感应加热虽然在许多应用中具有优势,但也有一些明显的缺点。这些缺点包括初始成本高、需要专业设备和熟练人员、精炼能力有限、热分布管理困难以及需要专用电感器。此外,感应加热系统通常需要强大的控制算法来处理不同的负载和工作点,并且可能面临热量分布不均和加热速率过高等问题。与其他加热方法相比,这些因素可能会使感应加热变得不那么灵活,而且成本更高。
要点说明
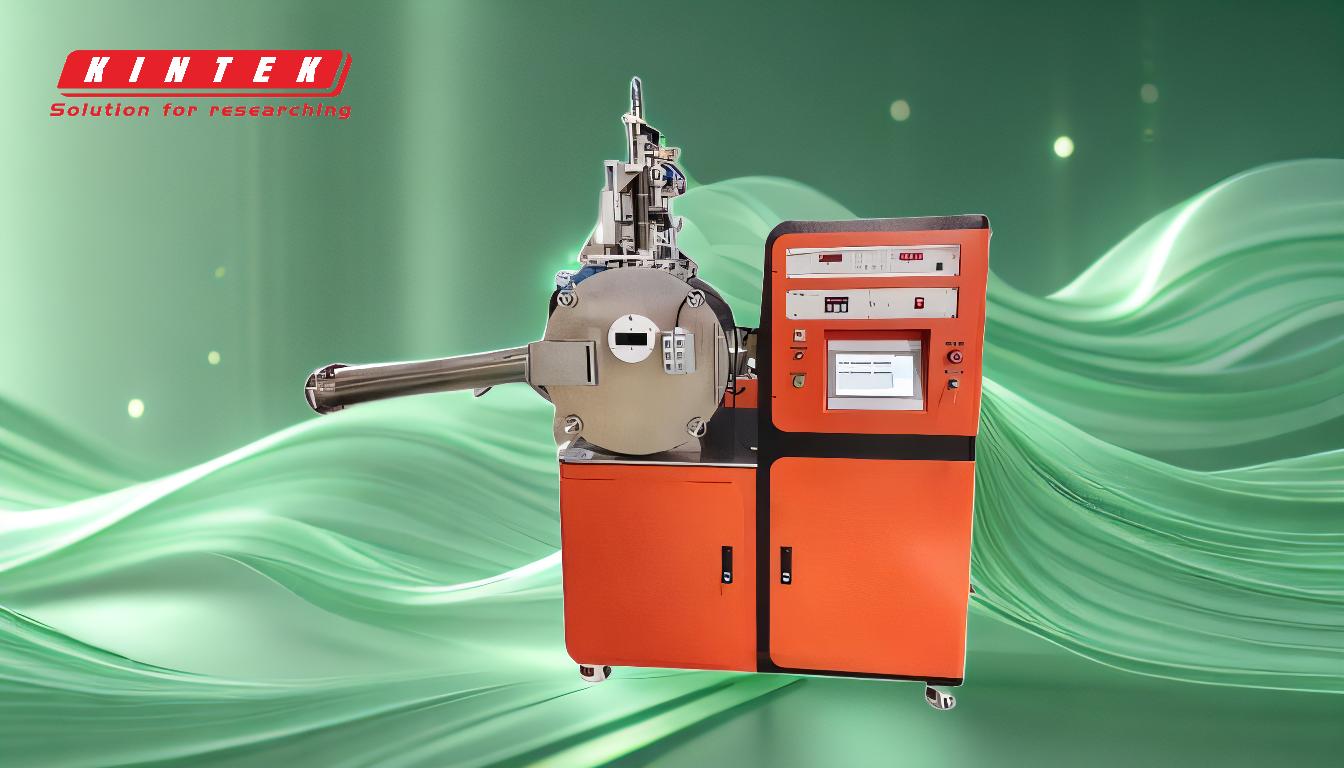
-
初始投资高
- 感应加热系统需要大量前期费用,包括高频发电机和电源等专用设备。
- 需要具备感应加热原理和安全程序专业知识的技术人员,这进一步增加了运行费用。
- 因此,对于预算有限的小规模运行或应用来说,电感加热就不那么容易实现了。
-
缺乏炼油能力
- 感应炉不能精炼材料,这意味着装料材料必须不含氧化物且成分已知。
- 某些合金元素可能会在加热过程中因氧化而损失,需要重新添加到熔体中。
- 这种限制使得感应加热不适合需要净化或提炼材料的应用。
-
需要专用电感器
- 由于需要为特定应用生产定制电感器,电感加热的灵活性受到限制。
- 这些电感器的设计和制造成本很高,尤其是复杂或独特几何形状的电感器。
- 在小型铜电感器中管理高电流密度通常需要专业的工程设计和精确的 "铜配",这进一步增加了成本。
-
热量分配面临的挑战
- 感应加热会导致热量分布不均匀,从而可能导致最终产品的材料特性不一致。
- 高加热率会加剧这一问题,对材料造成热应力或损坏。
- 正确的校准和良好的电感耦合对实现均匀加热至关重要,从而增加了工艺的复杂性。
-
与导热系数的关系
- 感应加热的效果取决于被加热材料的热传导率。
- 导热性差的材料可能无法均匀加热,从而限制了感应加热在某些情况下的适用性。
- 与对流或辐射加热等其他方法相比,这种对材料特性的依赖限制了感应加热的多功能性。
-
复杂的控制要求
- 要针对不同的感应加热负载和工作点管理电源转换器,就必须采用可靠的控制算法。
- 多线圈系统带来了更多挑战,需要实时识别和自适应算法才能实现最佳性能。
- 这些复杂的控制问题会增加感应加热系统的成本和实施难度。
-
表面加热限制
- 感应加热对表面加热最有效,但可能不适合需要均匀加热整个材料的应用。
- 这一局限性限制了它在某些需要深度或容积加热的热处理工艺中的应用。
-
关注能源效率
- 虽然电感加热在特定应用中可以实现节能,但所需的高频发电机和电源会消耗大量能源。
- 系统效率低下,如感应耦合不良或热量损失,会进一步降低整体能效。
-
维护和运行挑战
- 由于感应加热设备的专业性,通常需要熟练的技术人员进行定期维护和故障排除。
- 运行方面的挑战,如管理高电流密度和确保正确校准,可能会导致停机和运行成本增加。
-
针对不同应用的灵活性有限
- 对定制电感器的需求以及对材料特性的依赖限制了电感加热对各种应用的适应性。
- 其他加热方法,如燃气炉或电炉,可为更多材料和工艺提供更大的灵活性。
总之,虽然感应加热在特定应用中具有精确性和高效性,但其缺点--如成本高、精炼能力有限以及热量分布和控制方面的挑战--使其不太适合某些情况。在为工业或制造过程选择加热方法时,了解这些局限性对于做出明智的决策至关重要。
总表:
劣势 | 说明 |
---|---|
初始投资高 | 设备和技术人员的前期费用高昂。 |
缺乏炼油能力 | 无法提炼材料;需要预先纯化的充电材料。 |
需要专用电感器 | 定制电感器价格昂贵,灵活性有限。 |
热量分配面临的挑战 | 加热不均匀会导致材料性能不一致。 |
与导热系数的关系 | 对导热性差的材料效果有限。 |
复杂的控制要求 | 需要针对不同的负载和工作点采用稳健的算法。 |
表面加热限制 | 不适合深度加热或均匀加热。 |
关注能源效率 | 高能耗和潜在的低效率。 |
维护方面的挑战 | 需要熟练的技术人员和定期维护。 |
有限的灵活性 | 与其他加热方法相比,对各种应用的适应性较差。 |
需要帮助为您的应用选择正确的加热方法吗? 立即联系我们的专家 获取个性化建议!