马弗炉是一种专门的高温加热设备,用于实验室和工业环境中的灰化、烧结、热处理和材料测试等过程。其设计特点是有一个独立的燃烧室和一个气体密封的加热室,确保被加热的材料不受燃烧副产品的污染。现代马弗炉通常使用电加热元件,可提供精确的温度控制和一致性。使用马弗炉的程序包括准备样品、设定所需温度和监控加热过程,以达到所需的结果。气密门和温度控制器等安全装置对安全操作至关重要。
要点说明:
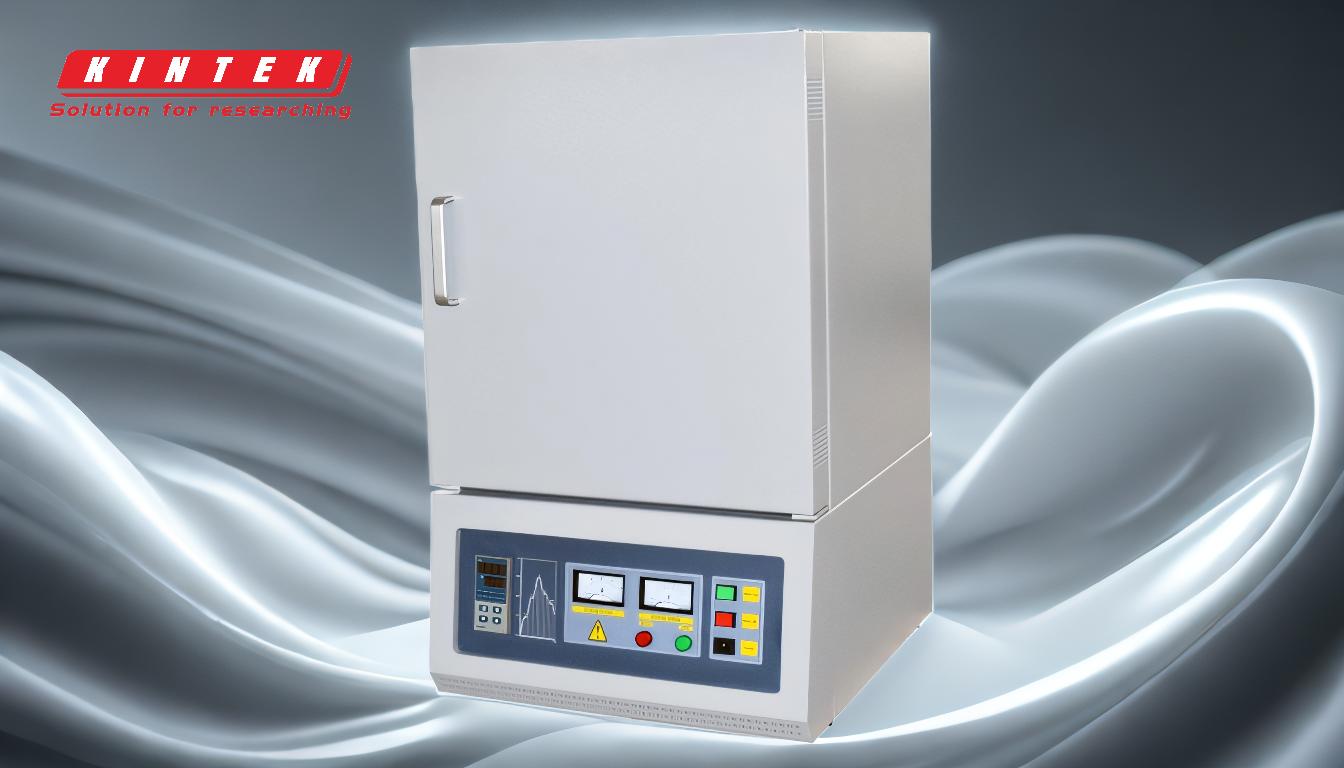
-
马弗炉的原理:
- 马弗炉的工作原理是将被加热材料与燃烧过程隔离开来。这是通过一个气体密封加热室实现的,该加热室可防止燃烧副产品的污染。现代马弗炉通常使用电加热元件,与传统的燃烧系统相比,电加热元件可提供更清洁、更可控的加热。这种设计尤其适用于烧结、退火和灰化等需要高温和精确控制的工艺。更多详情,请参阅 马弗炉 .
-
设计与组件:
-
马弗炉通常包括
- 加热室:气体密封舱:放置材料进行加热的舱室。
- 加热元件:产生热量的电或燃烧元件。
- 隔热:优质隔热材料,可保持高温并提高能效。
- 温度控制系统:先进的控制器可精确调节温度。
- 安全功能:气密门、过温保护和警报,以确保操作安全。
-
马弗炉通常包括
-
马弗炉的使用步骤:
- 样品制备:确保样品清洁并为加热做好适当准备。
- 装炉:将样品放入加热室,确保其位置稳固。
- 设置温度:使用温度控制系统设置所需的温度。
- 加热过程:启动窑炉并监控加热过程。现代熔炉通常配有可编程控制器,用于自动加热循环。
- 冷却和卸载:加热过程结束后,待炉冷却后再取出样品。
-
马弗炉的应用:
- 阿兴:用于通过燃烧掉有机成分来确定材料的灰分含量。
- 烧结:加热粉末状材料,使其在不熔化的情况下形成固体。
- 热处理:退火、淬火和回火等改变材料特性的工艺。
- 烧制陶瓷:将陶瓷材料加热至高温,以获得所需的特性。
- 熔化金属:冶金过程中用于熔化金属以进行铸造或合金化。
-
安全考虑:
- 气密门:确保炉门密封良好,以保持环境安全。
- 温度监控:使用内置温度控制器和警报器防止过热。
- 通风:确保适当通风,避免有害气体积聚。
- 个人防护设备(PPE):操作窑炉时应穿戴适当的个人防护设备,如耐热手套和安全眼镜。
-
现代马弗炉的优点:
- 精确度:电加热元件提供精确的温度控制。
- 清洁加热:无燃烧副产品,确保清洁的加热环境。
- 多功能性:适用于各种高温应用。
- 能源效率:先进的隔热材料和加热元件可降低能耗。
通过了解马弗炉的原理、设计和使用程序,用户可以在确保安全和精度的前提下,有效地将该设备用于各种高温应用。
汇总表:
方面 | 细节 |
---|---|
原则 | 利用气体密封舱将材料与燃烧副产品隔离。 |
关键部件 | 加热室、加热元件、隔热材料、温度控制系统。 |
程序 | 样品准备、装载、温度设定、加热、冷却和卸载。 |
应用 | 灰化、烧结、热处理、烧制陶瓷、熔化金属。 |
安全功能 | 气密门、温度控制器、警报器、通风设备、个人防护设备。 |
优势 | 精确、清洁加热、多功能、节能。 |
了解马弗炉如何改进您的实验室流程 今天就联系我们 获取专家指导!