等离子氮化是一种表面硬化工艺,用于提高金属部件的耐磨性、疲劳强度和耐腐蚀性。它是利用等离子放电将氮引入材料表面,形成坚硬的氮化层。这种工艺的优势在于它能在较低温度下工作,最大限度地减少变形并保持材料的核心强度。它适用于各种黑色和有色金属材料,是各种工业应用的多功能选择。
要点说明:
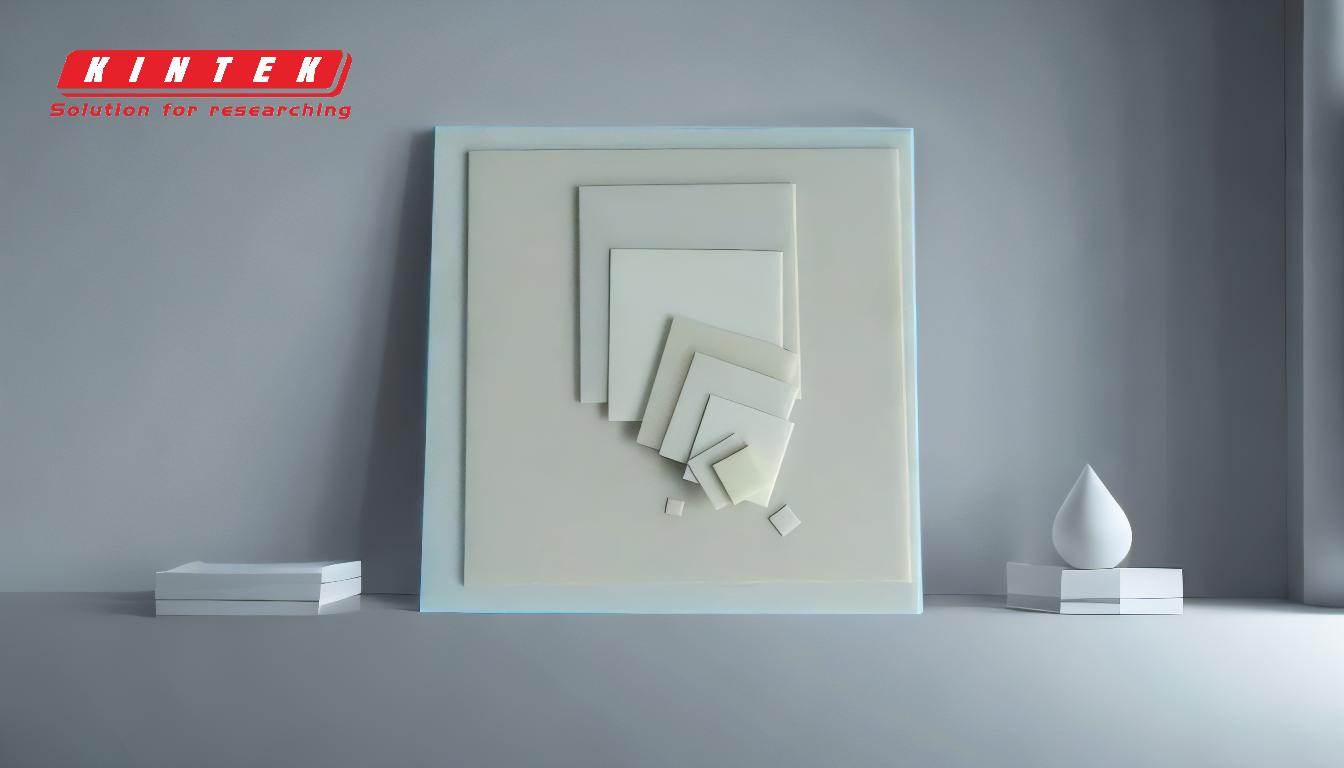
-
流程概述:
- 等离子氮化是一种热化学工艺,利用等离子放电将氮引入材料表面。
- 该工艺通常是将工件置于真空室中,通过在工件(阴极)和真空室壁(阳极)之间施加高压产生等离子体。
- 等离子体中的氮离子被加速冲向工件,穿透工件表面,形成坚硬的氮化层。
-
温度控制:
- 温度是等离子氮化的关键因素,因为它直接影响氮化过程的动力学。
- 该工艺可在相对较低的温度下进行(最高可达 350°C),这对于需要精确尺寸稳定性的材料尤为有利。
- 低温氮化可最大限度地减少变形,并保持低温淬火钢的高芯部强度。
-
等离子氮化的优点:
- 速度:等离子氮化比传统氮化技术更快,可缩短加工时间。
- 控制:适当控制温度、气氛成分和放电参数,可获得出色的微观结构,并更好地控制最终产品的表面成分、结构和性能。
- 环境影响:该工艺不会产生有害的副产品,因此对环境无害。
- 多功能性 可用于多种材料,包括黑色金属材料、烧结钢、铸铁、高合金工具钢、不锈钢、镍基合金、钛和铝合金。应用领域
-
: 等离子氮化可用于多种工业应用,包括齿轮、曲轴、凸轮轴、凸轮升程器、阀门零件、挤出机螺杆、压铸工具、锻造模具、冷成型工具、喷油器、塑料成型工具、长轴、车轴、联轴器和发动机零件。
- 该工艺尤其适用于需要高耐磨性、高疲劳强度和耐腐蚀性的部件。
- 与气体氮化的比较
-
: 气体氮化是将工件置于密封空间,通入氨气,然后将其加热至 500-580°C ,持续数小时至数十小时。
- 在 400°C 以上的温度下,氨分解成氢原子和活性氮原子,这些原子被钢表面吸收并向内部扩散,形成氮化层。
- 而等离子氮化的操作温度较低,对工艺参数的控制更好,因此氮化层更均匀、更可控。
- 材料兼容性
-
: 等离子氮化适用于所有黑色金属材料、烧结钢、铸铁、高合金工具钢、不锈钢、镍基合金、钛和铝合金。
- 这种广泛的材料兼容性使等离子氮化成为各种工业应用的多功能选择。
- 总之,等离子氮化是一种高效的表面硬化工艺,与传统氮化技术相比具有众多优势。
它能在较低温度下操作,加上对工艺参数的出色控制,使其成为提高各行业关键部件性能和使用寿命的首选。汇总表:
方面
详细信息 | 工艺流程 |
---|---|
利用等离子放电将氮气引入材料表面。 | 温度范围 |
可在低温(最高 350°C)下工作,最大限度地减少变形。 | 优点 |
比传统方法更快、控制精确、环保、用途广泛。 | 应用领域 |
齿轮、曲轴、凸轮轴、发动机零件等。 | 材料兼容性 |
黑色金属和有色金属材料,包括不锈钢和钛。 | 了解等离子氮化如何提高部件性能 |
立即联系我们的专家 ! !