间接电弧炉是电弧炉的一种,其中电弧不与被加热的材料直接接触。相反,电弧在两个电极之间产生,产生的热量通过辐射和对流传递到材料。这种方法可以更好地控制加热,通常用于需要精确温度控制的应用,例如金属熔化或某些化学品的生产。该炉通常由耐火材料衬里的室、电极和产生电弧的电源系统组成。
要点解释:
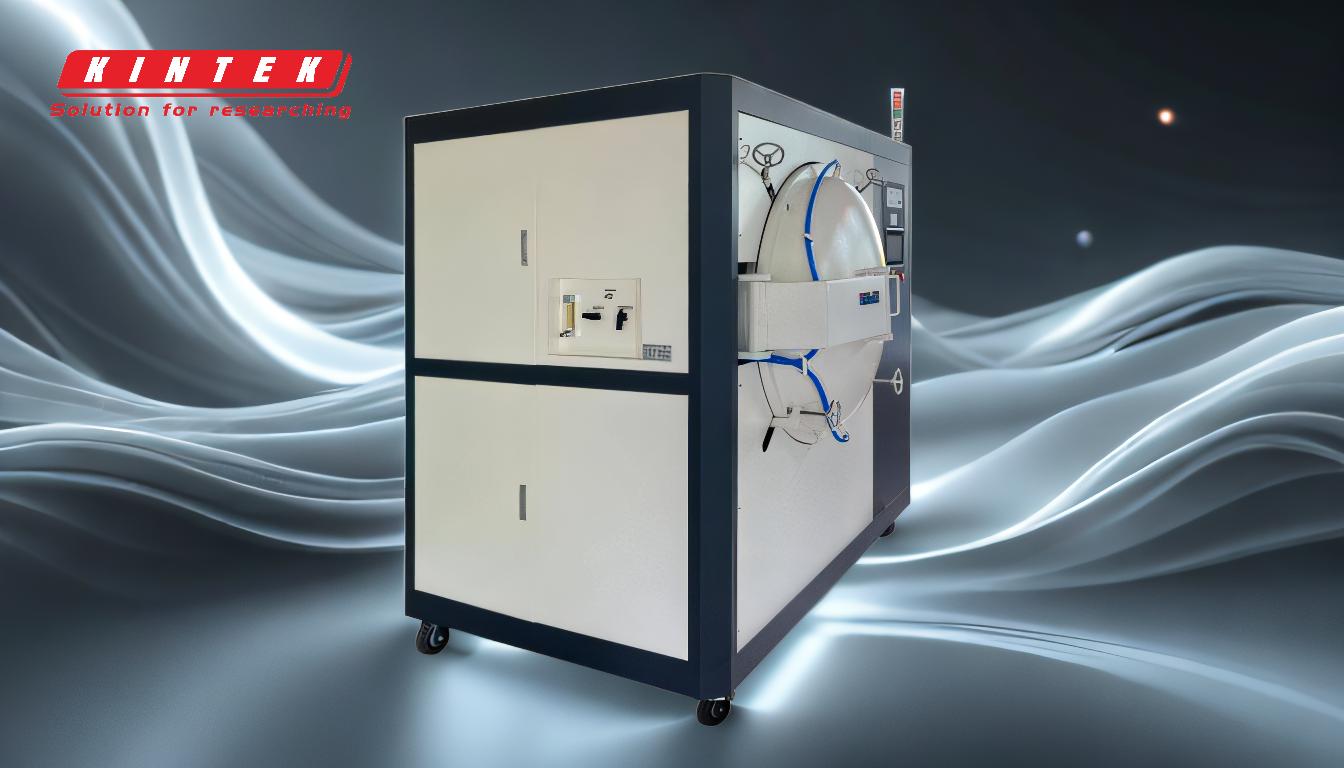
-
定义及基本原理:
- 间接电弧炉通过在两个电极之间产生电弧来运行。与直接电弧炉不同,电弧不与被加热的材料直接接触。相反,电弧产生的热量通过辐射和对流传递到材料。这种间接加热方法可以更精确地控制温度,使其适合需要仔细热管理的工艺。
-
间接电弧炉的组件:
- 耐火材料衬里室 :炉膛内衬有耐火材料,可承受高温并提供隔热作用以维持炉内的热量。
- 电极 :电极对于产生电弧至关重要。它们通常由能够承受高温和耐腐蚀的材料制成。
- 供电系统 :该系统将输入电压(通常为 220V 或 380V)转换为低电压和高电流,这是产生和维持电弧所必需的。
-
工作机制:
- 通过在正极和负极之间形成短路来引发电弧。电弧一旦建立,就成为一种自持放电现象,保持稳定燃烧而不熄灭。然后电弧产生的热量通过辐射和对流传递给炉内的材料,确保加热均匀。
-
应用领域:
- 金属熔化 :间接电弧炉通常用于金属熔化,特别是那些需要精确温度控制的金属,例如某些合金。
- 化学品生产 :这些熔炉还用于需要高温处理的化学品的生产,其中间接加热方法确保材料受热均匀,而无需直接暴露于电弧。
-
优点:
- 精确的温度控制 :间接加热方法可以更精确地控制温度,这对于需要特定热条件的工艺至关重要。
- 均匀加热 :通过辐射和对流方式均匀传递热量,保证物料受热均匀。
- 减少污染 :由于电弧不直接接触材料,因此电极污染的风险较小。
-
与其他炉子的比较:
- 直接电弧炉 :在直接电弧炉中,电弧与材料直接接触,这可以导致加热更快,但也增加了污染风险和温度控制精度较低。
- 等离子弧炉 :等离子电弧炉利用电弧加热器产生的低温等离子流来熔化材料。虽然它也提供高温,但传热机制不同,并且它可能无法提供与间接电弧炉相同水平的控制。
- 通道式感应炉 :通道感应炉利用电磁感应在材料本身内产生热量。这种方法对于熔化金属非常有效,但无法提供与间接电弧炉相同水平的温度控制。
总之,间接电弧炉是一种多功能、高效的加热设备,可提供精确的温度控制和均匀的加热,使其适用于各种工业应用,特别是金属熔化和化学生产。
汇总表:
方面 | 细节 |
---|---|
定义 | 通过辐射和对流间接传递热量的电弧炉。 |
关键部件 | 内衬耐火材料的室、电极、供电系统。 |
工作机制 | 电极之间的电弧间接加热材料,确保均匀加热。 |
应用领域 | 金属熔炼、化学生产。 |
优点 | 控温精确,加热均匀,减少污染。 |
比较 | 比直接电弧炉或槽式感应炉提供更好的控制。 |
了解间接电弧炉如何改善您的工业流程 — 今天联系我们 寻求专家建议!