热解是一种将有机物转化为气体、液体和固体等有用产品的热分解过程,其效率取决于多个因素。这些因素包括原料成分、反应器设计、操作参数(温度、压力、停留时间)以及生物质的含水量。正确控制这些因素对于最大限度地将有机材料转化为高能量产品和提高整体工艺效率至关重要。此外,优化粒度、加热速率和反应器条件还能进一步提高热解效率。
要点说明
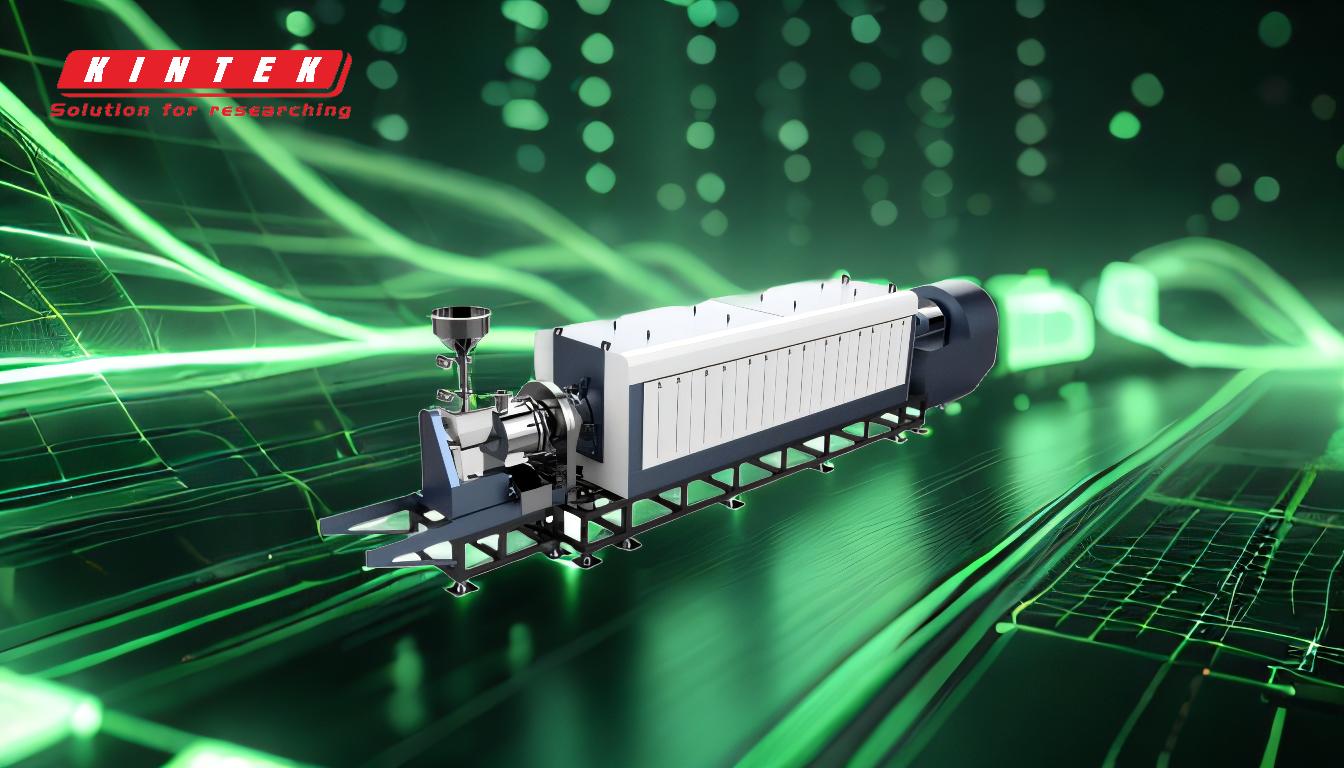
-
影响热解效率的因素
- 原料成分:废物或生物质的类型和成分对热解效率有很大影响。有机馏分的降解方式不同,其转化为气体、液体或固体取决于其化学结构。
- 水分含量:生物质含水量高会降低效率,因为能量被浪费在蒸发水分而不是降解有机物上。干燥原料是提高效率的首选。
- 颗粒大小:较小的颗粒尺寸可增加传热表面积,从而使热解反应更快、更均匀。
-
运行参数
- 温度:热解效率在很大程度上取决于温度。最佳温度因原料而异,但一般在 400°C 至 800°C 之间。更高的温度可以提高气体产量,但可能会降低液体或固体产品产量。
- 停留时间:物料在反应器中停留的时间会影响分解程度。停留时间越长,转化越彻底,但可能会降低产量。
- 压力:在适当的压力下运行可确保高效的热传递和产品形成。升高压力可以促进某些反应,但过高的压力可能会给操作带来挑战。
-
反应堆设计与优化
- 反应堆类型:不同的反应器设计(如流化床、固定床、回转窑)具有不同的效率。反应器的选择取决于原料和所需的最终产品。
- 加热率:受控和优化的加热速率可确保原料的高效分解。快速加热可提高液体产品的产量,而慢速加热则有利于产生气体或焦炭。
- 能源回收:高效的能源回收系统可将热解过程中产生的热量用于其他操作,从而提高整体工艺效率。
-
提高热解效率
- 优化原料制备:干燥、切碎和分拣等预处理方法可提高原料质量和热解效率。
- 先进控制系统:对温度、压力和停留时间实施自动控制系统,可确保始终如一的最佳条件。
- 催化热解:使用催化剂可以降低所需的反应温度,提高特定产品(如生物油或合成气)的产量。
-
挑战和考虑因素
- 原料变化:不一致的原料成分会导致不可预测的热解结果,这就需要采取适应性操作策略。
- 能量输入:加热反应器和维持最佳条件所需的能量必须与热解产品的能量输出相平衡。
- 环境影响:高效热解可最大限度地减少排放和废物,但操作不当会导致有害副产品的释放。
-
应用与优势
- 能源生产:热解将废物和生物质转化为生物油、合成气和生物炭等高能量产品,这些产品可用于发电或用作燃料。
- 废物管理:热解减少了废物量,并将其转化为有价值的资源,为循环经济做出了贡献。
- 碳封存:热解过程中产生的生物碳可用于改善土壤健康和固碳,减少温室气体排放。
通过了解和优化这些因素,可以显著提高热解的效率,使其成为废物管理和能源生产的可行且可持续的解决方案。
总表:
系数 | 对热解效率的影响 |
---|---|
原料成分 | 根据化学结构确定气体、液体或固体的转换。 |
水分含量 | 高水分会降低效率;最好是干燥原料。 |
颗粒大小 | 较小的颗粒增加了表面积,改善了传热和反应的均匀性。 |
温度 | 最佳温度范围:400°C-800°C;较高温度有利于产生气体,较低温度有利于产生液体/固体。 |
停留时间 | 较长的时间可确保完全分解,但可能会降低吞吐量。 |
反应堆类型 | 选择取决于原料和所需产品(如流化床、固定床、回转窑)。 |
加热率 | 受控的速率可确保高效分解;快速加热有利于液体,慢速加热有利于气体。 |
催化热解 | 催化剂可降低反应温度,提高生物油或合成气等特定产品的产量。 |
优化热解工艺,实现最高效率 立即联系我们的专家 !