注塑成型和压力成型的区别在于其工艺、机制和应用。注塑成型是在高压下将熔融材料注入模腔,使其冷却并凝固成所需形状。另一方面,压力成型则结合使用热量和压力来塑造材料,通常无需注入熔融材料。这两种方法都广泛应用于制造业,但其适用性取决于材料、设计复杂性和生产要求。
要点说明:
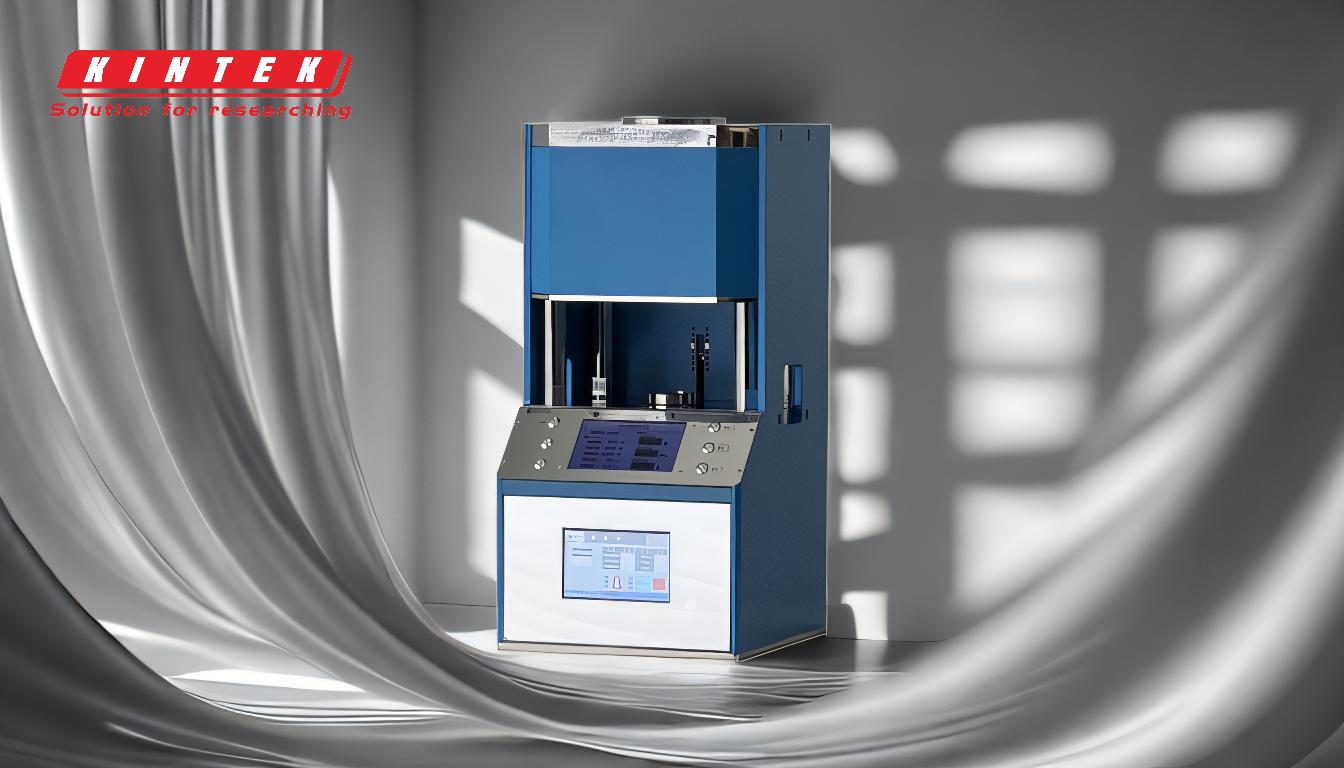
-
流程机制:
- 注塑:该工艺包括熔化材料(通常是塑料)并在高压下将其注入模具。材料填充模腔、冷却、凝固,形成最终产品。这是一种高度自动化的高效工艺,适合大批量生产。
- 压力成型:这种方法对材料(通常是热固性塑料或复合材料)施加热量和压力,使其成型。与注塑成型不同的是,材料并不一定熔化,而是在压力下软化成型。它通常用于需要在压力下固化或凝固的材料。
-
材料适用性:
- 注塑:最适用于可多次熔化和重塑的热塑性塑料。常见材料包括聚乙烯、聚丙烯和 ABS。
- 压力成型:适用于热固性材料,这些材料在成型过程中会发生化学变化,无法重新熔化。例如酚醛树脂和环氧树脂复合材料。
-
设计复杂性:
- 注塑:能够生产高度复杂、错综复杂、细节精细的零件。它适用于壁薄、有凹槽和复杂几何形状的零件。
- 压力成型:更适用于形状较简单和较大的零件。它通常用于需要高强度和耐用性的部件,如汽车部件或电气绝缘体。
-
产量:
- 注塑:自动化程度高,生产周期短,大规模生产效率高。对于生产数千或数百万个相同部件而言,它具有很高的成本效益。
- 压力成型:通常用于中低批量生产。与注塑成型相比,它的劳动密集程度更高,周期更长。
-
模具和设备:
- 注塑:需要专用设备,如注塑机和精密模具。初始设置成本较高,但单位成本会随着产量的增加而降低。
- 压力成型:利用设计用于承受高压和高温的压力机和模具。设备的复杂程度通常低于注塑机,但模具仍需要大量投资。
-
应用领域:
- 注塑:常用于汽车、消费品、医疗器械和电子产品等行业,用于生产外壳、容器和齿轮等部件。
- 压力成型:常用于需要高强度部件的行业,如航空航天、电气和重型机械。例如断路器、绝缘体和结构件。
总之,选择注塑成型还是压力成型取决于材料、设计要求、产量和应用。注塑成型适用于热塑性塑料制成的大批量复杂部件,而压力成型则更适用于热固性材料制成的高强度耐用部件。
汇总表:
指标角度 | 注塑成型 | 压力成型 |
---|---|---|
工艺机制 | 在高压下将材料熔化并注入模具。 | 利用热量和压力塑造材料,而无需注入熔融材料。 |
材料适用性 | 最适用于热塑性塑料(如聚乙烯、聚丙烯)。 | 最适合热固性材料(如酚醛树脂、环氧树脂复合材料)。 |
设计复杂性 | 适用于设计复杂、错综复杂的精细零件。 | 更适用于形状简单和较大的高强度部件。 |
大批量生产 | 大批量生产,生产周期短。 | 中低产量,生产周期较长。 |
工具和设备 | 需要专门的机器和精密模具。 | 使用专为高压和高温设计的压力机和模具。 |
应用领域 | 汽车、消费品、医疗器械、电子产品。 | 航空航天、电气、重型机械的高强度零件。 |
需要帮助选择适合您项目的成型工艺吗? 立即联系我们的专家!