石墨烯剥离是生产高质量石墨烯的关键过程,可通过多种方法实现,每种方法都有其自身的优势和局限性。主要技术包括机械剥离、液相剥离和化学气相沉积(CVD)。机械剥离通常被称为 "苏格兰胶带法",是生产高质量石墨烯薄片的一种简单而有效的方法,但这种方法无法在工业应用中推广。另一方面,液相剥离法是将石墨分散在溶剂中,然后施加能量(如超声波)来分离石墨层。这种方法的可扩展性较高,但通常会导致石墨烯质量较低。CVD 是一种自下而上的方法,涉及在基底(通常是铜或镍)上生长石墨烯,被认为是最有希望生产出大面积、高质量石墨烯的方法。每种方法都有其自身的一系列挑战,如产量、质量和可扩展性,必须根据预期应用加以考虑。
要点说明:
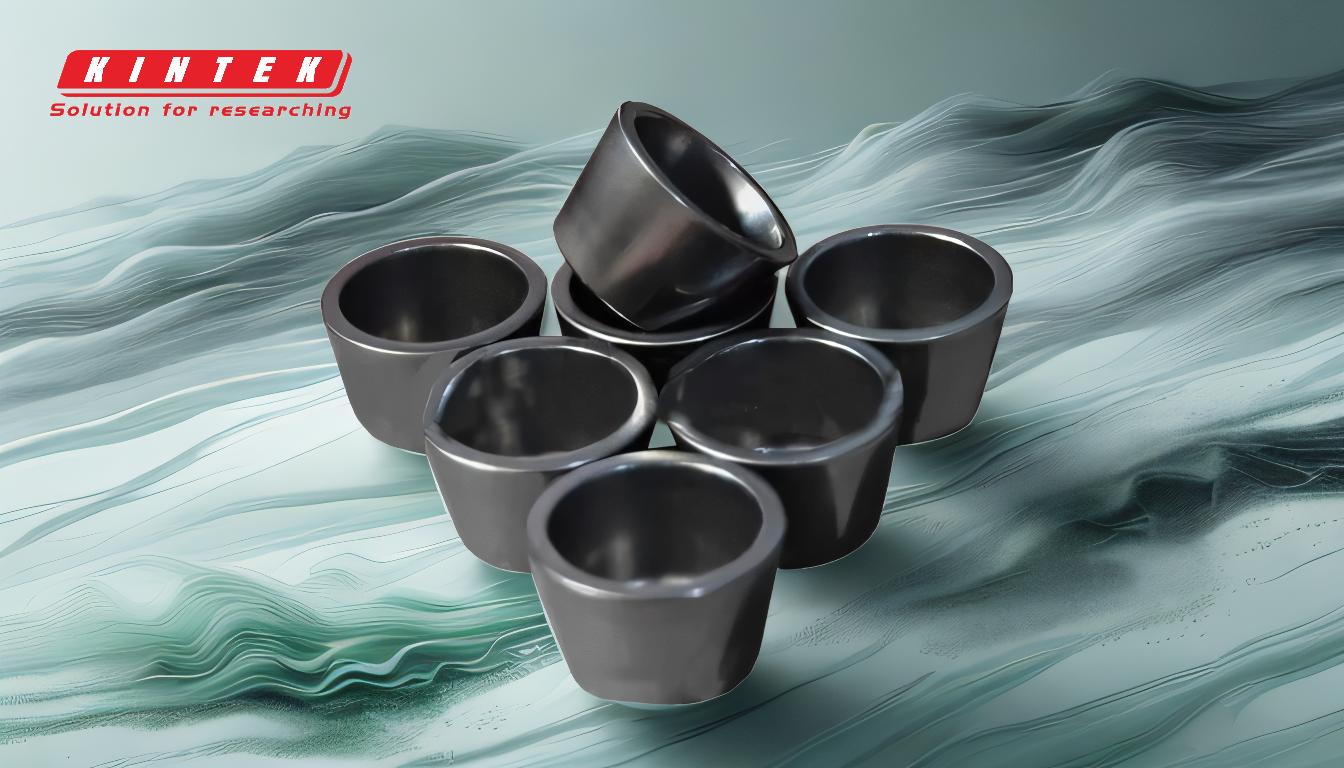
-
机械去角质
- 工艺:机械剥离法,又称 "苏格兰胶带法",是指使用胶带从石墨晶体上剥离石墨烯层。这种方法简单直接,可以生产出高质量的石墨烯薄片。
-
优点:
- 生产出缺陷极少的高质量石墨烯。
- 操作简单,成本低廉,是研究和基础研究的理想选择。
-
缺点:
- 无法在工业应用中推广。
- 产量低,耗时长。
-
液相剥离
- 工艺:这种方法是将石墨分散在溶剂(通常是非水性溶剂,如 n-甲基-2-吡咯烷酮)中,然后施加能量(如超声波或高剪切力)来分离石墨烯层。然后使用离心分离法分离出单层和少层石墨烯薄片。
-
优点:
- 比机械剥离法更具可扩展性。
- 可大量生产石墨烯,适用于复合材料和涂层等应用。
-
缺点:
- 生产的石墨烯通常电气质量较低。
- 需要离心等后处理步骤来提高产量和质量。
-
化学气相沉积(CVD)
- 工艺:CVD 是指在高温下将基底暴露于含碳气体中,从而在基底(通常是铜或镍)上生长石墨烯。碳原子沉积在基底上,形成石墨烯层。
-
优点:
- 生产大面积、高质量的石墨烯。
- 可扩展,适合工业应用。
-
缺点:
- 需要昂贵的设备和对反应条件的精确控制。
- 后加工步骤(如将石墨烯从基底上转移)可能会带来缺陷。
-
还原氧化石墨烯 (GO)
- 工艺:氧化石墨烯是通过氧化石墨产生的,然后通过化学或热方法将石墨还原成石墨烯。该工艺可与液相剥离相结合,以提高产量。
-
优点:
- 具有成本效益和可扩展性。
- 可批量生产石墨烯,用于能源储存和传感器等应用。
-
缺点:
- 生产的石墨烯往往含有残余氧和缺陷,影响其电气性能。
- 需要额外的步骤来提高质量。
-
碳化硅(SiC)的升华
- 工艺:这种方法是将碳化硅加热到高温,使硅原子升华,在表面留下石墨烯层。
-
优点:
- 生产出具有优异电气性能的高质量石墨烯。
- 无需基底转移步骤,降低了出现缺陷的风险。
-
缺点:
- 由于起始材料(碳化硅)昂贵,成本较高。
- 工业应用的可扩展性有限。
-
其他考虑因素
- 基质处理:对于 CVD 等方法,对基底进行处理(例如对铜进行化学处理)可减少缺陷并增大基底的晶粒尺寸,从而提高石墨烯的质量。
- 产量与质量的权衡:每种方法都需要在产量、质量和可扩展性之间进行权衡。例如,机械剥离法质量高但产量低,而液相剥离法产量高但质量低。
- 特定应用方法:剥离方法的选择取决于预期应用。例如,化学气相沉积法非常适合电子产品,而液相剥离法可能更适合复合材料或涂层。
总之,石墨烯剥离方法的选择取决于质量、产量和可扩展性之间的平衡。机械剥离法最适合研究,液相剥离法适合批量应用,而 CVD 适合高质量、大面积的石墨烯。每种方法都有其自身的一系列挑战,但正在进行的研究仍在不断改进这些工艺,使石墨烯更易于广泛应用。
汇总表:
方法 | 工艺概要 | 优点 | 缺点 |
---|---|---|---|
机械剥离 | 使用胶带从石墨中剥离石墨烯层。 | 石墨烯质量高、操作简单、成本低廉。 | 不可扩展、产量低、耗时长。 |
液相剥离 | 将石墨分散在溶剂中,利用能量分离石墨层。 | 可扩展,适合复合材料等大块应用。 | 电气质量较低,需要后处理。 |
化学气相沉积(CVD) | 利用含碳气体在基底上生长石墨烯。 | 可生产大面积、高质量的石墨烯,并可扩展至工业用途。 | 设备昂贵,后处理可能带来缺陷。 |
还原氧化石墨烯(GO) | 氧化石墨并还原成石墨烯。 | 成本效益高,可批量应用。 | 残留氧和缺陷会影响电气性能。 |
碳化硅(SiC)升华 | 加热碳化硅使硅升华,留下石墨烯。 | 高质量石墨烯,无需基底转移。 | 成本高,可扩展性有限。 |
需要帮助选择适合您项目的石墨烯剥离方法? 立即联系我们的专家 !