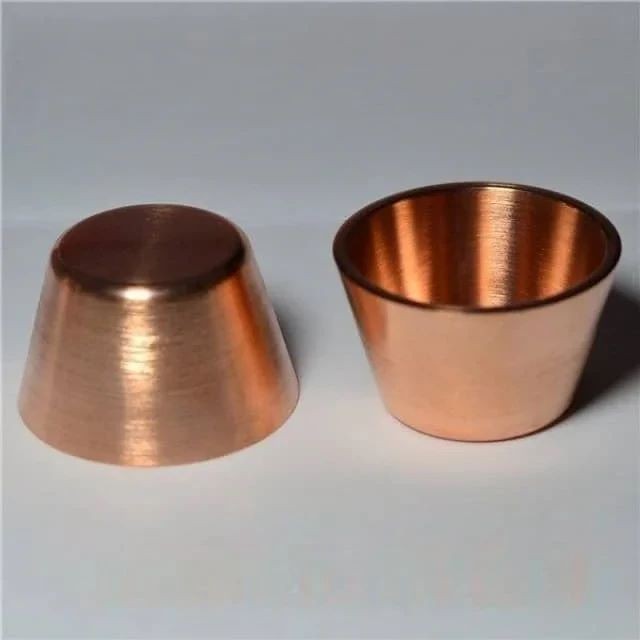
为什么选择我们
可靠的合作伙伴简易的订购流程、优质的产品和专业的支持,助力您的业务成功。
简介
电子束蒸发镀膜无氧铜坩埚是一种用于沉积薄膜的实验室设备。它使用电子束蒸发材料,然后将其沉积在基底上。该工艺用于制造金属、电介质和其他材料的薄膜。
电子束蒸发涂层无氧铜坩埚由无氧铜制成,具有高导热性和抗氧化性。因此非常适合高温应用。坩埚还采用水冷技术,以防止过热。
电子束蒸发涂层无氧铜坩埚是一种多功能设备,可用于多种应用。它通常用于半导体行业,但也可用于其他行业,如光学和医疗行业。
应用
电子束蒸发镀膜是指在薄膜沉积过程中使用电子束蒸发材料,然后将其凝结在基底上形成薄膜的过程。使用电子束蒸发技术时,应使用无氧铜坩埚来维持无氧或缺氧环境,以最大限度地降低蒸发过程中的氧污染风险。这有助于确保沉积出高质量的薄膜,而不会发生不必要的化学反应或氧化。在处理敏感材料或沉积纯度要求较高的薄膜时,通常首选无氧铜坩埚。
- 半导体工业:集成电路、半导体器件和微电子的制造。
- 光学和光子学:用于透镜、反射镜、滤镜、波导和其他光学元件的光学镀膜和薄膜。
- 太阳能:电子束蒸发用于制造薄膜太阳能电池,如 CIGS(铜铟镓硒)和 CdTe(碲化镉)太阳能电池。
- 显示技术:电子束蒸发可用于生产各种类型显示器的薄膜,包括 LCD(液晶显示器)、OLED(有机发光二极管)和微型显示器技术。
- 传感器和电子产品的制造:电子束蒸发用于生产传感器、电子器件和集成电路用薄膜。
技术规格
外径和高度 | 35*17 毫米 | 40*17 毫米 | 45*22 毫米 | 50*25 毫米 |
我们展示的坩埚有不同尺寸,也可根据要求定制尺寸。
特点
电子束蒸发镀膜无氧铜坩埚具有四孔炉膛,最多可容纳四种源材料,可在不破坏真空的情况下连续沉积四层材料。这样就可以方便地从不同的目标材料中涂覆几层不同的涂层,轻松适应各种升离掩蔽技术。
坩埚是水冷却的,以防止通过热能加热,直接加热源材料消除了基底受热损坏的风险。这使得电子束蒸发技术非常适合高温和耐磨性要求较高的应用领域,如航空航天、汽车和切削工具行业。
电子束蒸发还可用于激光光学、太阳能电池板、眼镜和建筑玻璃等光学薄膜,使其具有所需的导电性、反射性和透射性。
FAQ
什么是物理气相沉积(PVD)?
什么是磁控溅射?
用于沉积薄膜的方法有哪些?
为什么选择磁控溅射?
什么是薄膜沉积设备?
使用蒸发舟有哪些优势?
蒸发坩埚常用的材料有哪些?
用于薄膜沉积的材料有哪些?
薄膜沉积通常使用金属、氧化物和化合物作为材料,每种材料都有其独特的优缺点。金属因其耐用性和易于沉积而受到青睐,但价格相对昂贵。氧化物非常耐用,可耐高温,并可在低温下沉积,但可能比较脆,难以操作。化合物具有强度和耐久性,可在低温下沉积,并可定制以显示特定性能。
薄膜涂层材料的选择取决于应用要求。金属是热传导和电传导的理想材料,而氧化物则能有效提供保护。可根据具体需求定制化合物。最终,特定项目的最佳材料将取决于应用的具体需求。
什么是薄膜沉积技术?
蒸发舟的典型使用寿命是多久?
使用蒸发坩埚有哪些优势?
实现最佳薄膜沉积的方法有哪些?
要获得具有理想特性的薄膜,高质量的溅射靶材和蒸发材料至关重要。
溅射靶材或蒸发材料的纯度起着至关重要的作用,因为杂质会导致生成的薄膜出现缺陷。晶粒大小也会影响薄膜的质量,晶粒越大,薄膜的性能越差。
要获得最高质量的溅射靶材和蒸发材料,选择纯度高、晶粒度小、表面光滑的材料至关重要。
薄膜沉积的用途
氧化锌薄膜
氧化锌薄膜可应用于热学、光学、磁学和电气等多个行业,但其主要用途是涂层和半导体器件。
磁性薄膜
磁性薄膜是电子、数据存储、射频识别、微波设备、显示器、电路板和光电子技术的关键元件。
光学薄膜
光学镀膜和光电子技术是光学薄膜的标准应用。分子束外延可以生产光电薄膜设备(半导体),外延薄膜是一个原子一个原子地沉积到基底上的。
聚合物薄膜
聚合物薄膜可用于存储芯片、太阳能电池和电子设备。化学沉积技术(CVD)可精确控制聚合物薄膜涂层,包括一致性和涂层厚度。
薄膜电池
薄膜电池为植入式医疗设备等电子设备提供动力,由于薄膜的使用,锂离子电池的发展突飞猛进。
薄膜涂层
薄膜涂层可增强各行业和技术领域目标材料的化学和机械特性。
薄膜太阳能电池
薄膜太阳能电池对于太阳能产业至关重要,它可以生产相对廉价的清洁电力。光伏系统和热能是两种主要的适用技术。
使用薄膜沉积设备有哪些优势?
蒸发舟可以重复使用吗?
应如何处理和维护蒸发坩埚?
影响薄膜沉积的因素和参数
沉积速率:
薄膜的生成速率(通常以厚度除以时间来衡量)对于选择适合应用的技术至关重要。对于薄膜而言,适度的沉积速率就足够了,而对于厚膜而言,快速沉积速率则是必要的。在速度和精确薄膜厚度控制之间取得平衡非常重要。
均匀性:
薄膜在基底上的一致性称为均匀性,通常指薄膜厚度,但也可能与折射率等其他属性有关。
填充能力:
填充能力或台阶覆盖率是指沉积工艺对基底形貌的覆盖程度。所使用的沉积方法(如 CVD、PVD、IBD 或 ALD)对台阶覆盖率和填充有重大影响。
薄膜特性:
薄膜的特性取决于应用要求,可分为光子、光学、电子、机械或化学要求。大多数薄膜必须满足一个以上类别的要求。
制程温度:
薄膜特性受制程温度的影响很大,这可能受到应用的限制。
损坏:
每种沉积技术都有可能损坏沉积在其上的材料,而较小的特征更容易受到制程损坏。污染、紫外线辐射和离子轰击都是潜在的损坏源。了解材料和工具的局限性至关重要。
选择薄膜沉积设备时应考虑哪些因素?
如何选择合适的蒸发舟材料?
操作薄膜沉积设备有哪些安全注意事项?
4.8
out of
5
Prompt delivery. Well-packaged and protected.
4.9
out of
5
Amazing quality, works like a charm. Worth every penny!
4.7
out of
5
Durable and long-lasting. Highly recommended!
4.6
out of
5
Great value for money. Exceeded my expectations.
4.8
out of
5
Top-notch quality. Highly satisfied with my purchase.
4.9
out of
5
State-of-the-art technology. Works flawlessly.
4.7
out of
5
Easy to use and maintain. Made my work so much easier.
4.6
out of
5
Reliable and efficient. Highly recommend it to others.
4.8
out of
5
Great addition to my lab. Highly satisfied with the results.
4.9
out of
5
Excellent product. Meets all my requirements.
4.7
out of
5
User-friendly interface. Makes my work more efficient.
获取报价
我们的专业团队将在一个工作日内回复您。请随时与我们联系!
相关产品
相关文章
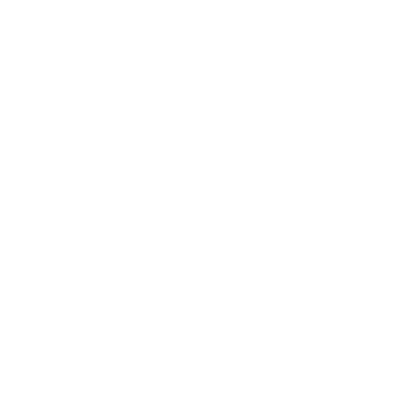
薄膜沉积中蒸发和溅射技术的比较研究
最常用的两种薄膜沉积技术是蒸发和溅射。
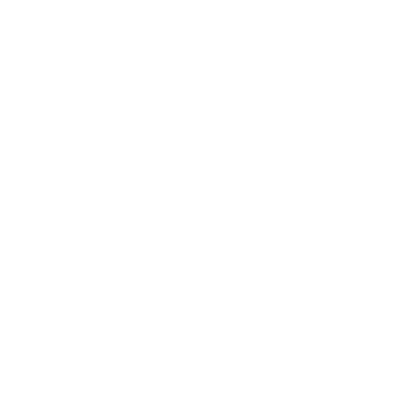
了解电化学电极的电沉积作用
电沉积是通过电流在表面沉积金属或非金属材料的过程。
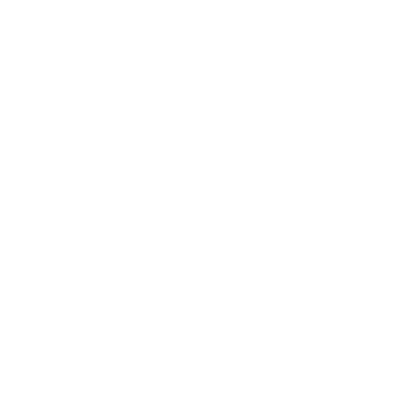
电子束蒸发涂层技术和材料选择
深入探讨电子束蒸发涂层技术的原理和应用,包括材料选择和各种应用领域。
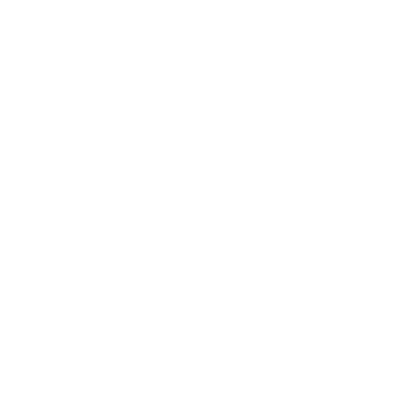
了解电解槽及其在铜净化和电镀中的作用
电解槽在铜净化和电镀等各种工业流程中发挥着至关重要的作用。这些电池利用外部电源驱动化学反应,从而分解物质。在电解过程中,电流通过含有离子的液体或溶液,使其分解。
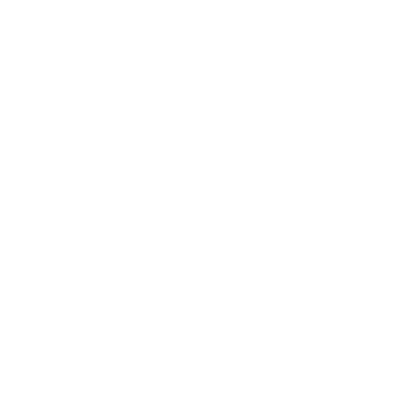
利用电解槽进行涂层评估的先进技术
探索使用电解槽进行涂层评估的综合指南,涵盖电镀、溶胶-凝胶法和湿化学技术。加深对金属镀层性能和应用的了解。
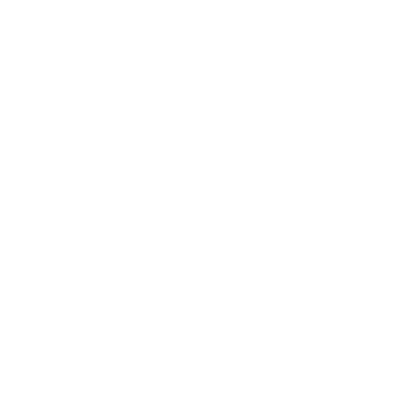
真空镀膜中的电子束蒸发技术
深入了解电子束蒸发及其在真空镀膜工艺中的类型、优点和缺点。
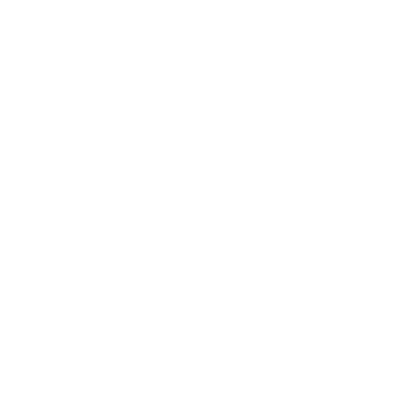
电子束蒸发涂层:原理、特点和应用
深入分析电子束蒸发涂层技术及其优缺点和在薄膜制造中的应用。
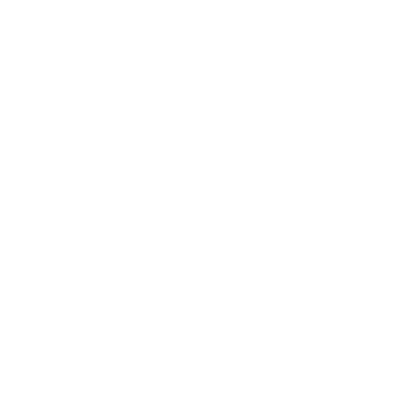
电子束蒸发:先进的薄膜制造
探讨电子束蒸发在薄膜生产中的技术和应用。
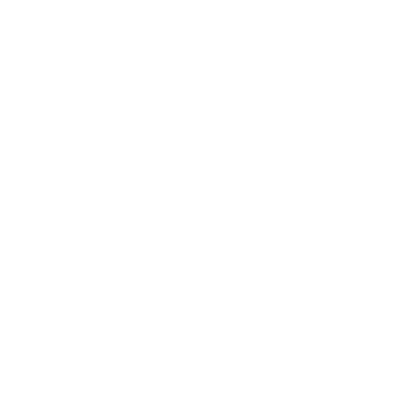
真空熔炼炉:真空感应熔炼综合指南
了解真空感应熔炼炉的复杂性、组件、操作、优势和应用。探索这些熔炉如何彻底改变金属加工工艺并实现优异的材料性能。
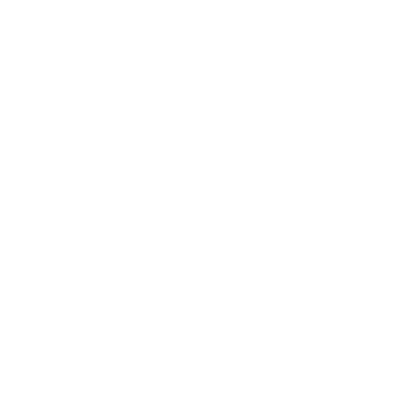
电子束蒸发涂层:优缺点与应用
深入了解电子束蒸发涂层的优缺点及其在工业中的各种应用。
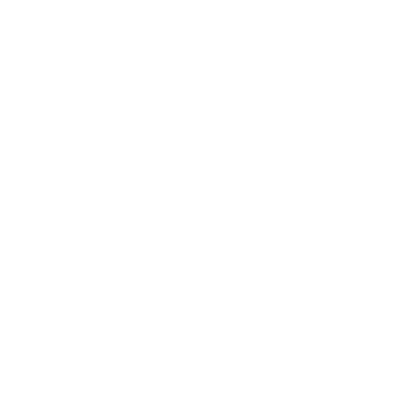
了解电极和电化学电池
电极是电流进出电解质的点。它是一种导体,用于与电路中的非金属部分连接。电极可以由金、铂、碳、石墨或金属等材料制成。它们是电化学电池中发生氧化还原反应的表面。电极有不同的类型,包括阳极和阴极。
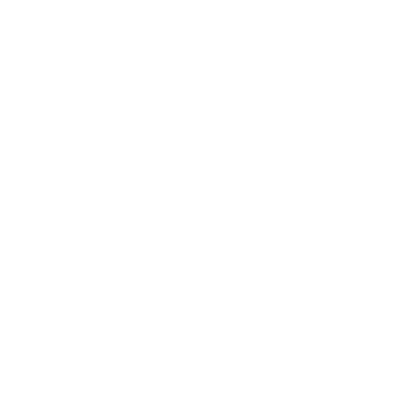
选择真空镀膜材料:关键因素和考虑因素
根据应用、材料特性、沉积方法、经济性、基底兼容性和安全性选择正确真空镀膜材料的指南。