制备用于 X 射线荧光 (XRF) 分析的压制颗粒是确保结果准确可靠的关键步骤。这一过程包括将样品研磨成细粉,与粘合剂混合,然后在高压下压制成均匀的颗粒。这种方法可以提高样品的均匀性,消除空隙,减少样品稀释,从而获得更好的分析结果。压制颗粒因其方便性、成本效益和可靠性而被广泛使用,成为 XRF 样品制备的行业标准。
要点说明:
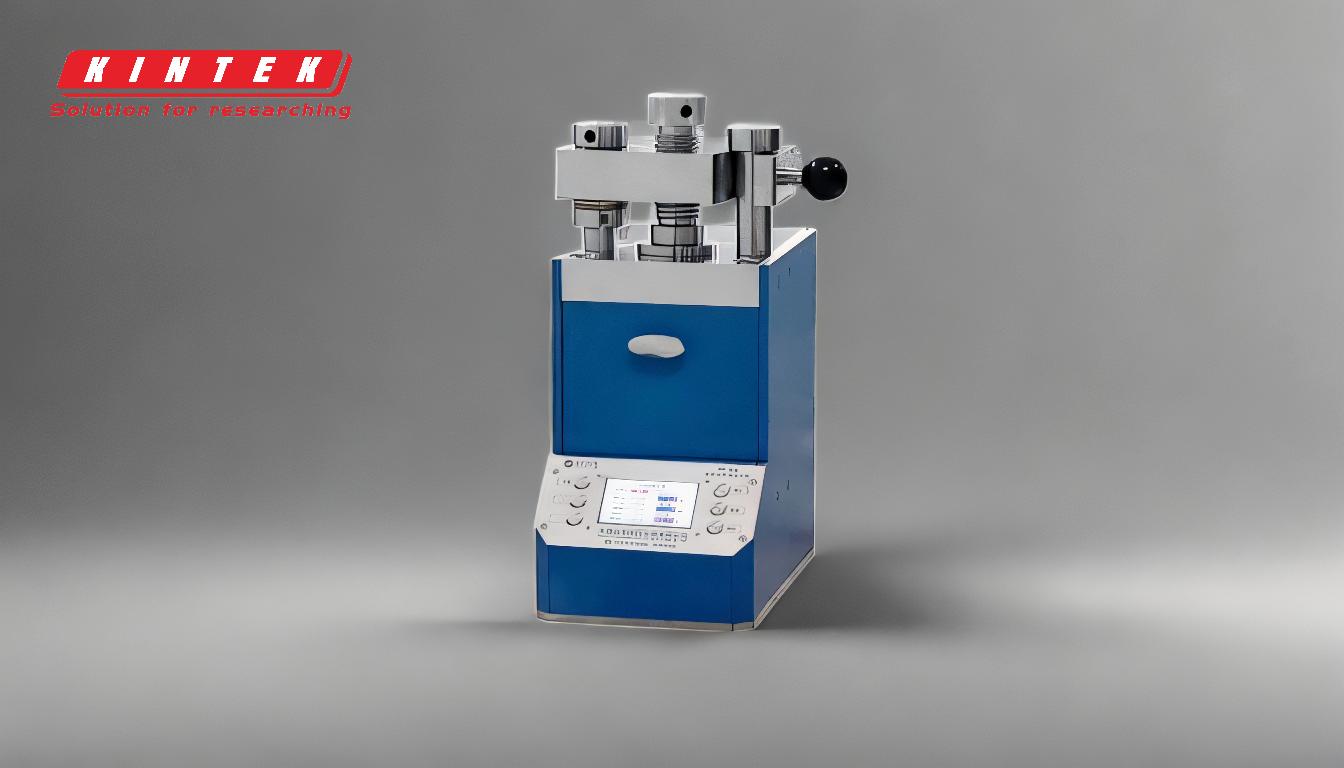
-
将样品研磨成细粉:
- 制备压制颗粒的第一步是将样品研磨成细小的颗粒。理想情况下,粒度应小于 75µm,最佳粒度应小于 50µm。小粒径至关重要,因为它能确保更好的均匀性,降低粒度效应的风险,而粒度效应会影响 XRF 分析的准确性。可以使用粉碎机或类似设备进行研磨。
-
与粘合剂混合:
- 研磨后,将粉末样品与粘合剂或研磨助剂混合。常见的粘合剂包括纤维素蜡混合物,它有助于在压缩过程中将颗粒粘合在一起。粘合剂与样品的比例一般在 20% 到 30% 之间。粘合剂可确保样品附着良好,形成没有裂缝或空隙的固体颗粒,否则会导致分析结果不一致。
-
将混合物压制成颗粒:
- 然后将粉末样品和粘合剂的混合物倒入压模中。压模的设计目的是在高压(通常在 15 至 40 吨之间,但最常见的压力范围在 20 至 30 吨之间)下保持样品。高压会压缩混合物,形成致密、均匀的颗粒。这一步骤至关重要,因为它可以消除空隙,确保样品均匀分布,这对精确的 XRF 分析至关重要。
-
压制颗粒的优势:
- 与松散粉末或其他样品制备方法相比,压制颗粒具有多种优势。由于颗粒均匀且无空隙,大多数元素的分析强度较高,因此能提供更好的分析结果。压制颗粒尤其适用于分析 ppm 范围内的微量元素。此外,它们的制备相对简单且成本低廉,只需要粉碎机和样品压片机等基本设备。
-
注意事项和局限性:
- 虽然压制颗粒非常有效,但也并非没有局限性。它们仍然容易受到粒度效应和矿物效应的影响,尤其是对主要元素而言。因此,必须确保将样品研磨到适当的粒度,并将粘合剂与样品充分混合,以尽量减少这些影响。
-
自动化和手动压制:
- 压制颗粒可采用自动系统或手动压制。自动系统速度更快、更稳定,适合高通量实验室使用。而手动压片机则更具成本效益,可用于小型实验室或不太频繁的分析。只要研磨、混合和压制步骤正确,这两种方法都能制备出高质量的颗粒。
按照这些步骤,您就可以制备出用于 XRF 分析的高质量压制颗粒,确保结果准确可靠。该过程简单明了、成本效益高,并在业内广泛使用,是任何实验室进行 XRF 分析的必备技术。
汇总表:
步骤 | 关键细节 |
---|---|
研磨 | 粒度小于 75µm(最佳粒度小于 50µm),以获得更好的均匀性。 |
与粘合剂混合 | 使用 20-30% 的粘合剂(如纤维素蜡),以确保粘合力并防止裂缝。 |
压制 | 施加 20-30 吨压力,形成致密、均匀的颗粒。 |
优点 | 提高均一性,减少稀释,提高分析精度。 |
局限性 | 易受主要元素的粒度和矿物学影响。 |
自动化与手动 | 自动化系统适用于高通量实验室;手动压片机具有成本效益。 |
需要帮助制备用于 XRF 分析的压制颗粒吗? 立即联系我们的专家 获取量身定制的解决方案!