挤压是一种广泛使用的制造工艺,但它也有一些缺点,会影响产品质量、成本和灵活性。主要缺点包括产品尺寸的变化、横截面的均匀性对产品设计的限制以及高昂的初始设置成本。这些因素会使挤压技术不太适合某些应用,特别是那些要求复杂几何形状或严格公差的应用。
要点说明:
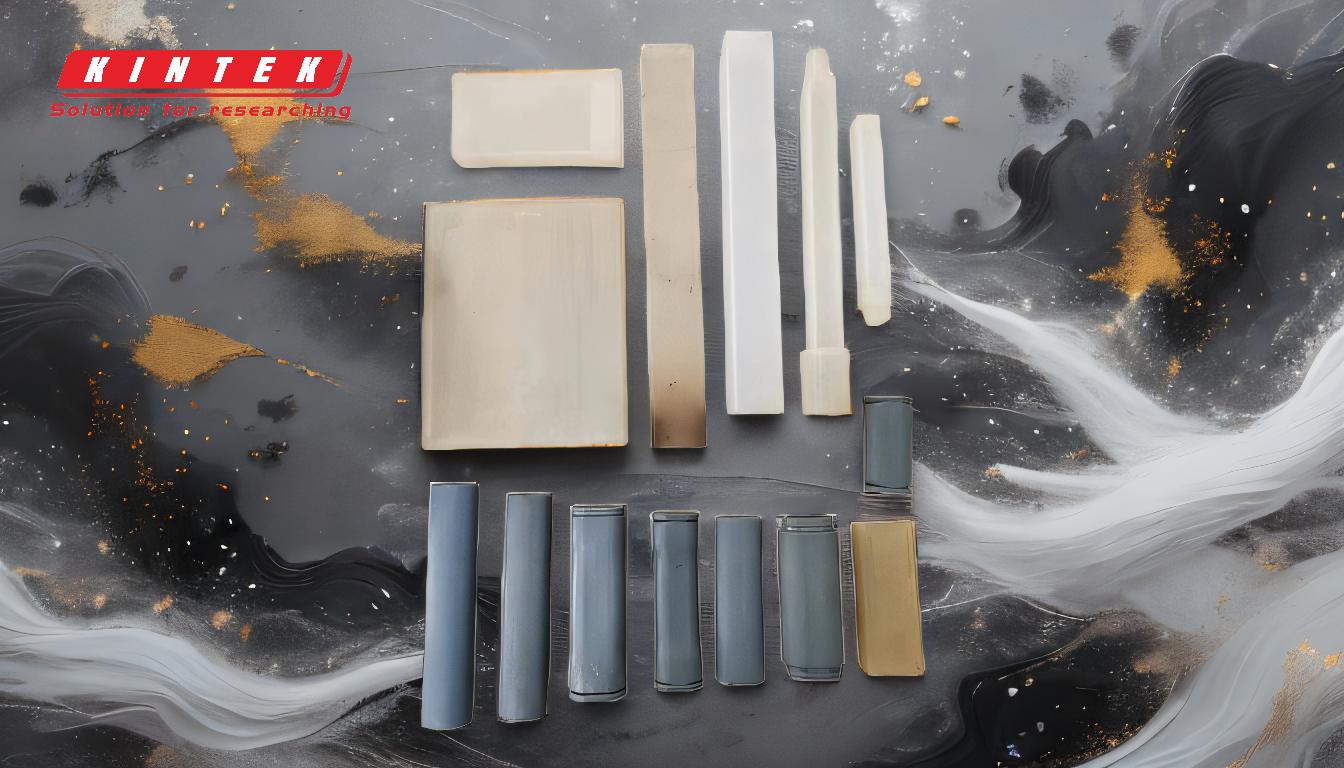
-
产品尺寸的变化:
- 说明:在挤压过程中,保持产品尺寸的一致性是一项挑战。温度波动、材料不一致和机器磨损等因素都会导致挤压产品的尺寸发生变化。
- 影响:这些差异可能导致产品不符合精确的规格要求,从而引发潜在的质量控制问题并增加浪费。对于航空航天或医疗设备等需要严格公差的行业来说,这可能是一个重大缺陷。
-
产品限制:
- 说明:挤压生产的产品通常在整个长度上具有均匀的横截面。这意味着一次只能获得一种横截面,限制了设计的灵活性。
- 影响:对于需要复杂几何形状或不同横截面的应用来说,这种限制可能是一个很大的缺点。例如,制作具有复杂形状或多种轮廓的零件需要额外的加工步骤,从而增加了时间和成本。
-
初始设置成本高:
- 说明:挤压设备和模具所需的初始投资可能很大。这包括挤压机、模具和其他必要工具的成本,以及建立生产线的相关费用。
- 影响:对于希望采用挤压工艺的中小型企业或初创企业来说,高昂的前期成本可能是一个障碍。此外,随着时间的推移,维护和更换模具的成本也会增加总支出,从而降低小批量生产的经济性。
总之,尽管挤压是一种多功能、高效的制造工艺,但也并非没有缺点。产品尺寸的变化、设计上的限制以及高昂的初始成本都是在为特定应用选择挤压工艺时需要考虑的重要因素。了解这些缺点有助于制造商做出明智的决定,并在必要时探索替代工艺。
汇总表:
缺点 | 说明 | 影响 |
---|---|---|
产品尺寸变化 | 温度波动、材料不一致和机器磨损会导致尺寸变化。 | 这会导致质量控制问题,增加浪费,并给公差要求严格的行业带来挑战。 |
产品限制 | 挤压产生均匀的横截面,限制了设计的灵活性。 | 复杂几何形状需要额外的加工步骤,增加了时间和成本。 |
初始设置成本高 | 设备、工具和生产线设置投资大。 | 对中小企业和初创企业来说是个障碍;对小批量生产来说不太经济。 |
需要帮助选择正确的制造工艺? 立即联系我们的专家 获取量身定制的解决方案!