Definition and Overview of Cold Isostatic Pressing
Table of Contents
- Definition and Overview of Cold Isostatic Pressing
- Advantages of Cold Isostatic Pressing
- Uniform Density
- Uniform Strength
- Versatility
- Corrosion Resistance
- Improved Mechanical Properties
- Applications in Powder Metallurgy
- Production of Refractory Metals
- Preparation for Sintering
- 6 Key Advantages of Cold Isostatic Pressing versus Uniaxial Pressing
- Advantages of Using Hot Isostatic Pressing Tools
- Cold Isostatic Pressing Technical Considerations
- Cold Isostatic Pressing vs. Hot Isostatic Pressing
- Advantages of Cold Isostatic Pressing for ITO Targets
- Types of Cold Isostatic Pressing
- Application of Dry Bag Isostatic Pressing in Tungsten Carbide Production
Explanation of cold isostatic pressing
Cold Isostatic Pressing (CIP), also known as cold isostatic compaction, is a materials processing technique that involves subjecting a material to uniform pressure from all sides. This is achieved by immersing the material in a high-pressure fluid medium and applying hydraulic pressure. CIP is particularly effective for shaping and consolidating powdered materials, allowing for the creation of intricate shapes and achieving high green density.
Comparison with other pressing methods
In the realm of materials processing, CIP stands out as a unique method due to its ability to apply pressure uniformly from all directions. This sets it apart from other pressing methods, such as hot isostatic pressing (HIP), which is conducted at high temperatures. While HIP and CIP share the goal of enhancing material properties, they do so under different conditions, each offering its own advantages.
Basic principles of cold isostatic pressing
The basic principle of cold isostatic pressing involves placing the material in a flexible mold, which is then immersed in a high-pressure fluid medium, typically water or oil. Hydraulic pressure is applied to the fluid, which in turn applies uniform pressure to the material from all sides. This pressure helps to shape and consolidate the material, resulting in a denser and more uniform structure.
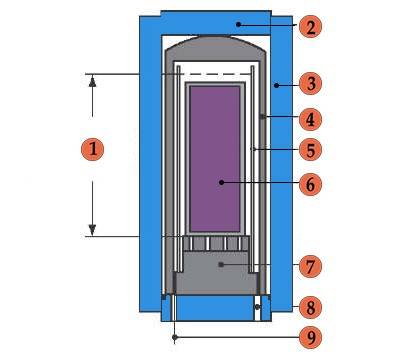
Use cases for cold isostatic pressing
Cold isostatic pressing is commonly used in various industries for a range of applications. Some of the key use cases include:
-
Shaping and consolidating powdered materials: CIP is particularly effective in shaping and consolidating powdered materials, allowing for the creation of complex geometries and achieving high green density.
-
Producing large and complex spare parts: CIP is often used to produce very large and complex spare parts where the initial cost of alternative manufacturing methods is unjustified.
-
Ensuring uniform density distribution: The isostatic pressing technique, including CIP, enables the achievement of a uniform density distribution in the material, which is essential for many applications.
In summary, cold isostatic pressing is a materials processing technique that involves subjecting a material to uniform pressure from all sides. It offers unique advantages in shaping and consolidating powdered materials, creating intricate shapes, and achieving high green density. By understanding the basic principles and use cases of cold isostatic pressing, businesses can make informed decisions about utilizing this technique in their manufacturing processes.
Advantages of Cold Isostatic Pressing
Uniform Density
Cold isostatic pressing (CIP) ensures that materials have a uniform density. This is because the pressure used in CIP reaches every part of the material with equal magnitude. As a result, there will be uniform shrinkage when the material undergoes other processes such as sintering.
Uniform Strength
CIP compacts materials using equal pressure in all directions, resulting in materials with uniform strength. This uniform strength makes the materials more efficient and reliable than those without uniform strength.
Versatility
CIP can be used to produce difficult shapes that cannot be achieved by other methods. It also allows for the production of large-sized materials, with the only limitation being the size of the pressure vessel.
Corrosion Resistance
Materials produced through CIP have improved corrosion resistance, leading to a longer lifespan compared to most other materials. This makes them ideal for applications where corrosion is a concern.
Improved Mechanical Properties
CIP improves the mechanical properties of materials, such as ductility and strength. This enhancement makes the materials more durable and better suited for their intended applications.
Applications in Powder Metallurgy
CIP is commonly used in powder metallurgy for the compacting step that precedes sintering. It is particularly effective in producing complex shapes and dimensions.
Production of Refractory Metals
CIP is utilized in the production of refractory metals like tungsten, molybdenum, and tantalum. These metals have high melting points and are resistant to wear and tear, making them suitable for various industrial applications.
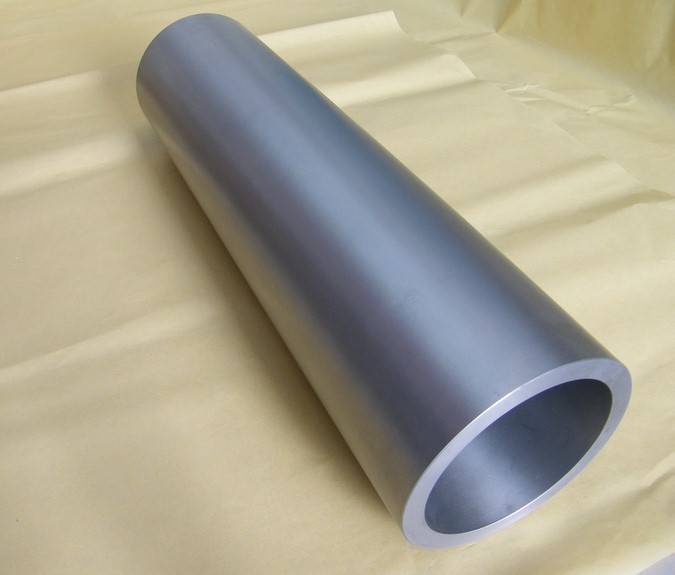
Preparation for Sintering
CIP is often performed just before the sintering process. The high green strength of cold isostatic pressed products allows for faster sintering compared to other materials.
6 Key Advantages of Cold Isostatic Pressing versus Uniaxial Pressing
- More uniform product properties, greater homogeneity, and more precise control of the finished product dimensions
- Greater flexibility in the shape and size of the finished product
- Longer aspect ratios possible, allowing for long thin pellets
- Improved compaction of the powder, leading to improved densification
- Ability to process materials with different characteristics and shapes
- Reduced cycle times and improved productivity
Advantages of Using Hot Isostatic Pressing Tools
- Allows for more efficient production by reducing manual rework and scrap material loss
- Helps reach precise tolerances, eliminating the need for secondary machining
- Helps consolidate powder alloys into specific parts and components
- Enables bonding of dissimilar metals and materials to create cost-effective components
Cold Isostatic Pressing Technical Considerations
Compared to cold pressing, isostatic compaction applies pressure uniformly over the entire surface of the mold, resulting in more uniform densities. Die-wall friction is eliminated, leading to higher pressed densities and eliminating issues associated with lubricant removal. Isostatic compaction provides increased and more uniform density, making it suitable for brittle or fine powders and allowing for more complex shapes than uniaxial pressing.
Cold Isostatic Pressing vs. Hot Isostatic Pressing
Cold isostatic pressing is advantageous for producing parts where the high initial cost of pressing dies cannot be justified or when very large or complex compacts are needed. Hot isostatic pressing is similar to cold isostatic pressing but is conducted at high temperatures. Both methods offer benefits in terms of uniform density distribution and reducing pressing flaws.
Advantages of Cold Isostatic Pressing for ITO Targets
- Suitable for pressing large-sized powder products
- Produces powder products with high density and uniformity
- Does not require the addition of lubricants
- Low production cost and suitable for mass production
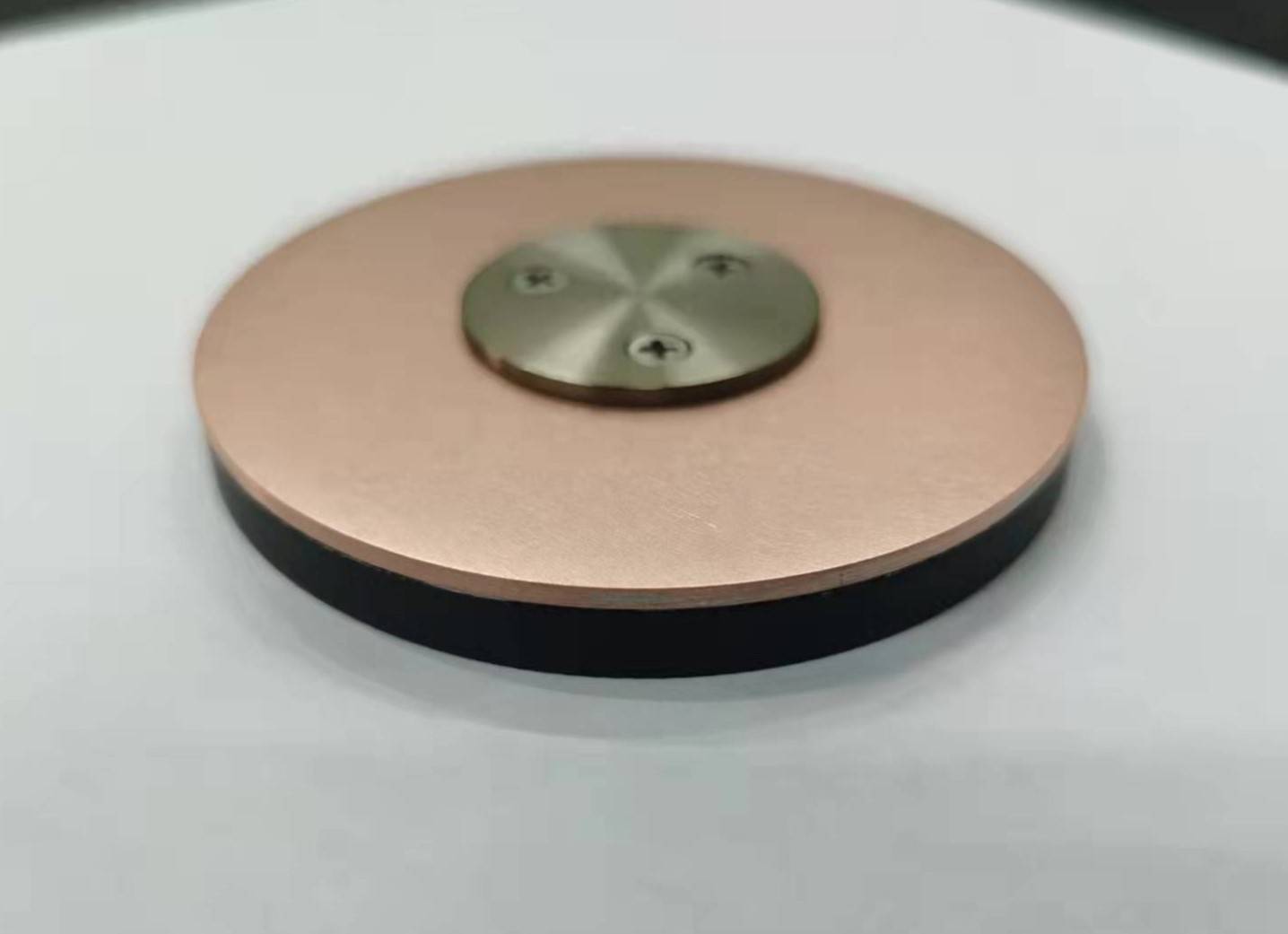
Cold isostatic pressing offers numerous advantages in terms of uniformity, versatility, improved mechanical properties, and corrosion resistance. It finds applications in various industries, including powder metallurgy, production of refractory metals, and automotive manufacturing. Whether used in cold or hot form, isostatic pressing tools provide efficiency and cost-effectiveness in production processes.
Types of Cold Isostatic Pressing
Wet Bag Isostatic Pressing
In the wet bag process, the powder material is enclosed in a flex mold bag, which is submerged into a high-pressure liquid in a pressure vessel. Isostatic pressure is then applied to the outer surfaces of the mold to compress the powder into a desired shape. This method is ideal for multi-shape and small to large quantity production, as well as the pressing of large products. It is also suitable for experimental research and small batch production, as it can simultaneously press more than two different shapes of parts in one high-pressure cylinder, resulting in a short production process and low cost.
Dry Bag Isostatic Pressing
In the dry bag process, the powder is added to an integrated mold within the pressure vessel. The mold is then sealed, pressure is applied, and the desired part is ejected. This method circumvents the immersion step involved in wet bag isostatic pressing, making automation easier. It is suited for pressing relatively long runs of compacts at high production rates.
Comparison between Wet and Dry Bag Isostatic Pressing
Both wet bag and dry bag isostatic pressing methods have their advantages. Wet bag isostatic pressing offers strong applicability, making it suitable for experimental research and small batch production. It allows for the simultaneous pressing of multiple different shapes of parts in one high-pressure cylinder, resulting in large and complex parts production. On the other hand, dry bag isostatic pressing lends itself to automation and is well-suited for pressing relatively long runs of compacts at high production rates.
Overall, the decision between wet bag and dry bag isostatic pressing depends on the specific goals of your project and the characteristics of the materials involved.
Application of Dry Bag Isostatic Pressing in Tungsten Carbide Production
Use of dry bag isostatic pressing in manufacturing tungsten carbide rods and bars
Dry bag isostatic pressing is a highly efficient method used in the production of tungsten carbide rods and bars. This technique involves building up pressure by means of a high-pressure pump, which is then transmitted radially to an elastic pressing mold filled with WC-Co powder. The major advantage of using dry bag presses is the possibility of automation, allowing for cost-effective mass or semi-mass production of carbide articles with complex geometries.
By utilizing dry isostatic pressing, manufacturers are able to produce almost net-shape hollow green compacts with precise outer and internal dimensions. This significantly reduces the amount of machining required, leading to a reduction in swarf generation. The quality of the WC-Co powder and the design of the pressing mold play crucial roles in achieving highly effective fabrication of carbide green compacts.
Limitations and considerations of dry bag isostatic pressing in tungsten carbide production
While dry bag isostatic pressing offers numerous benefits, it does have some limitations and considerations to be aware of. This method is most suitable for producing relatively small carbide articles with axisymmetric geometry. It may not be as effective for larger and more complex parts.
Additionally, the cost of implementing a dry bag isostatic pressing system can be higher compared to other manufacturing methods. Companies considering this technique should carefully evaluate their production requirements and weigh the potential benefits against the investment costs.
Post-pressing processes for tungsten carbide
After the dry bag isostatic pressing process, there are several post-pressing processes that can be employed to further enhance the properties of tungsten carbide. These processes include sintering, heat treatment, and finishing.
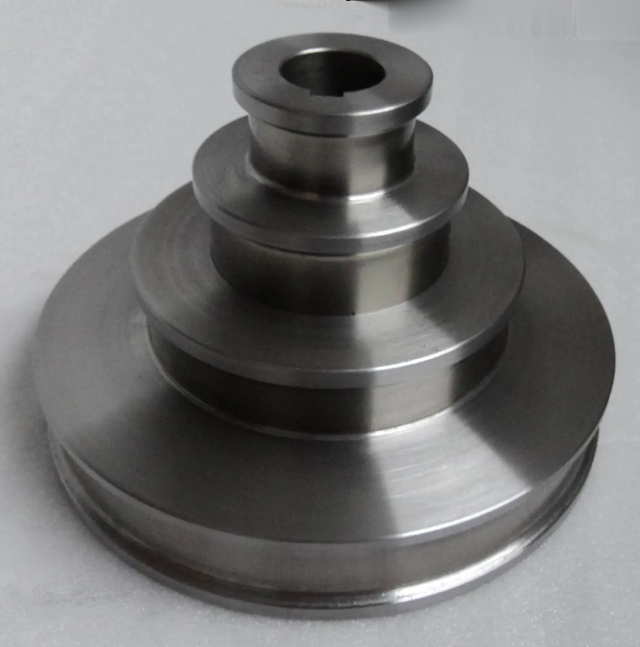
Sintering involves subjecting the pressed tungsten carbide compacts to high temperatures in a controlled atmosphere. This process helps to bond the particles together, resulting in a denser and stronger material.
Heat treatment is often used to optimize the mechanical properties of tungsten carbide. It involves heating the material to specific temperatures and then cooling it at a controlled rate. This process can improve hardness, toughness, and wear resistance.
Finally, finishing processes such as grinding, polishing, and coating may be applied to achieve the desired surface finish and dimensional accuracy of the tungsten carbide products.
In conclusion, dry bag isostatic pressing is a valuable technique in the production of tungsten carbide rods and bars. It offers automation capabilities and the potential for cost-effective mass production. However, companies should consider the limitations and evaluate their specific production requirements before implementing this method. Additionally, post-pressing processes such as sintering, heat treatment, and finishing play vital roles in enhancing the properties of tungsten carbide.
If you are interested in this product you can browse our company website: https://kindle-tech.com/product-categories/isostatic-press, we always insist on the principle of quality first. During the production process, we strictly control every step of the process, using high quality materials and advanced production technology to ensure the stability and durability of our products. to ensure that their performance meets the highest standards. We believe that only by providing customers with excellent quality can we win their trust and long-term cooperation.
联系我们获取免费咨询
KINTEK LAB SOLUTION 的产品和服务得到了世界各地客户的认可。我们的员工将竭诚为您服务。如需免费咨询,请与我们的产品专家联系,以找到最适合您应用需求的解决方案!