陶瓷热压工艺是对陶瓷粉末同时施加热量和压力,以达到致密化和成型的目的。这种方法对于生产高密度、细粒度、机械性能更强的陶瓷材料尤为有效。该工艺通常包括几个阶段:粉末制备、模具填充、加热、压制、冷却和后处理。通过加热和加压,热压可减少孔隙率,改善陶瓷的微观结构,使其适用于需要高强度和耐用性的应用。
要点说明:
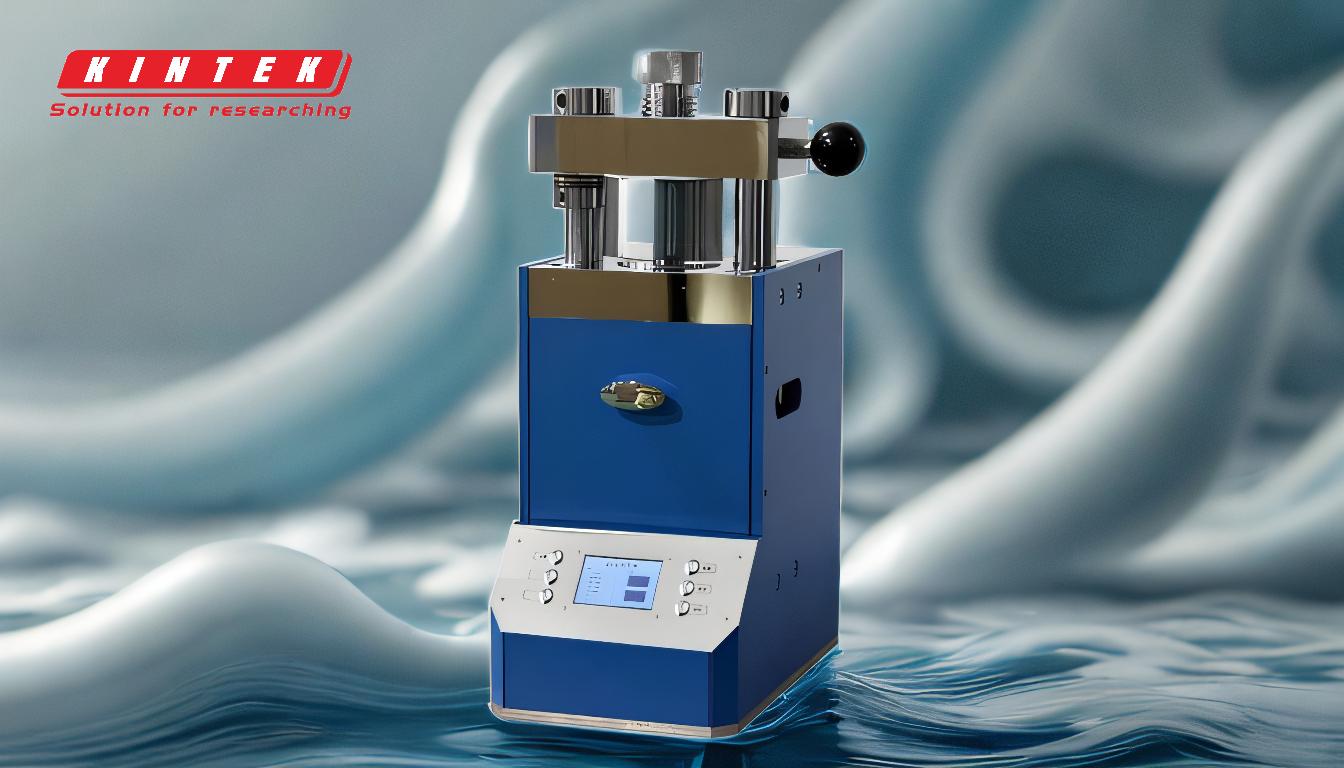
-
粉末制备:
- 首先要制备陶瓷粉末,陶瓷粉末通常颗粒细小且均匀。粉末可与粘合剂或添加剂混合,以改善流动性和压实性。
- 适当的粉末制备可确保热压过程中的均匀致密化。
-
模具填充:
- 将制备好的陶瓷粉末装入模具,模具通常由石墨或其他耐高温材料制成。模具的设计可承受工艺中使用的高温和高压。
- 模具的均匀填充对于实现一致的致密化和避免最终产品出现缺陷至关重要。
-
加热:
- 将装有陶瓷粉末的模具放入热压炉中,根据陶瓷材料的不同,加热温度通常在 1000°C 至 2000°C 之间。
- 加热过程受到严格控制,以确保温度分布均匀,这对获得均匀的微观结构至关重要。
-
压制:
- 达到所需温度后,使用液压或机械手段对陶瓷粉末施加压力。压力范围从几兆帕到几百兆帕不等。
- 热量和压力的结合会促进颗粒重新排列、塑性变形和扩散,从而导致致密化和消除孔隙。
-
冷却:
- 压制阶段结束后,陶瓷缓慢冷却至室温。控制冷却对防止热应力和裂纹非常重要。
- 冷却速度可根据特定陶瓷材料及其热特性进行调整。
-
后处理:
- 热压陶瓷可能需要经过其他后加工步骤,如机械加工、抛光或表面处理,以达到所需的最终尺寸和表面光洁度。
- 后处理可确保陶瓷部件符合其预期应用所需的规格。
-
热压工艺的优势:
- 热压法生产的陶瓷密度高、晶粒细小、机械性能(如强度、硬度和耐磨性)更好。
- 该工艺尤其适用于传统烧结方法难以致密化的材料。
-
应用领域:
- 热压陶瓷应用广泛,包括切削工具、耐磨部件、电子基板和生物医学植入物。
- 热压陶瓷具有更强的性能,适用于要求高性能和高可靠性的苛刻环境。
通过这些步骤,热压工艺可以生产出具有卓越性能的高质量陶瓷材料,使其成为先进陶瓷制造领域的一项重要技术。
汇总表:
阶段 | 描述 |
---|---|
粉末制备 | 制备细粒陶瓷粉末,通常使用粘合剂以提高流动性。 |
模具填充 | 将粉末装入耐高温模具,以实现均匀的致密化。 |
加热 | 模具加热至 1000°C-2000°C,使温度分布均匀。 |
加压 | 施加压力(兆帕)以消除气孔并实现致密化。 |
冷却 | 受控冷却可防止热应力和开裂。 |
后处理 | 加工、抛光或表面处理,确保最终规格。 |
优势 | 密度高、粒度细、机械性能优异。 |
应用领域 | 切削工具、耐磨部件、电子基板和植入物。 |
了解更多有关热压技术如何提高陶瓷生产效率的信息 立即联系我们的专家 !