溅射和脉冲激光沉积(PLD)都是用于制造薄膜的物理气相沉积(PVD)技术,但两者在机制、应用和结果上有很大不同。溅射是利用高能离子将原子从目标材料中物理喷射出来,然后沉积到基底上。这种方法不依赖热量,因此适用于低温应用和各种材料,包括塑料和有机物。另一方面,PLD 使用高能激光脉冲烧蚀目标材料,形成等离子体羽流,沉积到基底上。PLD 以能够保留目标材料的化学计量而著称,因此非常适合氧化物等复杂材料,并能精确控制薄膜的微观结构。根据薄膜应用的具体要求,这两种技术都具有独特的优势。
要点说明:
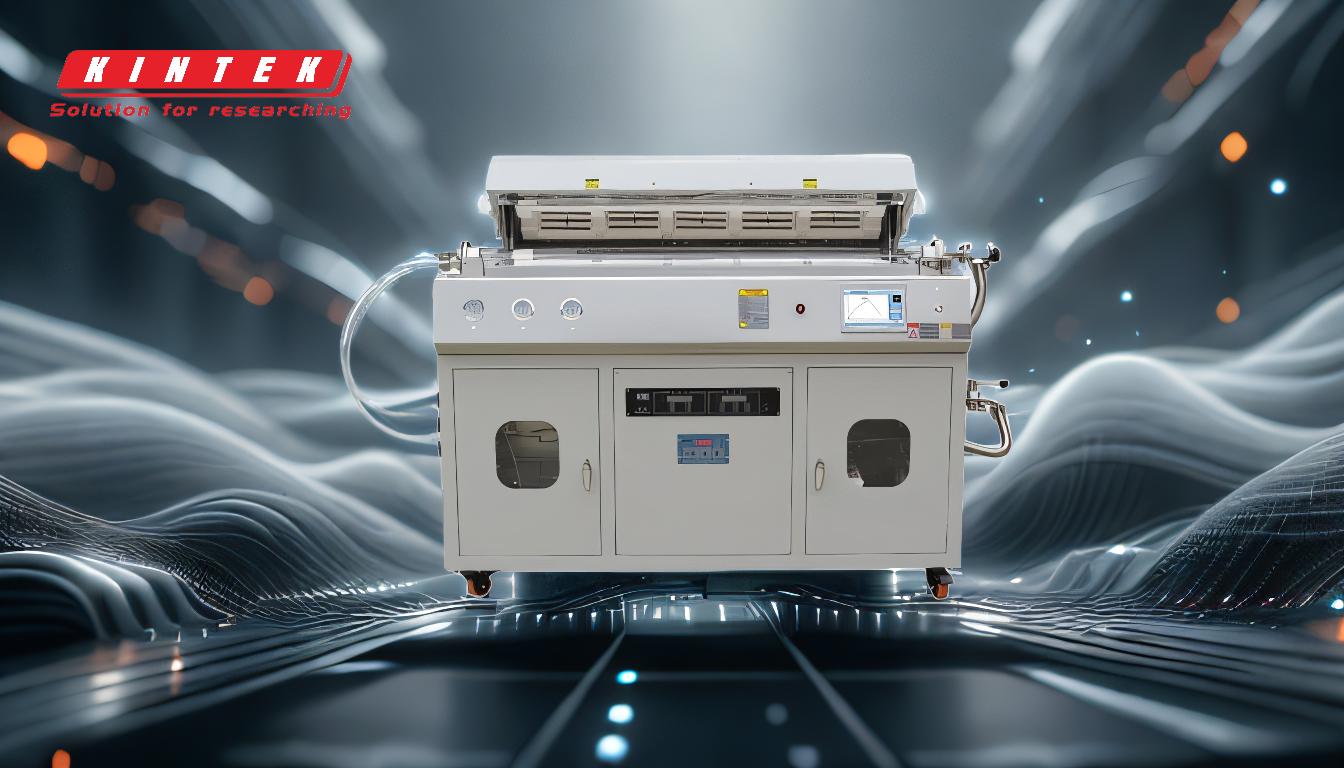
-
材料喷射机制:
- 溅射: 在溅射过程中,目标材料和基底之间会产生等离子体。等离子体中的高能离子轰击靶材,通过动量传递使原子喷射出来。这一过程不涉及目标材料的熔化,因此适用于对高温敏感的材料。
- PLD: PLD 使用高能激光脉冲烧蚀目标材料。激光脉冲从目标物中产生由离子、原子和分子组成的等离子体羽流,然后凝结在基底上。这种方法非常精确,可通过控制达到特定的薄膜特性。
-
温度要求:
- 溅射: 溅射可以在相对较低的温度下进行,这对于塑料和有机物等对温度敏感的材料的涂层来说非常有利。该工艺不依赖热蒸发,从而降低了对基底造成热损伤的风险。
- PLD: PLD 也可以在较低的基底温度下进行沉积,但激光烧蚀过程本身会产生局部高温。不过,基底的整体温度仍然很低,因此适用于易碎材料。
-
化学计量和薄膜成分:
- 溅射: 虽然溅射可以产生高质量的薄膜,但要保持复杂材料(如多组分氧化物)的精确化学计量却具有挑战性。由于不同元素的溅射产率不同,该过程可能会导致成分的细微偏差。
- PLD: PLD 的主要优势之一是能够在沉积薄膜中保留目标材料的化学计量。这对于需要精确成分控制的复杂材料尤为重要。PLD 通常用于沉积氧化物、氮化物和其他多组分材料。
-
薄膜微观结构和晶粒尺寸:
- 溅射: 溅射法生产的薄膜晶粒更小,微观结构更均匀。这种工艺可以很好地控制薄膜的均匀性和粘附性,因此适合需要致密、粘附性好的薄膜的应用。
- PLD: PLD 可对晶粒尺寸和微观结构进行出色的控制,从而沉积出具有特定结构特性的薄膜。这使 PLD 成为研究应用的理想选择,因为研究微观结构与性能之间的关系非常重要。
-
沉积速率和效率:
- 溅射: 溅射法的沉积速率因目标材料和工艺条件而异。对于纯金属,沉积速率可能相对较高,但对于复杂材料,沉积速率可能较低。对于大面积涂层和工业应用,溅射通常是高效的。
- PLD: 与溅射相比,PLD 的沉积速率通常较低,尤其是在大面积涂层方面。不过,它在精度和控制方面表现出色,因此更适合薄膜质量至关重要的研究和小规模应用。
-
应用和材料兼容性:
- 溅射 溅射被广泛应用于各种材料的涂层,包括金属、半导体和绝缘体。对于需要良好附着力和均匀性的应用,如光学涂层、硬涂层和电子设备的生产,溅射尤其有效。
- PLD: PLD 通常用于需要精确控制薄膜成分和微观结构的研究环境和特殊应用。它尤其适用于沉积高温超导体、铁电薄膜和多组分氧化物等复杂材料。
-
真空要求:
- 溅射: 与电子束蒸发等其他 PVD 技术相比,溅射技术的真空度通常较低。这对于某些难以保持高真空度的应用非常有利。
- PLD: PLD 通常需要较高的真空环境,以确保沉积薄膜的纯度和质量。高真空有助于最大限度地减少污染,并能更好地控制沉积过程。
总之,虽然溅射和 PLD 都是用于薄膜沉积的 PVD 技术,但它们在机理、温度要求、保持化学计量的能力、微观结构控制、沉积速率和应用方面都有所不同。溅射技术更适用于工业应用和大面积涂层,而 PLD 则具有更高的精度和控制能力,是研究和特殊应用的理想选择。
汇总表:
特征 | 溅射 | PLD |
---|---|---|
机理 | 高能离子通过动量传递将原子从目标中喷射出来。 | 高能激光脉冲烧蚀材料,形成等离子体羽流。 |
温度 | 低温工艺,适用于热敏材料。 | 基底温度低,但烧蚀过程中局部温度较高。 |
化学计量 | 对复杂材料具有挑战性;可能出现轻微偏差。 | 保持目标材料的化学计量,是复杂氧化物的理想选择。 |
微观结构 | 晶粒更小、薄膜更均匀、附着力更强。 | 可精确控制晶粒大小和微观结构。 |
沉积速率 | 金属材料高,复杂材料低;大面积使用时效率高。 | 沉积率较低,更适合精密和小规模使用。 |
应用 | 工业涂料、光学薄膜、电子产品。 | 研究、高温超导体、铁电薄膜。 |
真空要求 | 真空度较低,易于维护。 | 更高的真空度可保证纯度和质量控制。 |
需要帮助选择正确的薄膜沉积技术? 立即联系我们的专家 获取量身定制的建议!