感应炉的熔损是指在熔化过程中,由于氧化、蒸发、成渣等因素造成的金属重量的减少。这种损失受到几个变量的影响,包括熔化速率、功率配置、炉料清洁度、熔炉设计和所使用的耐火材料。干净的装料、适当的炉体长度和合适的坩埚(如石英坩埚)可以通过提高效率和减少传热消耗来最大限度地减少熔化损失。此外,由于水流不当、炉衬尺寸或耐火材料导致的过热可能会加剧熔损。了解这些因素有助于优化熔炉操作并减少材料浪费。
要点解释:
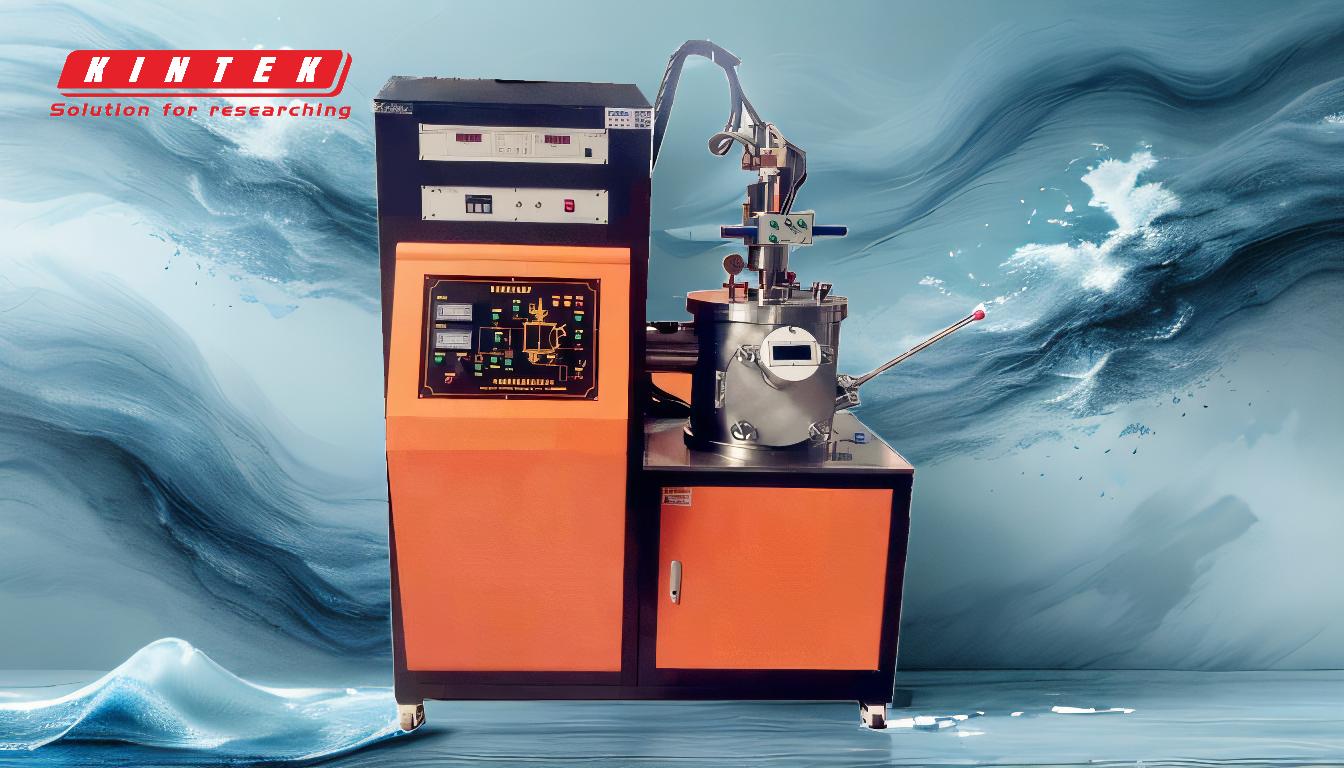
-
熔损的定义:
- 熔损是指金属在感应炉中熔化过程中重量的减少。这种损失是由于氧化、蒸发和熔渣形成而发生的,这些都是熔化过程所固有的。
-
影响熔损的因素:
- 熔化速率和功率配置 :熔化率的计算公式为(功率,单位为千瓦)/(标准功耗,单位为千瓦时/吨),直接影响熔化损失。较高的功率配置可以减少熔化时间,但如果不加以控制,可能会增加氧化和蒸发。
- 充电清洁度和尺寸 :杂质最少的清洁炉料可减少炉渣形成和氧化,从而最大限度地减少熔化损失。炉料的大小也会影响熔化和热量分布的均匀性。
- 耐火材料和坩埚 :所使用的耐火材料和坩埚的类型,例如石英坩埚,对于减少传热损失和提高整体效率起着重要作用。
- 熔炉设计和炉衬 :适当的炉衬尺寸和足够的耐火材料可以防止过热和线圈损坏,否则会导致熔化损失增加。
-
过热及其影响:
- 由于水流路径的限制或熔炉设计不当而导致熔炉线圈过热,会导致熔损增加。过热会加速氧化和蒸发,导致更多的材料浪费。
-
熔化速率和时间的计算:
- 熔化率的计算公式为:(功率(kW))/(标准功耗(kWh/吨)=(金属重量(kg))/(1000 kg)。例如,在 325 kW 时,熔化速率为 520 kg/小时。
- 熔化时间的计算公式为:(功率(kW)*时间(小时)/(金属重量(kg))=(标准功耗(kWh/吨*1小时)/(1000 kg)。对于功率为 325 kW 的 550 kg 熔炉,熔化时间为 1.06 小时(64 分钟)。
-
优化策略:
- 清洁充电 :确保炉料不含杂质和污染物,可减少炉渣形成和氧化。
- 正确的熔炉设计 :保持适当的炉体长度和炉衬尺寸可防止过热并提高效率。
- 适用坩埚 :使用石英坩埚等坩埚可减少传热损失,提高熔化效率。
- 定期保养 :定期检查和维护水流路径、热交换器和电源线可防止过热并确保一致的性能。
通过了解和解决这些因素,操作员可以最大限度地减少熔损,提高熔炉效率,并减少感应炉操作中的材料浪费。
汇总表:
关键因素 | 对熔损的影响 |
---|---|
熔化速率和功率 | 较高的功率会缩短熔化时间,但可能会增加氧化和蒸发。 |
充电清洁度和尺寸 | 清洁炉料可最大限度地减少炉渣形成和氧化,从而减少熔损。 |
耐火材料 | 石英坩埚等合适的材料可减少传热损失并提高效率。 |
熔炉设计和炉衬 | 适当的尺寸可防止过热和线圈损坏,从而减少材料浪费。 |
过热 | 过热加速氧化和蒸发,增加熔损。 |
优化您的感应炉操作并减少熔损 — 立即联系我们的专家 定制解决方案!