热压是一种结合热量和压力生产高密度、高强度材料的制造工艺。由于这种技术能够制造出具有优异机械和热性能的材料,因此被广泛应用于陶瓷、冶金和复合材料等行业。热压技术的优点包括提高材料密度、增强机械强度、更好地控制微观结构,以及能够生产出缺陷最小的复杂形状。此外,与传统的烧结方法相比,热压还能减少加工时间和能耗。下面,我们将详细探讨热压的主要优势。
要点说明:
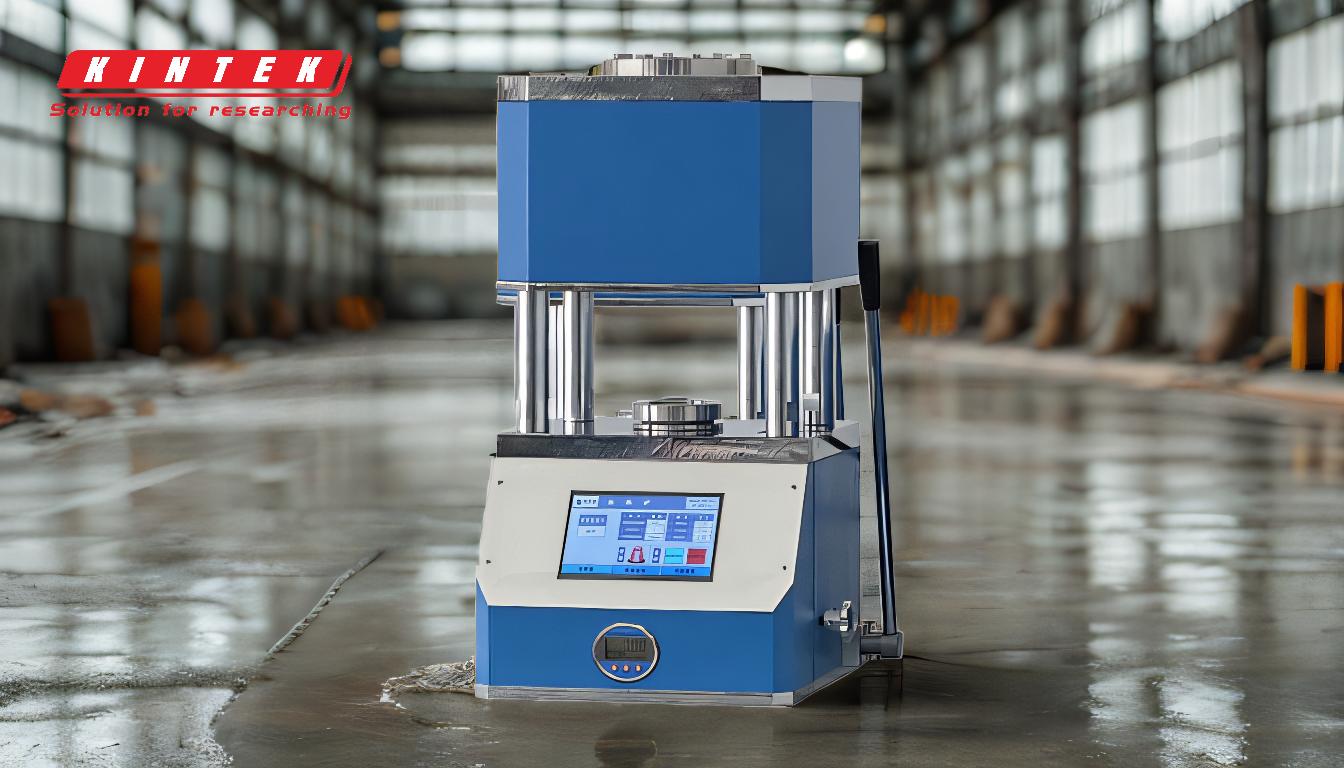
-
提高材料密度
- 热压同时施加热量和压力,有助于消除材料内部的孔隙和空隙。这样,最终产品密度更大,机械性能(如硬度、耐磨性和断裂韧性)也得到改善。
- 高压可确保颗粒紧密压实,而热量可促进颗粒间的扩散和粘合,从而形成更均匀的结构。
-
增强机械强度
- 热压过程中的热量和压力相结合,可加强颗粒间的结合,从而提高材料的整体强度。
- 这对于航空航天部件或切削工具等需要高承载能力的应用尤为有利。
-
更好地控制微观结构
- 热压可以精确控制材料的微观结构,包括晶粒大小和分布。这种控制对于获得所需的性能(如导热性、导电性和耐腐蚀性)至关重要。
- 对微观结构进行定制的能力使热压成型适用于陶瓷和复合材料等先进材料。
-
生产复杂形状
- 热压成型可用于生产复杂的形状,只需进行最少的后处理。均匀的压力可确保即使是复杂的几何形状在成型时也不会出现裂缝或空洞等缺陷。
- 这对于制造公差要求严格的部件(如涡轮叶片或医疗植入物)尤为有利。
-
减少加工时间和能耗
- 与传统烧结方法相比,热压将加热和压实步骤合并为一个操作,从而大大缩短了加工时间。
- 加工时间的缩短也意味着能耗的降低,使热压成为一种更具可持续性的制造选择。
-
减少缺陷,改善表面光洁度
- 热压过程中施加的压力有助于最大限度地减少缺陷,如气孔和表面不规则。这使得表面光洁度更高,从而减少了额外的机加工或精加工工序。
- 对于光学元件或半导体器件等表面完整性要求极高的应用来说,无缺陷的表面至关重要。
-
材料兼容性的多样性
- 热压工艺与多种材料兼容,包括金属、陶瓷和复合材料。这种多功能性使其成为需要不同材料特性的行业的首选。
- 例如,它可用于生产电子用先进陶瓷、汽车用金属基复合材料和航空用碳-碳复合材料。
-
大规模生产的成本效益
- 虽然热压设备的初始设置成本可能较高,但由于其效率高、浪费少,在大规模生产中,该工艺的成本效益很高。
- 此外,只需极少的后处理就能生产出高质量的部件,这也进一步促进了成本的节约。
总之,热压工艺具有众多优势,包括改善材料性能、提高机械强度,以及能够生产出缺陷最小的复杂形状。它的高效性和多功能性使其成为从航空航天到电子等各行各业的重要工艺。通过了解这些优点,设备和耗材采购人员在为其特定应用选择制造工艺时就能做出明智的决定。
汇总表:
优势 | 描述 |
---|---|
提高材料密度 | 消除气孔和空隙,使材料更致密、更坚固。 |
增强机械强度 | 更强的颗粒间结合力,适用于高承载应用。 |
更好的微观结构控制 | 精确的晶粒尺寸和分布,实现量身定制的材料特性。 |
复杂形状生产 | 形成复杂的几何形状,将缺陷和后处理减少到最低程度。 |
缩短加工时间 | 结合加热和压实,节省时间和能源。 |
缺陷最小化 | 光滑的表面光洁度,减少了额外加工的需要。 |
材料多样性 | 与金属、陶瓷和复合材料兼容,适用于各种应用。 |
成本效益 | 高效、低废料工艺,是大规模生产的理想选择。 |
准备好改进您的生产工艺了吗? 今天就联系我们 了解有关热压解决方案的更多信息!