laboratory equipment, aerospace components, and medical devices, among other applications. CIP is also expanding into new applications such as pressing of sputtering targets, coatings of valve parts in an engine to minimize wear of the cylinder heads, telecommunications, electronics, aerospace, and automotive.
In conclusion, Cold Isostatic Pressing (CIP) is a highly effective manufacturing process that offers numerous benefits. CIP can improve the corrosion resistance of materials, enhance their mechanical properties, and produce parts in complex shapes. Its applications are diverse, and it is widely used in the manufacturing of laboratory equipment, aerospace components, and medical devices, among others.
Applications in Powder Metallurgy, Refractory Metals, and Automobiles
Cold Isostatic Pressing (CIP) has numerous applications in various industries, including powder metallurgy, refractory metals, and automobiles.
Powder Metallurgy
In powder metallurgy, CIP is used to manufacture high-performance components such as gears, bearings, and cutting tools. The technique is ideal for this application as it produces high-density materials with complex shapes and intricate details. The CIP process removes porosity, increases density, and enhances mechanical properties, resulting in products with uniform density, close tolerances, and better machinability.
Refractory Metals
CIP is also used in the refractory metals industry to produce parts that can withstand extreme temperatures and harsh environments. Components such as refractory nozzles, blocks, and crucibles, cemented carbides, isotropic graphite, ceramic insulators, tubes for special chemical applications, ferrites, metal filters, preforms, and plastic tubes and rods are made through this process.
Automobiles
The automotive industry uses CIP to create lightweight and efficient engine parts such as pistons and cylinder heads. The high initial cost of pressing dies cannot be justified for these parts, and the CIP process allows for the creation of complex shapes and close tolerances. This results in lightweight and efficient engine parts, which are essential for reducing fuel consumption and emissions.
Benefits of CIP
The benefits of CIP make it a valuable technique for various industries. The process produces high-density materials with complex shapes and intricate details, eliminates porosity, increases density, and enhances mechanical properties. CIP also results in products with uniform density, close tolerances, and better machinability. The technique is relatively inexpensive and does not require high initial costs for pressing dies. The ability to create complex shapes and close tolerances makes it ideal for applications where strength, durability, and precision are essential.
In conclusion, Cold Isostatic Pressing (CIP) is a valuable technique for various industries, including powder metallurgy, refractory metals, and automobiles. Its ability to produce high-density materials with complex shapes and intricate details, eliminate porosity, increase density, and enhance mechanical properties make it an ideal choice for applications where strength, durability, and precision are essential.
Sintering and Green Strength
Cold Isostatic Pressing (CIP) is a powerful tool for improving the sintering and green strength of materials, making it an important process in the manufacturing of a wide range of products, including aerospace components, medical devices, and electronic components.
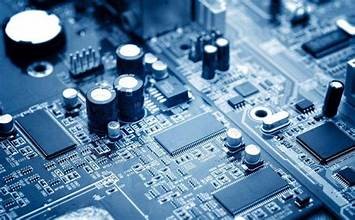
Sintering
Sintering is the process of heating a material to a high temperature without melting it, causing the particles to bond together. The high pressure applied during CIP helps to compact the material, resulting in a more uniform density and improved sintering. The process of sintering is a crucial step in the manufacturing of ceramic and metal materials. By using CIP, the sintering process is improved, making the material more durable and easier to handle during subsequent processing steps.
Green Strength
The green strength of a material refers to its ability to maintain its shape and structure during handling and processing. CIP helps to increase the green strength of materials by reducing the amount of voids and defects present in the material. When the material is compressed, the particles are rearranged, resulting in a more compact structure that is less prone to cracking or distortion during handling. This makes the material much easier to work with during processing and reduces the amount of scrap and waste generated during manufacturing.
Benefits of CIP
The benefits of CIP in improving the sintering and green strength of materials are significant. The process results in a more uniform density, improved sintering, and increased green strength. This makes the material more durable and easier to handle during subsequent processing steps, reducing the amount of scrap and waste generated during manufacturing. Additionally, the improved sintering process results in a material that is more resistant to wear and corrosion, making it ideal for use in harsh environments.
In conclusion, CIP is a powerful tool for improving the sintering and green strength of materials, making it an important process in the manufacturing of a wide range of products. By using CIP, the sintering process is improved, making the material more durable and easier to handle during subsequent processing steps. The increased green strength of materials reduces the amount of scrap and waste generated during manufacturing, making the process more cost-effective. CIP is a crucial step in the manufacturing of ceramic and metal materials, and its benefits are significant for a wide range of industries.
Conclusion
Cold Isostatic Pressing is a highly effective method for compacting and shaping materials. It offers numerous advantages over traditional pressing techniques, including greater uniformity of strength and improved mechanical properties. The process is versatile and adaptable, making it ideal for a wide range of applications, including powder metallurgy, refractory metals, and automobiles. With its ability to improve green strength and corrosion resistance, Cold Isostatic Pressing is becoming an increasingly popular choice for manufacturers seeking to improve the performance of their products. Overall, this technology represents a significant step forward in materials science and is sure to play an important role in shaping the future of manufacturing.
联系我们获取免费咨询
KINTEK LAB SOLUTION 的产品和服务得到了世界各地客户的认可。我们的员工将竭诚为您服务。如需免费咨询,请与我们的产品专家联系,以找到最适合您应用需求的解决方案!