双板模具虽然广泛用于注塑成型,但也有一些缺点,会影响生产效率、成本和设计灵活性。主要缺点包括浇口位置的限制,这限制了设计选择,并可能导致美观或功能上的妥协。此外,成型后需要移除流道系统,增加了劳动力和材料浪费,影响了整体效率和可持续性。下面,我们将详细探讨这些缺点,全面了解它们对设备和耗材采购商的影响。
要点解读:
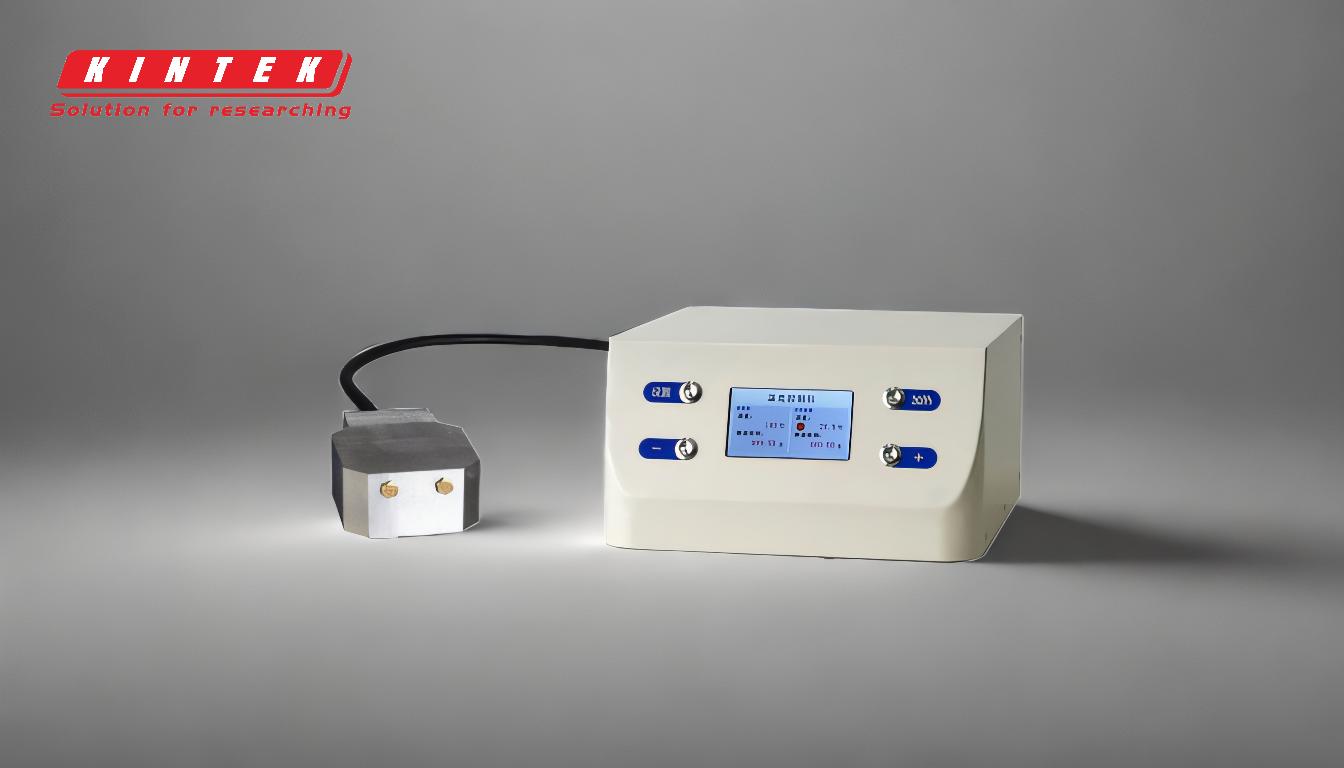
-
有限的闸门位置选择:
- 说明:在双板模具中,除非采取特殊措施,否则浇口(熔融塑料进入模腔的点)通常会被限制在零件的侧面。这种限制会影响最终产品的设计和功能。
-
影响:
- 设计限制:侧浇口可能不适合需要美观饰面的零件或具有复杂几何形状的零件。这会限制模具对不同产品设计的通用性。
- 复杂性增加:采取特殊措施将浇口安置在其他位置,会增加模具的复杂性和成本,使较简单的项目更不经济。
-
流道系统拆除:
- 说明:注塑成型后,必须将流道系统(熔融塑料流向模腔的通道)从成品部件上移除。这是一个增加生产周期的手动或半自动化过程。
-
影响:
- 劳动力成本增加:需要手动或使用额外的机器移除流道,增加了人工成本和生产时间。
- 材料浪费:流道系统通常在拆除后丢弃,造成材料浪费。这对于注重可持续发展的运营来说是一个重大问题。
- 后处理要求:去除过程可能需要额外的设备或步骤,如修剪或打磨,使生产工作流程更加复杂。
-
对生产效率的影响:
- 说明:有限的浇口位置和流道移除的共同作用会降低整体生产效率。
-
影响:
- 周期更长:需要移除流道和潜在的设计限制会延长生产周期,降低产量。
- 运营成本增加:劳动力增加、材料浪费以及对额外设备的潜在需求导致运营成本上升。
- 可扩展性问题:对于大规模生产而言,这些低效可能会变得非常明显,因此双板模具不太适合大批量生产。
-
材料考虑因素:
- 说明:注塑模具使用的材料类型会加剧双板模具的缺点。
-
影响:
- 材料兼容性:某些材料可能无法顺利通过侧浇口,导致最终产品出现缺陷或不一致。
- 热性能:具有特殊热特性的材料可能需要更精确的浇口位置,这对双板模具来说可能是个挑战。
-
替代解决方案:
- 说明:虽然双板模具有其缺点,但了解替代解决方案有助于减轻这些问题。
-
影响:
- 三板模具:这些模具可以更灵活地放置浇口和自动分离流道,从而减少劳动力和材料浪费。
- 热流道系统:这些系统使塑料在流道系统中保持熔融状态,从而无需移除流道,提高了效率并减少了浪费。
- 设计优化:与模具设计师密切合作,优化浇口位置和流道设计,有助于减少双板模具的一些缺点。
总之,虽然双板模具是注塑成型的常见选择,但其在浇口位置和流道移除需求方面的局限性会影响生产效率、成本和设计灵活性。了解这些缺点对于设备和耗材采购人员做出明智决策和探索更能满足其生产需求的替代解决方案至关重要。
汇总表:
缺点 | 说明 | 影响 |
---|---|---|
闸门位置选择有限 | 闸门通常被限制在侧面,影响设计和功能。 | - 美观/复杂几何形状的设计限制。- 模具成本增加。 |
流道系统拆除 | 注塑后手动或半自动拆除流道。 | - 人工成本较高。- 材料浪费。- 额外的后加工步骤。 |
对生产效率的影响 | 浇口限制和流道移除的综合影响。 | - 周期更长。- 运营成本更高。- 可扩展性挑战。 |
材料考虑因素 | 材料类型会加剧双板模具问题。 | - 与侧浇口的兼容性问题。- 热性能挑战。 |
替代解决方案 | 减轻双板模具缺点的备选方案。 | - 三板模具。- 热流道系统- 设计优化。 |
了解替代解决方案如何改善您的注塑成型工艺 今天就联系我们 获取专家建议!