等离子渗氮和氮碳共渗都是热化学表面硬化工艺,用于增强金属零件的机械性能,如硬度、耐磨性和疲劳寿命。然而,它们的机制、引入金属的元素以及所得的表面特性不同。等离子渗氮涉及使用等离子环境将氮扩散到金属表面,而氮碳共渗则将氮和碳引入表面层。这些差异导致每个工艺都有独特的优势和应用。
要点解释:
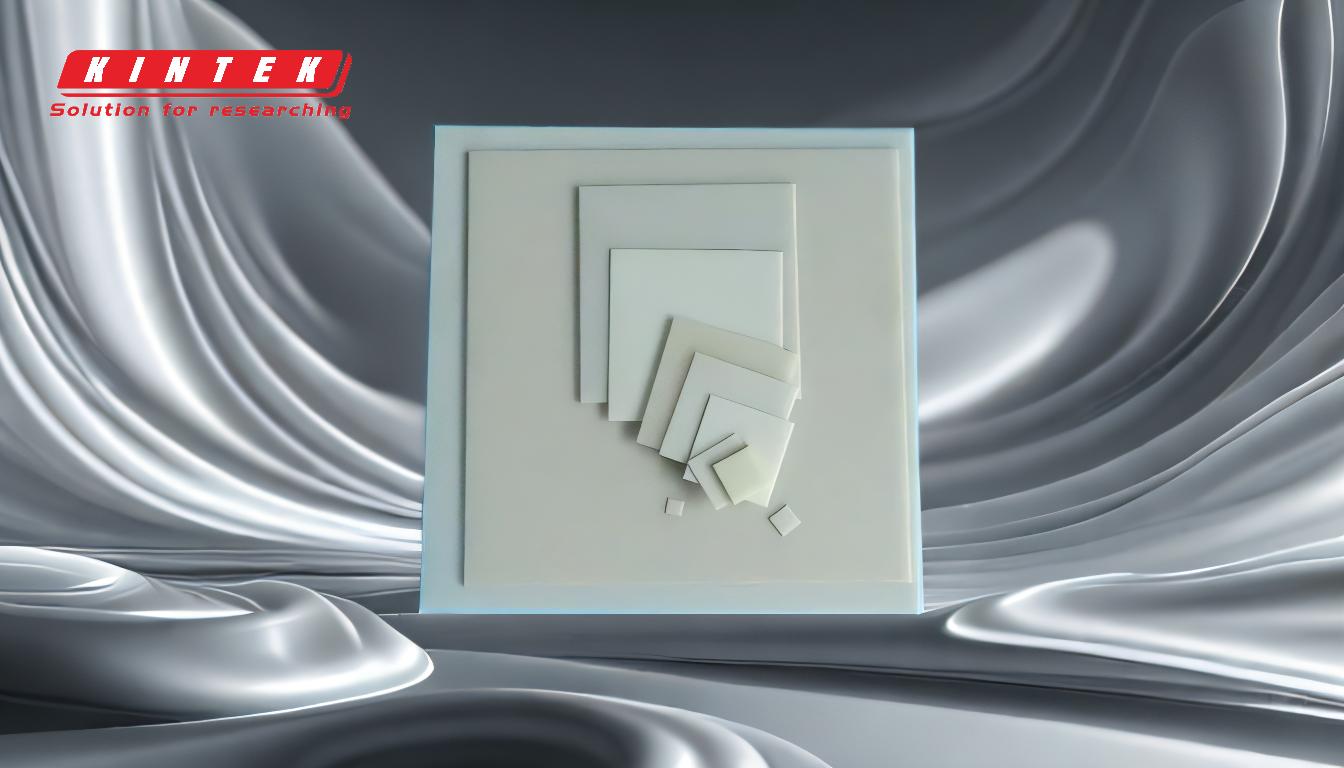
-
过程机制:
- 等离子渗氮 :该工艺利用等离子体环境电离氮气,然后扩散到金属表面。通过在工件(阴极)和室壁(阳极)之间施加高电压来产生等离子体。电离的氮原子向工件加速,在表面形成硬氮化物层。
- 氮碳共渗 :此过程涉及同时将氮和碳引入金属表面。它通常在含有氨(对于氮气)和富碳气体(例如二氧化碳或甲烷)的气态气氛中进行。氮和碳的组合扩散形成化合物层和其下方的扩散区。
-
要素介绍:
- 等离子渗氮 :仅将氮引入金属表面,形成氮化物,提高硬度和耐磨性。
- 氮碳共渗 :同时引入氮和碳,形成富含碳氮化物和氮化物的化合物层,从而提高耐磨性并减少摩擦。
-
温度和过程控制:
- 等离子渗氮 :在亚临界温度(通常在 350°C 至 600°C 之间)下运行,可最大限度地减少变形并允许精确控制氮化物层厚度。
- 氮碳共渗 :也可在亚临界温度(通常在 500°C 至 600°C 之间)下运行,但碳的存在需要仔细控制气体成分,以实现所需的表面特性。
-
表面特性:
- 等离子渗氮 :产生坚硬、耐磨的表面,变形最小。该工艺对于复杂的几何形状和薄壁部件特别有效,因为它能够均匀地处理复杂的形状。
- 氮碳共渗 :形成具有优异耐磨性和减少摩擦的复合层,使其适合需要改进滑动性能的应用。由于形成致密的化合物层,该工艺还增强了耐腐蚀性。
-
应用领域:
- 等离子渗氮 :通常用于硬度和耐磨性至关重要的高精度部件,例如齿轮、冲模和模具。它也适用于不锈钢和钛等材料,这些材料受益于硬氮化层的形成。
- 氮碳共渗 :非常适合遭受滑动磨损的部件,例如曲轴、凸轮轴和液压缸。该工艺还用于需要提高疲劳强度和耐腐蚀性的零件。
-
优点和局限性:
- 等离子渗氮 :提供对氮化层的精确控制、出色的表面硬度和最小的变形。然而,它需要专门的设备,并且比其他一些表面硬化方法更昂贵。
- 氮碳共渗 :兼具硬度、耐磨性和耐腐蚀性。对于某些应用来说,它更具成本效益,但可能无法达到与等离子渗氮相同的硬度水平。
通过了解这些关键差异,设备和耗材购买者可以做出明智的决定,决定哪种工艺最适合他们的特定需求,无论他们优先考虑硬度、耐磨性还是成本效益。
汇总表:
方面 | 等离子渗氮 | 氮碳共渗 |
---|---|---|
机制 | 使用等离子体将氮气扩散到金属表面。 | 将氮和碳引入金属表面。 |
要素介绍 | 仅氮气。 | 氮和碳。 |
温度范围 | 350°C 至 600°C。 | 500°C 至 600°C。 |
表面特性 | 坚硬、耐磨的表面,变形最小。 | 复合层具有耐磨、减摩、耐腐蚀的特点。 |
应用领域 | 齿轮、模具等高精度零部件。 | 遭受滑动磨损的部件,例如曲轴和凸轮轴。 |
优点 | 控制精确,硬度优异,变形极小。 | 具有成本效益,提高耐磨性和耐腐蚀性。 |
局限性 | 需要专门设备,成本较高。 | 可能无法达到与等离子渗氮相同的硬度。 |
需要帮助为您的金属部件选择正确的表面硬化工艺吗? 立即联系我们的专家 获取量身定制的建议!