简介
等静压等静压是一种制造工艺,在各行各业中具有众多优点和应用。它是将材料置于来自各个方向的同等压力下,以达到均匀的密度和形状。与其他生产技术相比,这种方法尤其具有优势。等静压可以生产出具有复杂内部形状和长薄壁的零件,而其他方法可能难以实现这一点。但是,必须考虑到等静压的局限性,例如与其他技术相比,等静压的压制表面精度较低,生产率较低。
等静压工艺概述
等静压的解释
等静压是一种利用流体压力压实粉末混合物并减少孔隙率的粉末加工技术。粉末混合物使用等静压封装,等静压从各个方向施加相同的压力。这种工艺是将金属粉末封闭在柔性膜或密封容器内,在粉末和环绕粉末的加压介质(液体或气体)之间形成压力屏障。
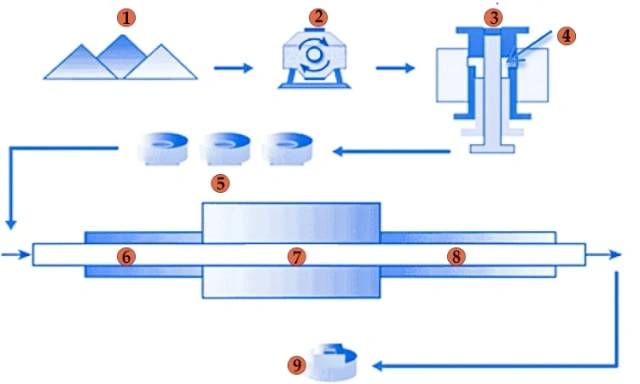
等静压类型:湿袋和干袋
等静压操作一般有两种类型:湿袋和干袋。湿袋变化包括使用一个单独的弹性模具,该模具在压机外装载,然后浸没在压力容器中。加压和压实后,将模具从容器中取出,取回零件,然后重复该过程。一次加压可将多个模具装入容器。
另一方面,干袋工艺通过创建一个与压力容器融为一体的模具,省去了浸泡步骤。在干袋工艺中,粉末被添加到模具中,模具被密封,施加压力,然后部件被顶出。与湿袋工艺相比,该工艺中的集成模具更易于实现自动化。
陶瓷的成型压力
等静压为陶瓷和耐火材料应用提供了独特的优势。无论产品的形状或尺寸如何,它都能在整个产品上施加均匀且相等的力。这一特性使产品形状的形成具有精确的公差,从而减少了昂贵的机加工需求。等静压工艺已广泛应用于高温耐火材料、陶瓷、硬质合金、镧系永久磁铁、碳材料和稀有金属粉末的成型。
等静压已成为各行各业用于固结粉末或修复铸件缺陷的可行生产工具。等静压技术能够实现高密度和复杂形状,因此在许多应用中成为首选。不过,需要注意的是,与单轴压制相比,该工艺的模具成本和复杂程度更高。
等静压的优势
与其他生产方法相比,等静压工艺具有多项优势。让我们来详细了解等静压工艺与其他工艺相比的一些优势:
等静压工艺与其他生产方法相比的优势
- 烧制时变形小:等静压在烧制过程中变形极小,确保了最终产品的尺寸精度。
- 烧制时收缩率一致:在烧制过程中,等静压部件的收缩率是一致的,因此可获得可预测的均匀结果。
- 部件无需干燥即可烧制:与其他方法不同,等静压工艺无需事先干燥即可烧制零件,从而节省了时间和能源。
- 可降低粉末中的粘合剂含量:等静压可以降低粉末混合物中的粘合剂含量,从而减少额外的加工步骤。
- 大多数生坯(未烧制)可进行机械加工:等静压成型的绿色环保型压实材料易于加工,为生产过程提供了灵活性。
- 压制密实材料的内应力低:等静压工艺使压制件的内应力较低,从而降低了开裂或变形的风险。
- 超大压制件能力:等静压工艺可采用湿袋法生产超大型零件,从而扩大了应用范围。
- 模具成本低:与其他制造方法相比,等静压工艺的模具成本较低,因此对于短期生产而言是一种经济高效的选择。
- 在给定的压制压力下密度更高:与机械压制方法相比,在给定的压制压力下,等静压工艺可获得更高的密度,从而生产出更坚固耐用的零件。
- 能够压制长径比非常高的紧凑型产品:等静压工艺可生产高长径比的紧凑型产品,因此应用范围更广。
- 能够压制具有内部形状的零件:等静压工艺可压制具有螺纹、花键、锯齿和锥度等内部形状的零件,从而扩大了设计的可能性。
- 能够压制长薄壁零件:等静压工艺能够生产长薄壁零件,为产品设计提供了多样性。
- 压制弱粉末的能力:等静压工艺可有效压制弱粉末,提高材料利用率和最终产品的整体质量。
- 能够压制具有不同特性的两层或多层粉末压制件:等静压工艺可生产多层粉末压制物,每层粉末都具有不同的特性,从而提高了材料的特性和性能。
等静压工艺具有一系列优势,是各行各业首选的生产方法。让我们来详细了解一下它的一些功能。
等静压的功能
- 密度均匀:等静压可确保压制件具有均匀的密度,从而在烧结或热等静压过程中实现一致的收缩,并将翘曲降至最低。
- 形状灵活性:等静压可生产出其他方法难以实现或无法实现的形状和尺寸,从而提供设计灵活性。
- 部件尺寸:等静压工艺可适应各种部件尺寸,从 30 吨的大型近净粉末冶金形状到重量不足 100 克的小型 MIM 部件。
- 较大部件:等静压室的大小是对零件尺寸的唯一限制,因此适合生产大型零件。
- 增强合金化可能性:等静压可在不引起材料偏析的情况下增加合金元素,从而扩大了材料的选择范围。
- 缩短交货时间:从原型到批量生产,等静压工艺可经济地生产复杂形状的产品,与传统制造方法相比,大大缩短了生产周期。
- 降低材料和加工成本:使用等静压工艺可制造出接近净形的零件,从而减少了材料浪费和加工成本。
等静压技术以其独特的优势和能力在各行各业得到广泛应用。让我们来看看等静压机的一些常见应用。
等静压机的应用
- 制药
- 炸药
- 化学品
- 食品
- 核燃料
- 铁氧体
等静压机的其他应用行业(制药、炸药、化工、核燃料铁氧体)
等静压是一种多功能生产方法,与其他技术相比具有众多优势。它适用于多种材料,可以高精度地生产复杂形状和尺寸的产品。无论是实现均匀密度、压制内部形状复杂的零件,还是降低模具成本,等静压都被证明是许多行业的重要制造选择。
等静压的缺点
与其他技术相比,等静压是一种具有各种优势的生产方法。然而,它也并非没有缺点。让我们来详细了解一下等静压的一些缺点:
压制表面精度较低
等静压的一个缺点是软袋附近的压制表面精度较低。这意味着可能需要进行后续加工才能达到所需的精度。相比之下,机械压制或挤压技术通常能获得更精确的压制表面。
全自动干袋压机成本较高
等静压常用的全自动干袋压机需要相对昂贵的喷雾干燥粉末。这会增加工艺的总体成本。使用高质量的材料和专用设备也是造成这种压机费用较高的原因。
与挤压或压模相比,生产率较低
与挤压或模具压制方法相比,等静压的生产率较低。这意味着就产量而言,该工艺的效率可能不高。在选择不同的压制技术时,必须考虑生产要求和时间安排。
尽管存在这些缺点,等静压仍具有独特的优势,使其成为某些应用的重要选择。它在烧制过程中变形小、收缩率一致,可以加工生坯,并能压制内部形状和长径比高的零件。此外,等静压还能获得比机械压制更高的密度,并能压制多层粉末压制物。
重要的是要根据具体的制造需求权衡等静压的利弊,以确定它是否是特定应用的正确选择。
干袋等静压
干袋等静压的解释和应用
干袋等静压是一种在加工或烧结前将粉末状材料压制成均匀的固体团块的方法。它是一种简单的工艺,可生产高完整性的坯料或预型件,在烧制时变形或裂纹最小。这种工艺特别适合生产具有轴对称几何形状的较小硬质合金制品。
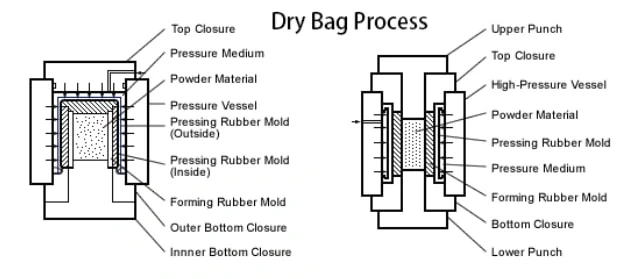
干袋工艺
干袋等静压工艺的自动化优势
干袋压制的主要优点是可以实现自动化,从而可以经济高效地批量或半批量生产几何形状复杂的硬质合金产品。这包括棒、管、衬套、球、柱塞、钻头、螺钉、喷嘴等。
干袋等静压工艺的自动化还能生产出具有精确外部和内部尺寸的近乎网状的空心绿色压实物。这大大减少了所需的加工量,从而减少了切屑的产生。
WC-Co 粉末质量和压制模具设计的作用
WC-Co 粉末的质量和压制模具的设计对有效制造硬质合金绿色压制件起着至关重要的作用。必须仔细选择粉末质量,以确保最终产品具有适当的压实性和所需的性能。
不同的压制模具设计方案,如集成模具或可更换模具,可为压制过程提供灵活性。当硬质合金产品的尺寸在一定时期内保持不变时,集成式模具更为理想,而柔性模具系统则更适合频繁更换模具的情况。
干袋压机的组件
干袋压制机由高压泵、弹性压制模具、带薄膜的压制室和压力容器组成。压力由高压泵产生,并通过薄膜沿径向传递到装有 WC-Co 粉末的压模。压模可手动或自动装载。
一次压制通常持续 5-10 分钟,生产一个绿色压制件。干袋系统可以压制直径达 200 毫米、长度达 600 毫米的棒材或管材。此类管材的内径和外径的压制公差从 0.1 毫米到 1 毫米不等,具体取决于其尺寸。
总之,干袋等静压是将粉末状材料压制成均匀固体的有效方法。它具有自动化大批量生产、尺寸精确和降低加工要求等优点。WC-Co 粉末的质量和压制模具的设计是成功制造的关键因素。
湿袋等静压
湿袋等静压的解释和应用
湿袋技术是一种冷等静压方法,在这种方法中,粉末被填充到模具中,并在压力容器外严密密封。然后将模具浸没在容器内的压力流体中,在模具外表面施加等静压,将粉末压制成固体块。
这种工艺不像干袋等静压那样普遍,但全世界使用的湿袋压制机超过 3000 台。湿袋的尺寸从直径 50 毫米到 2000 毫米不等。
湿袋技术相对较慢,加工时间从 5 到 30 分钟不等。不过,使用大容量泵和改进的装载机制有助于加快工艺流程。
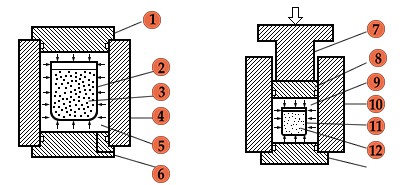
湿袋工艺(1.顶盖 2.橡胶模具 3.粉末 4.高压 5.压力介质 6.底盖 7.阀杆 8.活塞 9.压力介质 10.高压容器 11.橡胶模具 12.粉末 13.底盖)
湿袋等静压的优势
-
湿袋等静压具有以下几个优点:
-
密度均匀:湿袋等静压可以接近等静压的理论概念,从而获得密度均匀、夹带应力小的压制物。这样就可以在生坯状态下进行加工,而不会产生变形。
-
减少变形:通过湿袋等静压技术生产的部件在烧制时几乎不会变形,从而减少或消除了昂贵的机加工需求。
自动化潜力:湿袋等压工艺非常适合自动化生产,因此适合以较高的生产率压制相对较长的紧凑型产品。
湿袋和干袋等压工艺的区别
-
湿袋等静压和干袋等静压的主要区别在于压制粉末的方法:
-
湿袋等静压:在湿袋等静压法中,粉末是在完全浸没在加压流体中的密封弹性模具中压制的。这种方法适用于特种零件的小批量生产、原型制作和研发。
干袋等静压:在干袋等静压中,弹性模具是等静压的一个组成部分。施加的压力多为双轴,该工艺可实现自动化,以满足大批量生产的需要。
湿袋和干袋等静压各有利弊。湿袋更适合生产大型部件,可在摩擦最小的情况下获得更高的密度。但是,装卸模具会降低生产率,限制自动化程度。而干袋等静压则在自动化和生产率方面更具优势。
总之,选择等静压是为了获得高密度和单轴压力机无法压制的形状。选择湿袋还是干袋等静压取决于生产工艺的具体要求。
单轴压制与等静压制
等静压可克服单轴压制的局限性
等静压可以克服单轴压制在常规颗粒包装方面的一些局限性。等静压与单轴压制不同,等静压从各个方向施加压力,而单轴压制只从一个方向施加压力。这使得压实更加均匀,填料均匀度更高。等静压通常采用两种方法:湿袋和干袋。
在湿袋等静压法中,粉末被填入一个柔性模具中,密封后浸入高压容器中的液体中。液体被加压,压力通过模具的柔性壁传递给粉末,从而产生压实效果。与单轴压制相比,湿袋等静压具有更高的包装均匀性。压力最高可达 1000 GPa,但最常见的生产设备的压力可达 200-300 MPa。湿袋等静压结合三维绿色加工,可用于制造复杂的高质量陶瓷部件。
干袋等静压比湿袋工艺更容易实现自动化。它包括一个与压力容器紧密相连的橡胶模。然而,加压液体并不是从所有方向作用的,因此必须仔细设计模具,以确保粉末密实中的颗粒包装均匀。
单轴压制和等静压制绿化体的比较
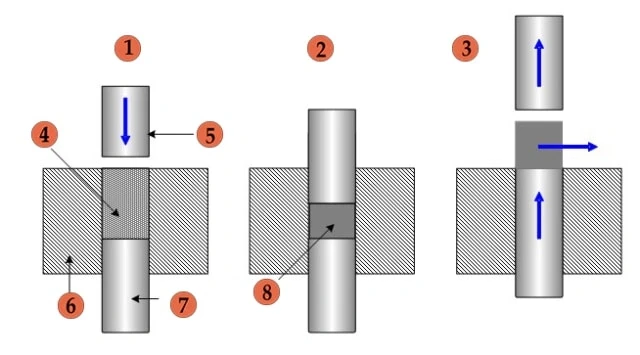
单轴压制技术示意图(1.模具填充阶段 2.压实 3.部件顶出 4.粉末 5.上冲头 6.模具 7.下冲头 8. "绿色 "压实)
单轴压制与等静压制相比,单轴压制更适用于生产率较高的小型产品。但是,模壁摩擦可能会导致密度不均匀,尤其是在长宽比较大的情况下。而等静压则可用于小型或大型、简单或复杂的形状。均匀的生坯密度使烧结过程中的收缩更加均匀,这对形状控制和均匀性能非常重要。等静压还无需使用单轴压制中使用的蜡粘合剂,从而省去了脱蜡操作。
低成本的弹性体模具可用于等静压,但只有在高精度钢芯轴上压制的表面才能获得接近的公差。与弹性体模具接触的表面可能需要进行后加工,以获得严格的公差和良好的表面光洁度。
总之,等静压通过从各个方向施加压力,克服了单轴压制的某些局限性。它能提供更高的填料均匀性,在烧结过程中产生更均匀的收缩,并且无需使用蜡粘合剂。等静压可以通过湿袋法或干袋法进行,每种方法都有自己的优点和局限性。
等静压的粉末制备
等静压对粉末的要求
等静压是一种利用流体压力压实零件的粉末加工技术。为了达到最佳效果,等静压所使用的粉末必须满足某些要求。
其中一个重要要求是粉末的粒度分布。在等静压时,建议使用粒度为 1-5 μm 的粉末。这一粒度范围可形成密度高于理论密度 98% 的材料。使用平均粒径约为 0.5 μm 的未掺杂氧化铝粉末可有效达到上述密度。
另一个要求是粉末混合物中的粘结剂含量。粘合剂的作用是在压制过程中将粉末颗粒固定在一起。具体的粘合剂含量取决于所使用的粉末类型和最终产品所需的性能。通常情况下,粘合剂含量为 20%-30%,纤维素蜡混合物是常见的选择。
调整粒度分布和粘合剂含量
为了优化等静压之前的粉末调节,可以对粒度分布和粘合剂含量进行调整。
粒度分布可通过将粉末研磨成更细的粒度来调整。理想情况下,用于等静压的粉末粒度应小于 75 μm。更细的粒度可以更好地压实,确保样品颗粒更均匀。
粘合剂含量也可根据生产部件的具体要求进行调整。增加粘合剂含量可以增加压制颗粒的强度,而减少粘合剂含量则会使颗粒结构更加多孔。重要的是要在强度和孔隙率之间找到适当的平衡,使最终产品达到所需的性能。
通过仔细考虑等静压工艺对粉末的要求,并对粒度分布和粘合剂含量进行调整,制造商可以生产出具有所需性能的高质量零件。等静压为粉末压制提供了一种通用而有效的方法,可以生产多种材料。
结论总而言之 等静压
联系我们获取免费咨询
KINTEK LAB SOLUTION 的产品和服务得到了世界各地客户的认可。我们的员工将竭诚为您服务。如需免费咨询,请与我们的产品专家联系,以找到最适合您应用需求的解决方案!