与其他沉积方法相比,溅射技术具有多种优势,因此成为各种应用的首选。这些优势包括:能在较低温度下对多种材料进行镀膜、分子级精度、可重复性和更简单的流程自动化。溅射的成本相对较低,可以沉积熔点极高、难以蒸发的材料。溅射薄膜的成分与源材料非常接近,而且这些薄膜通常与基底有更好的附着力。此外,溅射技术无需维护,适用于超高真空应用,并支持外延生长等先进工艺。即使在低温条件下,该技术也能实现纯净、精确的原子级薄膜沉积,薄膜更均匀,堆积密度更高。
要点说明:
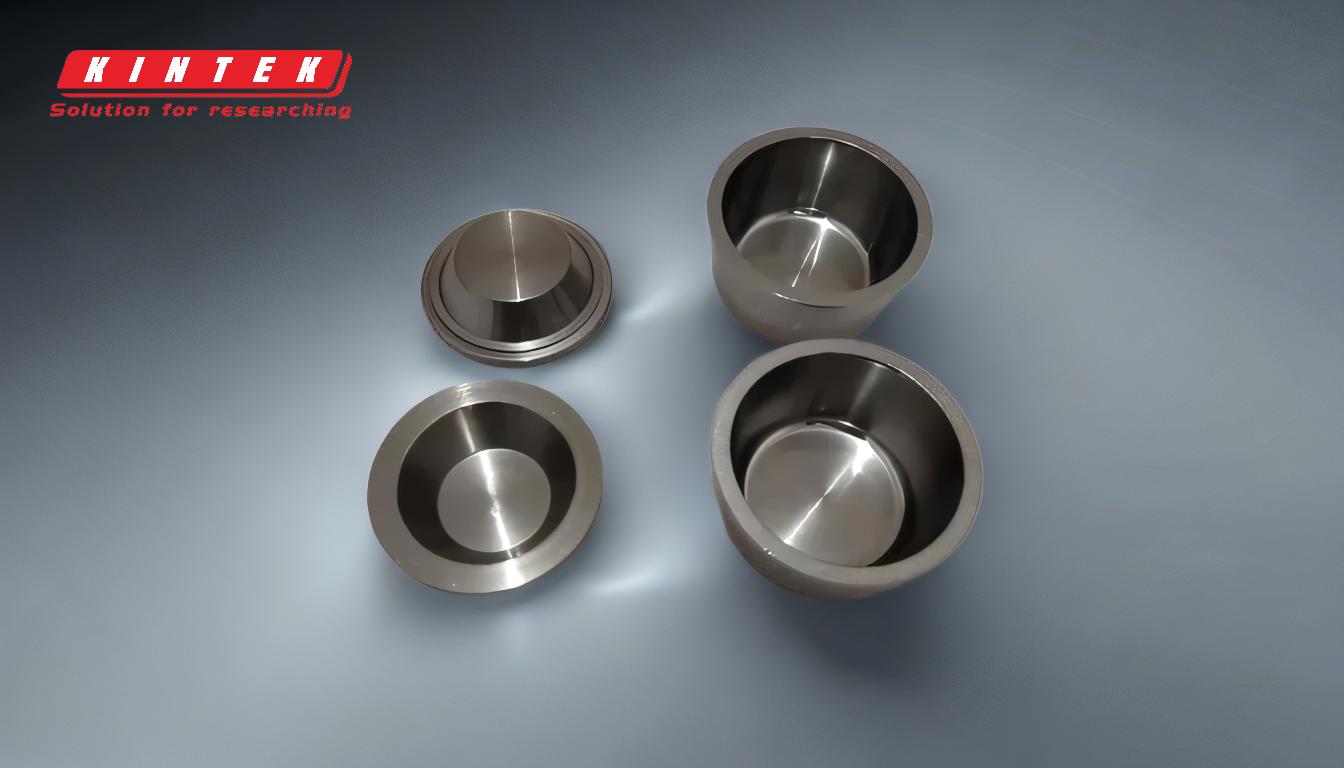
-
材料涂层的多样性:
- 多种材料:溅射可以在较低温度下为各种材料涂层,包括塑料、有机物、玻璃和金属。这种多功能性使其适用于各种应用。
- 高熔点材料:溅射可以沉积熔点极高的材料,而这些材料用其他方法很难或根本无法蒸发。
-
精度和控制:
- 分子级精度:溅射技术具有分子级精度,可在材料之间形成原始界面,并可通过精确控制工艺参数调整薄膜特性。
- 原子级薄膜沉积:该技术可实现纯净、精确的原子级薄膜沉积,从而获得高质量的薄膜。
-
可重复性和自动化:
- 可重复性:溅射沉积具有很高的可重复性,这对多批次薄膜质量的一致性至关重要。
- 流程自动化更简单:与电子束或热蒸发等方法相比,溅射更容易实现自动化,从而降低了沉积过程的复杂性和人为失误的可能性。
-
成本效益:
- 相对便宜:与其他沉积工艺相比,溅射沉积的成本相对较低,因此在许多应用中都是一种具有成本效益的选择。
-
薄膜质量和附着力:
- 更好的附着力:与蒸发材料相比,溅射出的原子动能更高,因此薄膜与基底的附着力更好。
- 均匀的薄膜:即使在低温条件下,溅射也能产生更均匀、堆积密度更高的薄膜。
-
与反应性气体的兼容性:
- 反应沉积:溅射技术可以很容易地将等离子体中激活的活性气体种类纳入其中,从而形成所需成分的氧化物或氮化物薄膜层。
-
低维护和高真空兼容性:
- 免维护:溅射是一种免维护工艺,可减少停机时间和运行成本。
- 超高真空应用:该技术适用于超高真空应用,这对某些高精度工艺至关重要。
-
先进工艺:
- 外延生长:溅射支持外延生长等先进工艺,而外延生长对于制造高质量的晶体薄膜至关重要。
-
动能和沉积方向:
- 更高的动能:与蒸发材料相比,溅射出的原子具有更高的动能,从而提高了薄膜的附着力和质量。
- 灵活的沉积方向:溅射既可自下而上进行,也可自上而下进行,为沉积过程提供了灵活性。
-
腔室体积小:
- 紧凑型设置:溅射沉积室的体积可以很小,这对某些应用是有利的,可以减少沉积系统的总体占地面积。
总之,溅射技术具有一系列综合优势,在许多情况下都优于其他沉积方法。溅射技术的多功能性、精确性、成本效益以及生产具有出色附着力和均匀性的高质量薄膜的能力,都是其在各行各业得到广泛应用的关键因素。
汇总表:
优势 | 说明 |
---|---|
多功能性 | 可涂覆多种材料,包括高熔点物质。 |
精确度 | 原始界面和原子级沉积的分子级精度。 |
可重复性 | 确保多个批次的薄膜质量保持一致。 |
成本效益 | 与其他沉积方法相比,成本相对较低。 |
薄膜质量 | 更好的附着力、均匀的薄膜和更高的包装密度。 |
低维护 | 免维护工艺,降低运营成本。 |
先进工艺 | 支持高质量薄膜的外延生长和反应沉积。 |
灵活沉积 | 可以自下而上和自上而下两种方向进行沉积。 |
结构紧凑 | 腔体体积小,减少系统占用空间。 |
准备好在您的应用中利用溅射技术的优势了吗? 今天就联系我们 了解更多信息!