颗粒大小在热解过程中起着至关重要的作用,会影响传热、反应速率和最终产品(气体、液体和固体)的分布。较小的颗粒(通常不超过 2 毫米)传热更快、更均匀,热分解速度更快,热解油产量更高。另一方面,较大的颗粒可能会导致加热不均匀、反应速度变慢以及固体焦炭比例增大。颗粒大小还会影响热解过程的停留时间和效率,因此是优化生物质或废物转化为有价值产品的关键因素。
要点说明:
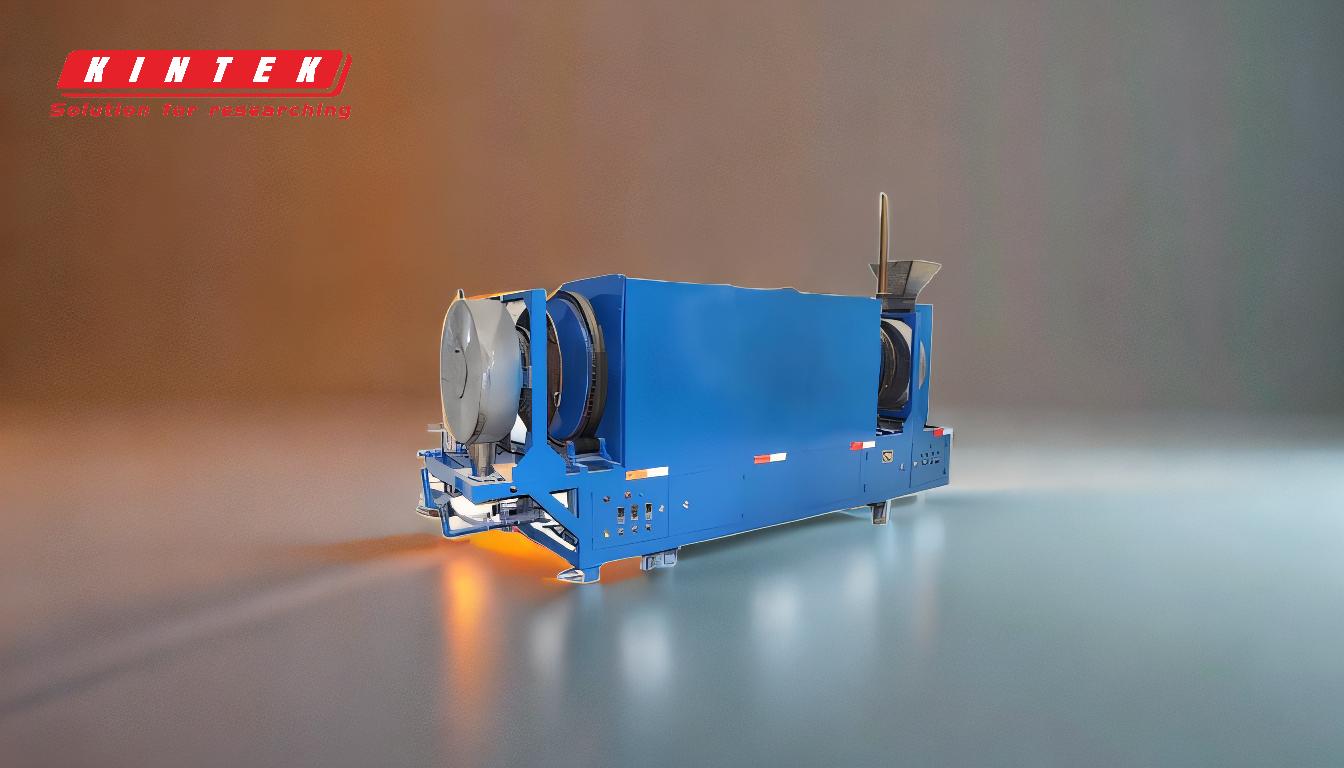
-
传热效率:
- 较小的颗粒(最多 2 毫米)提供了相对于其体积而言较大的表面积,使热量能够快速、均匀地传导到整个材料中。
- 这可确保整个颗粒迅速达到所需的热解温度,最大限度地降低不完全分解的风险。
- 较大的颗粒可能会因热量渗透较慢而导致加热不均匀,并有可能使颗粒的核心部分处理不当。
-
反应速率和热分解:
- 较小的颗粒由于表面积增大,热传导效率高,因此分解速度较快。
- 由于挥发性化合物释放得更快更有效,因此分解速度越快,热解油的产量就越高。
- 较大颗粒的分解速度较慢,可能会因热解不完全而导致固体炭的比例较高。
-
产品分布:
- 较小的颗粒有利于产生热解油和不凝性气体,因为快速分解会释放出更多的挥发性物质。
- 较大的颗粒往往会产生更多的固体炭,因为分解速度较慢,材料的碳化程度较高。
- 颗粒大小也会影响固体残渣的质量,较小的颗粒通常会产生更细、更均匀的炭。
-
停留时间:
- 较小的颗粒在热解室中需要较短的停留时间,因为它们分解得更快。
- 这可以提高工艺的整体效率,降低能耗,提高产量。
- 较大的颗粒可能需要较长的停留时间,这会导致能源成本增加和工艺效率降低。
-
工艺优化:
- 大多数热解技术设计用于处理小颗粒(最多 2 毫米),以最大限度地提高传热和反应速率。
- 为了减小原料的粒度,通常需要进行粉碎或研磨等预处理步骤。
- 粒度的选择应根据具体的热解技术和所需的产品分布情况而定。
-
原料成分和物理结构:
- 粒度与含水量、温度和加热速率等其他因素相互作用,影响热解过程。
- 例如,在生物质热解过程中,含水量低、加热速率高的较小颗粒往往会产生更多的液体和气体产品。
- 在废物热解(如轮胎)中,粉碎过程中去除强化材料(如钢和纤维)也会影响颗粒大小和热解结果。
-
实际考虑因素:
- 为达到理想粒度而进行的预处理会增加热解工艺的总体成本和复杂性。
- 最佳粒度可能因原料类型(如木材、农业废料、塑料)和使用的特定热解技术而异。
- 平衡粒度与其他工艺参数(如温度、停留时间)对于获得理想的产品产量和质量至关重要。
通过仔细控制原料的粒度,热解操作人员可以优化工艺,最大限度地提高所需产品(油、气或炭)的产量,同时最大限度地减少能耗和处理时间。因此,粒度是热解系统设计和运行中的一个关键因素。
汇总表:
指标 | 小颗粒(≤2 毫米) | 大颗粒 |
---|---|---|
传热 | 传热更快、更均匀 | 较慢,加热不均匀 |
反应速率 | 分解速度更快 | 分解速度较慢 |
产品分布 | 热解油气产量更高 | 产生更多固体炭 |
停留时间 | 停留时间更短 | 更长的停留时间 |
工艺效率 | 效率更高,能耗更低 | 效率低,能耗高 |
使用正确的粒度优化热解工艺 立即联系我们的专家 获取量身定制的解决方案!