双板模具结构是应用最广泛的注塑模具类型,其特点是在单个分模平面上将模具分成两半。这种设计简单高效,适用于各种注塑成型应用。在多腔模具中,流道和浇口系统位于分模平面内,以确保模具打开时成型零件和流道的正确顶出。这种结构具有成本效益,易于制造,非常适合生产几何形状简单的零件。
要点说明:
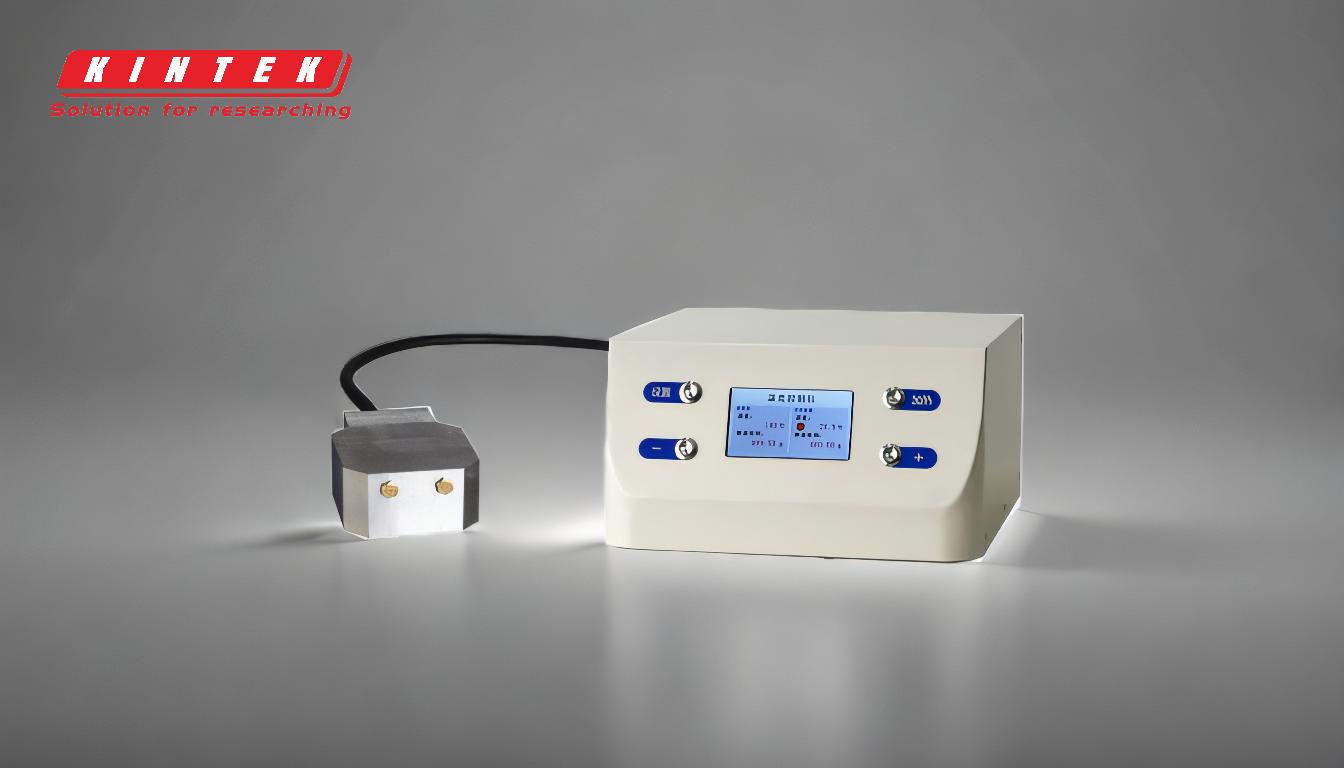
-
双板模具的定义
- 双板模具是最简单、最常见的注塑模具类型,由两块主板组成:型腔板(固定的一半)和型芯板(移动的一半)。
- 模具沿单个分模面(即两块板之间的界面)分开。这种设计可使成型零件与模具轻松分离。
-
分模面及其重要性
- 分模面是两半模具相接和分离的表面。
- 它对于确保模具打开时成型部件以及流道和浇口能够干净利落地顶出至关重要。
- 分模面的位置要经过精心设计,以避免出现缺口,确保顺利脱模。
-
流道和浇口位置
- 在双板模具中,流道系统(向型腔输送熔融塑料)和浇口(型腔入口)位于分模平面内。
- 这种放置方式可确保在模具打开时,流道和浇口与成型件一起顶出。
- 对于多腔模具,这种设计简化了顶出过程,降低了缺陷风险。
-
双板模具的优点
- 简单: 设计简单明了,与三板模具等更复杂的模具相比,制造更容易,成本更低。
- 成本效益高: 由于部件少,加工要求简单,因此生产成本更低。
- 易于维护: 活动部件少:减少机械故障的可能性,简化维护。
- 适用于简单零件: 适用于几何形状不复杂、无凹槽的零件。
-
双板模具的局限性
- 设计灵活性有限: 不适合几何形状复杂或有凹槽的零件,因为这些零件需要额外的机构,如侧动或升降器。
- 流道和浇口限制: 流道和浇口必须位于分型面内,这会限制某些零件的设计选择。
- 材料浪费: 在某些情况下,流道系统可能会导致材料浪费,尤其是在单腔模具中。
-
双板模具的应用
- 常用于生产简单的塑料零件,如容器、瓶盖和外壳。
- 效率高、操作简便,适合大批量生产。
- 适用于不需要复杂顶出机构或侧面动作的零件。
-
与其他模具类型的比较
- 三板模具: 与双板模具不同,三板模具有一个额外的板将流道系统与成型部件分开,从而可以更灵活地放置浇口。不过,三板模具更为复杂和昂贵。
- 热流道模具: 这种模具可使塑料在流道中保持熔融状态,从而减少材料浪费,因此无需使用流道系统。不过,这种模具的成本要高得多,而且需要精确的温度控制。
-
双板模具的设计注意事项
- 分模线位置: 分模线的设计应尽量减少飞边(多余材料),并确保易于弹出。
- 浇口设计: 浇口的位置应使熔融塑料顺利流入型腔,同时尽量减少成品部件上的可见痕迹。
- 顶出机制: 必须安装适当的弹射销或弹射板,以确保零件在释放时不会受到损坏。
通过了解双板模具结构,制造商可以在模具设计和选择方面做出明智的决策,确保高效生产和高质量零件。这种结构因其简单、可靠和成本效益高而一直是注塑成型行业的基石。
汇总表:
方面 | 细节 |
---|---|
定义 | 最简单的注塑模具,有两块板:型腔板和型芯板。 |
分模平面 | 模具分模的单一平面,便于零件和流道的顶出。 |
流道和浇口位置 | 位于分型面内,可实现高效顶出。 |
优点 | 简单、成本效益高、易于维护,是简单几何形状的理想选择。 |
局限性 | 设计灵活性有限,流道/闸门限制,可能浪费材料。 |
应用 | 用于容器、瓶盖、外壳和大批量生产。 |
比较 | 比三板模具或热流道模具更简单、更便宜。 |
设计注意事项 | 关注分模线、浇口设计和顶出机构,确保质量。 |
您的生产需要可靠的双板模具吗? 今天就联系我们 讨论您的需求!