双板模具是注塑成型中一种基本且广泛使用的设计。它由一个分模平面组成,将模具分成两半,通常称为型腔侧和型芯侧。这种设计可以在模具打开时有效地顶出成型零件和流道系统。双板模具的简易性和多功能性使其适用于各种应用,尤其是在将流道和浇口系统集成到分型面的多型腔设置中。这可确保在开模过程中,注塑件和流道系统同时顶出。
要点说明:
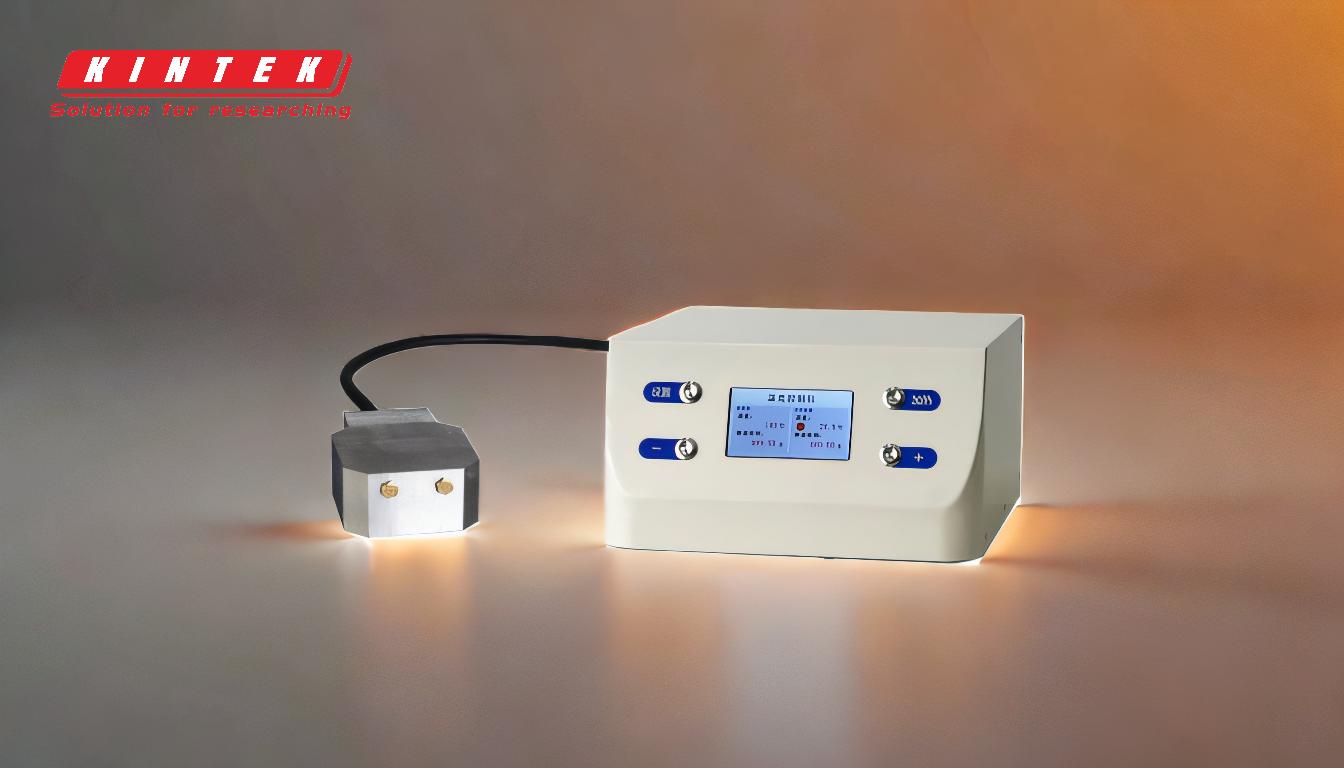
-
双板模具的基本结构:
- 双板模具由两个主要部分组成:型腔侧(固定)和型芯侧(活动)。
- 这两个半模在一个分模面相交,也就是模具在顶出过程中的分模界面。
- 这种简单的设计使其易于制造、维护和操作。
-
分模面的功能:
- 分模面对模具的运行至关重要,因为它能使模具顺利打开和关闭。
- 模具打开时,分模面将型腔和型芯分开,使成型零件和流道系统能够顶出。
- 在多型腔模具中,流道和浇口系统被设计在分模平面内,以确保它们与零件一起顶出。
-
流道和浇口系统:
- 流道是熔融塑料从注塑机流向模腔的通道。
- 浇口是熔融塑料进入模腔的入口。
- 在双板模具中,流道和浇口必须位于分模平面内,以确保在模具打开时将它们顶出。这对模具的自动运行和防止注塑过程中出现任何障碍至关重要。
-
顶出机构:
- 注塑件和流道系统的顶出由位于模具型芯一侧的顶针或顶板实现。
- 当模具打开时,顶出机构将零件和流道系统推出模具,从而实现连续生产周期。
- 顶出系统的设计对于确保零件无损脱模和流道系统完全脱离模具至关重要。
-
双板模具的优点:
- 简单: 双板模具设计简单,易于制造和维护。
- 成本效益高: 由于结构简单,与复杂的模具设计相比,双板模具通常更具成本效益。
- 多功能性: 从简单的单腔模具到复杂的多腔模具,它们的应用范围非常广泛。
- 操作简便: 单一的分模平面以及集成的流道和浇口系统使双板模具的操作相对简单,降低了生产过程中出错的可能性。
-
双板模具的应用:
- 两板模具通常用于生产各种塑料零件,包括消费品、汽车零部件和医疗器械。
- 它们尤其适用于对效率和成本效益要求较高的大批量生产。
- 在单个模具中包含多个型腔的能力使其成为生产大量相同零件的理想选择。
-
设计和制造的注意事项:
- 材料选择: 模具材料的选择对于确保耐用性和耐磨性至关重要,尤其是在大批量生产时。
- 冷却系统设计: 高效冷却对于保持稳定的零件质量和循环时间至关重要。要实现最佳冷却效果,必须对模具内的冷却通道进行适当设计。
- 浇口设计: 浇口的设计必须能让熔融塑料顺利流入型腔,同时尽量减少焊缝和气阱等缺陷。
- 顶出系统: 顶出系统必须足够坚固,能够同时顶出零件和流道系统,而不会造成损坏或变形。
总之,双板模具是一种多用途、经济高效的注塑成型解决方案,具有操作简单、易于使用、适用范围广等特点。其设计确保了注塑件和流道系统的高效顶出,使其成为生产塑料部件的重要工具。
汇总表:
主要方面 | 详细信息 |
---|---|
结构 | 由两半组成:腔体侧(固定)和芯材侧(活动)。 |
分模平面 | 使零件和流道系统顺利开模和顶出。 |
流道和浇口系统 | 与分型面集成,可同时顶出。 |
顶出机构 | 使用顶针/顶板将零件和流道推出,不会造成损坏。 |
优点 | 简单、成本效益高、用途广泛、易于操作。 |
应用领域 | 用于消费品、汽车、医疗设备和大批量生产。 |
设计考虑因素 | 材料选择、冷却系统、浇口设计和坚固的顶出系统。 |
了解双板模具如何优化您的注塑成型工艺--联系我们的专家 立即联系我们的专家 !