Introduction to Isostatic Presses
Isostatic pressing is a manufacturing process that uses pressure to create uniform parts with consistent density and strength. The process involves placing a material in a flexible container, which is then pressurized from all sides to create a uniform shape. Isostatic presses can be used for both cold isostatic pressing (CIP) and hot isostatic pressing (HIP). CIP is used for powder compaction, while HIP is used for densification of pre-formed parts. Isostatic presses are widely used in the aerospace industry for creating high-performance materials and components.
Table of Contents
Types of Isostatic Presses
Isostatic presses are used in various industries, including aerospace. There are two main types of isostatic presses used in aerospace applications: cold isostatic pressing (CIP) and hot isostatic pressing (HIP).
Cold Isostatic Pressing (CIP)
CIP involves applying pressure to a material using a fluid medium at room temperature. The fluid medium is typically water or oil. This type of pressing is used to create materials that are strong and durable, such as ceramic components for rocket engines. Cold isostatic presses are generally used in room temperature environments and are suitable for temperature-sensitive materials such as ceramics, metal powders, etc.
Hot Isostatic Pressing (HIP)
On the other hand, HIP involves applying pressure and heat to a material simultaneously. The heat and pressure are applied using an autoclave, which is a high-pressure vessel. This type of pressing is used to create complex shapes and parts, such as turbine blades for aircraft engines. Hot isostatic presses use an argon atmosphere or other gas mixtures heated up to 3000º F and pressurized up to 100,000 psi to process powders and other materials into dense preformed metals, plastics and ceramics. Hot isostatic presses function by introducing gas into the HIP furnace and simultaneously increasing the temperature and pressure to add density to the materials being processed.
Warm Isostatic Pressing (WIP)
Warm isostatic presses work at medium temperature and are suitable for materials with certain requirements on temperature, such as plastics, rubber, etc. The working temperature of hot isostatic press is high temperature, suitable for materials with high-temperature requirements, such as metals, alloys, etc.
In conclusion, isostatic presses are a crucial tool in the development of aerospace materials and components. Both types of isostatic presses have their own unique advantages and disadvantages, and the choice of which one to use depends on the specific application. The aerospace industry relies heavily on isostatic presses to create materials that are strong, lightweight, and able to withstand the harsh conditions of space. As technology advances, new and innovative uses for isostatic presses are discovered, making them a crucial tool in the development of aerospace materials and components.
Cold Isostatic Pressing (CIP)
Isostatic pressing is a powder metallurgy forming process that applies equal pressure in all directions on a powder compact, thus achieving maximum uniformity of density and microstructure without the geometrical limitations of uniaxial pressing. Cold isostatic pressing (CIP) is a specific type of isostatic pressing that involves compacting powdered materials into a solid, homogeneous mass before machining or sintering.
The CIP Process
In the cold isostatic pressing process, a mold or vacuumed sample is placed into a chamber that is filled with a working fluid, usually water with a corrosion inhibitor, which is pressurized by an external pump. The pressure chamber of the machine is designed to withstand the severe cyclic loading imposed by rapid production rates and has taken into account fatigue failure. Compared with cold pressing, isostatic compaction applies pressure uniformly over the entire surface of the mold, which eliminates die-wall friction, a factor that exerts a major influence on the density distribution of cold-pressed parts.
Advantages of CIP
The elimination of die-wall lubricants also permits higher pressed densities and eliminates problems associated with lubricant removal prior to or during final sintering. Furthermore, if necessary, air can be evacuated from the loose powder before compaction. Consequently, isostatic compaction provides increased and more uniform density at a given compaction pressure and relative freedom from compact defects when applied to brittle or fine powders. Because of the uniform compaction pressure, the cross section-to-height ratio of the part is not a limiting factor as it is with uniaxial pressing. In addition, cold isostatic pressing can be used to compact more complex shapes than possible with uniaxial pressing.
Applications of CIP
Cold isostatic pressing is commonly used for parts that are too large to be pressed in uniaxial presses and that do not require high precision in the sintered state. It is a very simple process capable of producing high-integrity billets or preforms that exhibit little distortion or cracking when fired. Some of the common applications for CIP include consolidation of ceramic powders, compressing of graphite, refractories and electrical insulators, and other fine ceramics for dental and medical applications. The technology is expanding into new applications such as pressing of sputtering targets, coatings of valve parts in an engine to minimize wear of the cylinder heads, telecommunications, electronics, aerospace and automotive.
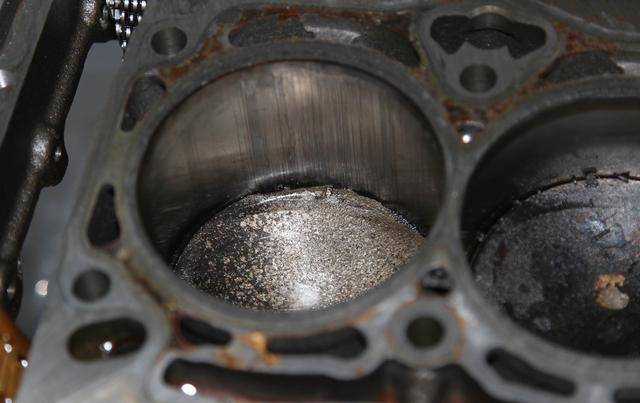
In the aerospace industry, CIP is used to manufacture parts for aircraft engines, turbines, and other components that require high strength and durability. The process is especially useful for producing parts that are difficult to machine or cast, such as those with intricate shapes or thin walls. Isostatic presses come in various sizes and designs, depending on the specific needs of the application. They are typically made of stainless steel or other high-strength materials capable of withstanding the high pressures and forces involved in the process.
Cold isostatic pressing is a proven process for high-performance parts, and as the demand for high-performance materials and manufacturing processes in the aerospace industry continues to grow, isostatic presses will remain an essential tool for researchers, engineers, and manufacturers alike.
Hot Isostatic Pressing (HIP)
Hot Isostatic Pressing (HIP) is a technique used in the aerospace industry to improve the quality and performance of critical aerospace components. The process involves the simultaneous application of high temperature and pressure to metals and other materials, such as ceramics, for a specified amount of time to improve their mechanical properties.
What Happens during HIP?
In a HIP unit, a high-temperature furnace is enclosed in a pressure vessel. The temperature, pressure, and process time are all precisely controlled to achieve the optimal material properties. Parts are heated in an inert gas, generally argon, which applies "isostatic" pressure uniformly in all directions. This causes the material to become "plastic," allowing voids to collapse under the differential pressure. The surfaces of the voids diffusion bond together to effectively eliminate the defects achieving near theoretical density while improving mechanical properties of the parts such as investment castings.
Benefits of HIP
The use of isostatic presses for aerospace applications has become increasingly common in recent years due to its numerous benefits. HIP can be used to consolidate metal powders, remove porosity, and increase material density, resulting in stronger, more durable components. This process is especially beneficial for aerospace applications, as it can improve the fatigue life, reduce the risk of failure, and increase the overall reliability of components.
Repairing Damaged Aerospace Parts
Additionally, HIP can be used to repair damaged or worn aerospace parts by filling in cracks and voids with new material. The process is highly specialized and requires a high degree of precision and expertise to achieve optimal results. The encapsulation methods, such as direct sealing of the circumference of the contact area between the two parts, placement of a sleeve of material around the contact area between the two parts, or full, or partial encapsulation of the entire component, must be carefully selected to ensure the interface is isolated from the gaseous pressure medium.
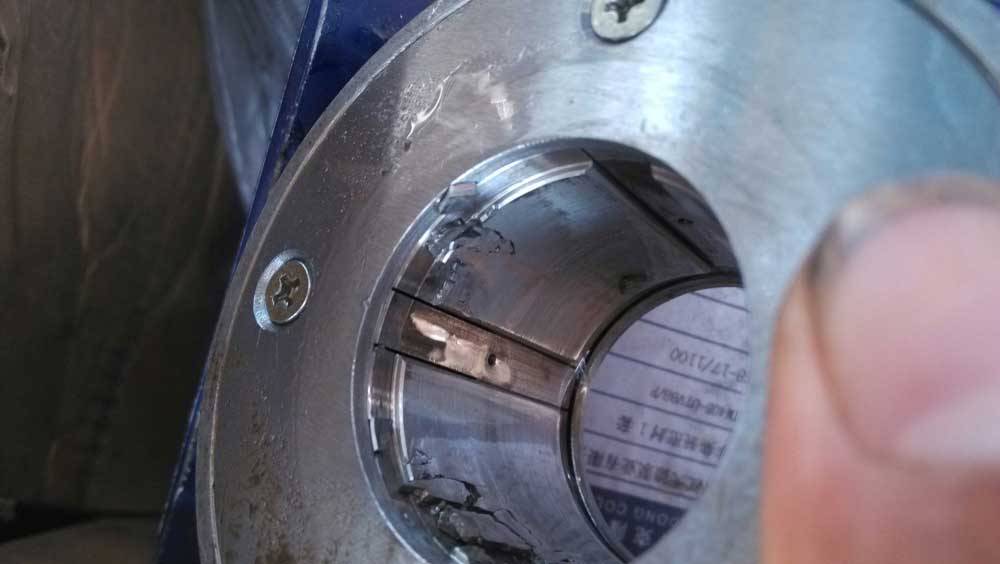
Cost-Effective Aerospace Components
HIP is an important technology for the aerospace industry that allows for smaller, lighter-weight parts with similar or superior performance to be produced. When incorporated as an integral part of the manufacturing process, HIP reduces scrap and improves yield. HIP also reduces quality assurance inspection requirements by improving material properties and reducing property scatter. Often, the savings on radiographic costs will cover the costs of HIP. Optimizes material properties, and parameters can be established to minimize subsequent heat treatment requirements. Processed parts exhibit enhanced reliability and extension of service life. It can reduce the total production costs of a product.
In conclusion, HIP is a critical process in the production of high-quality, reliable aerospace components. It allows for the consolidation of metal powders, the removal of porosity, and the increasing of material density, resulting in stronger, more durable components. Additionally, HIP can be used to repair damaged or worn aerospace parts. The encapsulation methods must be carefully selected to ensure the interface is isolated from the gaseous pressure medium. The use of isostatic presses for aerospace applications has become increasingly common in recent years, as manufacturers seek to produce cost-effective and high-quality products that can withstand the demands of space travel.
Isostatic Presses in the Aerospace Industry
Isostatic presses are an essential part of the aerospace industry, where precision and uniformity are of utmost importance. These machines are used to create high-quality and complex aerospace parts such as turbine blades, engine mounts, and heat shields.
Isostatic Pressing in Aerospace Industry
Isostatic pressing involves applying pressure equally from all directions to a material, making it ideal for producing parts with uniform density and strength. The aerospace industry demands high-quality and reliable equipment, and isostatic presses meet these requirements.
Production of Composite Materials
Isostatic presses are also used in the production of composite materials, which are increasingly being used in aerospace applications due to their lightweight and high-strength properties. Composite materials are used to manufacture aircraft parts such as wings, fuselage sections, and other structural components. Isostatic pressing is essential in the production of composite materials as it ensures that the material is uniformly compressed, resulting in a product with consistent strength and density.
Benefits of Isostatic Pressing in Aerospace Industry
The isostatic pressing method ensures that the parts manufactured are of high quality, reliable, and safe. The uniform density and strength of the parts produced using isostatic pressing make them ideal for use in the aerospace industry. The process also allows for the production of complex parts with precision and uniformity, making isostatic presses an indispensable tool in the manufacturing of aerospace parts.
Isostatic Pressing Equipment
Isostatic presses used in the aerospace industry consist of a high-pressure vessel, heating furnace, compressor, vacuum pump, storage tank, cooling system, and computer control system, where the high-pressure vessel is the key device of the whole equipment. The hot isostatic densification process involves placing the products into the closed container and inputting high pressure (50-200MPa) argon gas into the container through the compressor, while heating through the heating furnace inside the container, so that the products can be densified under the action of high temperature (400-2000℃) and high pressure at the same time.
Conclusion
Isostatic presses have revolutionized the manufacturing process of aerospace parts, especially with the increasing demand for composite materials. The uniformity and precision of the parts produced using this method make them ideal for use in the aerospace industry. The aerospace industry will continue to rely on isostatic presses to produce high-quality and complex parts with precision and uniformity.
Advantages of Isostatic Pressing in Aerospace
Isostatic pressing is a process that involves uniformly applying pressure to a material from all directions, resulting in a highly dense and uniform material. This process has been widely used in the aerospace industry due to its numerous advantages.
Complex Shapes and High Precision
One of the key advantages of isostatic pressing is that it can produce parts with complex shapes and high precision. This is particularly useful in the aerospace industry where components need to be precise and fit perfectly with other parts.
High Strength and Durability
Isostatic pressing can produce parts with high strength and durability, which is crucial for aerospace applications where parts need to withstand extreme conditions such as high temperatures, pressure, and vibration.
Reduced Defects
Isostatic pressing can also reduce the number of defects in the final product, which increases the safety and reliability of the components.
Versatility in Material Selection
Another advantage is that isostatic pressing can be used with a wide range of materials, including metal, ceramics, and composites, making it a versatile process.
Automation for Efficiency
Finally, isostatic pressing can be automated, which increases efficiency and reduces the risk of human errors.
Overall, isostatic pressing is a highly beneficial process for the aerospace industry as it can produce high-quality, precise, and durable components that meet the rigorous demands of aerospace applications.
Examples of Aerospace Applications
Isostatic presses are widely used in the aerospace industry to create high-density materials with consistent quality that can withstand the extreme conditions of spaceflight. Here are some examples of how isostatic presses are used in aerospace applications:
Rocket Engines Manufacturing
Rocket engines require intricate shapes and complex designs that can only be achieved through isostatic pressing. Isostatic presses are used to create high-density materials that have consistent density and have the ability to withstand the extreme heat and pressure generated by the engine. These engines are crucial components of spacecraft and their reliability is of utmost importance.
Heat Shields Production
Heat shields are ceramic parts that protect spacecraft during re-entry into the earth's atmosphere. These parts must be able to withstand extreme temperatures and radiation. Isostatic presses are used to create high-density materials that can withstand these conditions and have consistent quality.
Turbine Blades Production
Turbine blades for jet engines must be strong enough to withstand extreme heat and pressure. Isostatic pressing ensures that the blades are free of defects and have consistent density. This is important for the efficient and safe operation of the engine.
Satellite Components Production
Satellites must be able to withstand the harsh conditions of space. Isostatic pressing is used to create high-density materials that can withstand radiation and extreme temperature changes. These materials are used to create satellite components that are reliable and can withstand the harsh environment of space.
In addition to these specific applications, isostatic presses are also used in the production of a variety of other aerospace components. These machines are vital in ensuring that spacecraft and their components are able to withstand the harsh conditions of spaceflight and operate reliably.
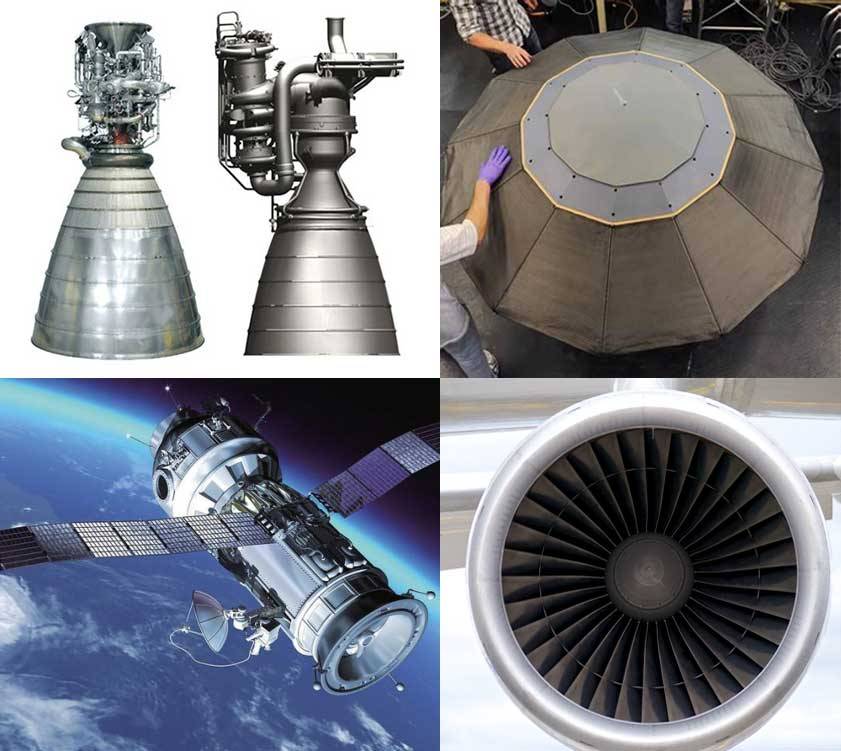
Future of Isostatic Pressing in Aerospace
Isostatic pressing has been a critical technology in the aerospace industry for the production of high-strength and lightweight materials. With the continued demand for stronger and lighter materials, isostatic pressing is expected to play an even more critical role in the development of new aerospace materials.
Isostatic Pressing for High-Temperature Materials
One area where isostatic pressing is expected to play a crucial role is in the development of new materials that can withstand high temperatures. Materials that can withstand high temperatures are essential for the development of hypersonic flight vehicles, which are expected to revolutionize air travel. Isostatic pressing can produce materials that have exceptional mechanical properties, making them ideal for use in these applications.
Isostatic Pressing for Composite Materials
Another area where isostatic pressing is expected to play a significant role is in the development of new composite materials. These materials are made by combining two or more different materials to create a new material that has improved properties. Isostatic pressing can be used to compress these materials, enhancing their strength and durability.
Isostatic Pressing for Additive Manufacturing Materials
To improve the mechanical properties and workability of additive manufacturing materials, many manufacturers use isostatic pressing. Isostatic pressing can be performed at elevated temperatures, known as hot isostatic pressing (HIP), or at ambient temperatures, known as cold isostatic pressing (CIP). Hot isostatic pressing can be used to manufacture metal components directly, or to densify parts from other powder metallurgy processes. Isostatic pressing has several benefits over the commonly used press and sinter method, including equal compaction in all directions and a more uniform final component density.
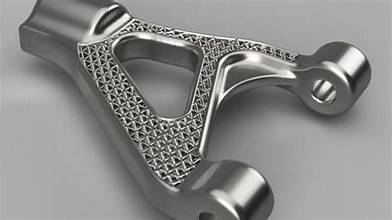
Powder Characterization for Successful Isostatic Pressing
As with other powder metallurgy processes, manufacturers must carefully characterize the metal powder’s properties for isostatic pressing to be successful. Spherical powders with a relatively wide but consistent particle size distribution are preferred for HIP because they produce higher fill densities. For CIP, some particle irregularity may help increase cold-welding, ideally without compromising powder flow and packing. Phase composition and grain size are also important characteristics to control, as they can affect the final component's mechanical properties.
In conclusion, isostatic pressing is a critical technology in the aerospace industry, and its future looks very bright. With the continued demand for stronger and lighter materials, isostatic pressing is expected to play an even more critical role in the development of new aerospace materials. Isostatic pressing can produce materials that have exceptional mechanical properties, making them ideal for use in aerospace applications where strength and weight are critical factors.
联系我们获取免费咨询
KINTEK LAB SOLUTION 的产品和服务得到了世界各地客户的认可。我们的员工将竭诚为您服务。如需免费咨询,请与我们的产品专家联系,以找到最适合您应用需求的解决方案!