溅射虽然是一种广泛使用的薄膜沉积技术,但也有一些明显的缺点,会影响其效率、成本和对某些应用的适用性。这些缺点包括资本支出高、某些材料的沉积率低、潜在的薄膜污染以及控制薄膜厚度和均匀性方面的挑战。此外,溅射通常需要复杂的设备和冷却系统,这会增加运营成本,降低生产速度。该工艺与某些材料的兼容性也较差,特别是有机固体,它们在离子轰击下会发生降解。此外,溅射还可能将杂质带入基底,而且其扩散传输机制使薄膜结构设计与升华工艺的整合变得更加复杂。
要点说明:
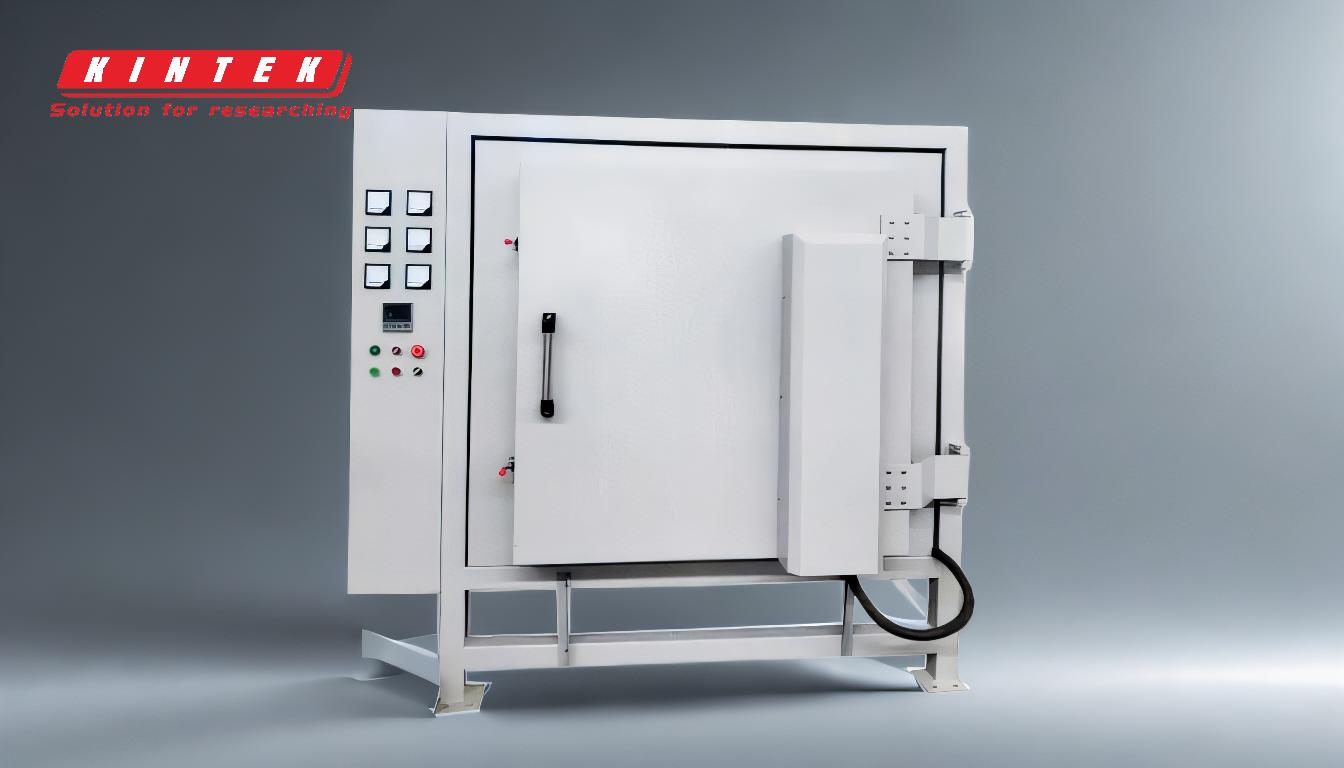
-
高资本支出:
- 溅射设备通常价格昂贵,需要大量的前期投资。这包括高压装置、冷却系统和其他专用组件的成本。
- 对冷却系统的需求不仅增加了初始资本成本,还增加了持续能源支出,降低了工艺的整体成本效益。
-
低沉积率:
- 与热蒸发等其他技术相比,溅射技术的沉积率通常较低。对于某些材料(如二氧化硅)来说尤其如此,这会降低生产速度。
- 在对速度要求很高的高产能制造环境中,溅射率低可能是一个很大的限制因素。
-
薄膜污染:
- 溅射的主要缺点之一是薄膜污染的风险。目标材料或溅射环境中的杂质会进入薄膜,降低薄膜的质量。
- 等离子体中的气体污染物会被激活并融入生长中的薄膜,进一步增加污染风险。
- 在反应溅射沉积过程中,必须仔细控制气体成分,以防止靶材中毒,因为靶材中毒也会导致污染。
-
难以控制薄膜厚度和均匀性:
- 在溅射过程中,由于沉积流量分布不均匀,要实现均匀的薄膜厚度可能具有挑战性。这通常需要使用移动夹具来确保均匀镀膜。
- 溅射原子的弥散传输使其难以实现完全遮蔽,从而使与薄膜成型的升华工艺的整合变得更加复杂。
-
材料限制:
- 某些材料,尤其是有机固体,在溅射工艺固有的离子轰击下容易发生降解。这就限制了使用这种技术可以有效沉积的材料范围。
- 涂层材料的选择还受到熔点的限制,因为熔点很高的材料可能不适合溅射。
-
杂质介绍:
- 与蒸发法相比,溅射法的真空度较低,这增加了将杂质带入基底的可能性。这会影响沉积薄膜的纯度和性能。
-
复杂的设备和维护:
- 溅射工艺需要复杂的设备,包括高压装置和冷却系统,这些设备可能难以维护和操作。
- 用户提供维护的需要和工艺参数的限制会使溅射技术在工业应用中的使用更加复杂。
-
基片温升高:
- 溅射过程会导致基底温度显著升高,这对于温度敏感的材料或应用来说可能是不可取的。
- 温度升高还会使基底更容易受到杂质气体的污染。
总之,尽管溅射是一种用途广泛的沉积技术,但它也有一些缺点,可能会限制其在某些应用中的有效性。这些缺点包括成本高、沉积率低、污染风险、难以控制薄膜特性、材料限制和复杂的设备要求。了解这些缺点对于为特定应用选择合适的沉积方法以及优化溅射工艺以减少其局限性至关重要。
总表:
缺点 | 说明 |
---|---|
高昂的资本支出 | 昂贵的设备和冷却系统增加了前期和持续成本。 |
沉积速率低 | 二氧化硅等材料的沉积速率较低,限制了高通量生产。 |
薄膜污染 | 靶材或等离子体中的杂质会降低薄膜质量。 |
薄膜厚度控制 | 不均匀的沉积流量使实现均匀涂层变得复杂。 |
材料限制 | 有机固体在离子轰击下会降解;高熔点材料不太适用。 |
杂质引入 | 真空度较低会增加基底中的杂质风险。 |
复杂的设备 | 高压设备和冷却系统需要大量维护。 |
基底温升 | 对温度敏感的材料可能会因溅射过程中产生的热量而降解。 |
需要帮助选择正确的薄膜沉积方法? 立即联系我们的专家 获取量身定制的解决方案!