喷涂和溅射是用于涂层和薄膜沉积的两种不同工艺,每种工艺都有独特的机制、应用和结果。喷涂通常是将液态材料雾化成细小的液滴并沉积到表面,通常用于喷漆、涂层或表面处理。另一方面,溅射是一种物理气相沉积(PVD)技术,原子在高能离子轰击下从固体目标材料中喷射出来,在基底上形成薄膜。它们的主要区别在于能量来源、材料状态、沉积机制以及所形成薄膜的特性。溅射具有附着力更强、薄膜更致密、对薄膜成分和厚度的控制更好等优点,因此适合半导体和光学镀膜等高精度应用。喷涂在大规模应用中用途更广,但可能缺乏溅射的精确性和均匀性。
要点说明:
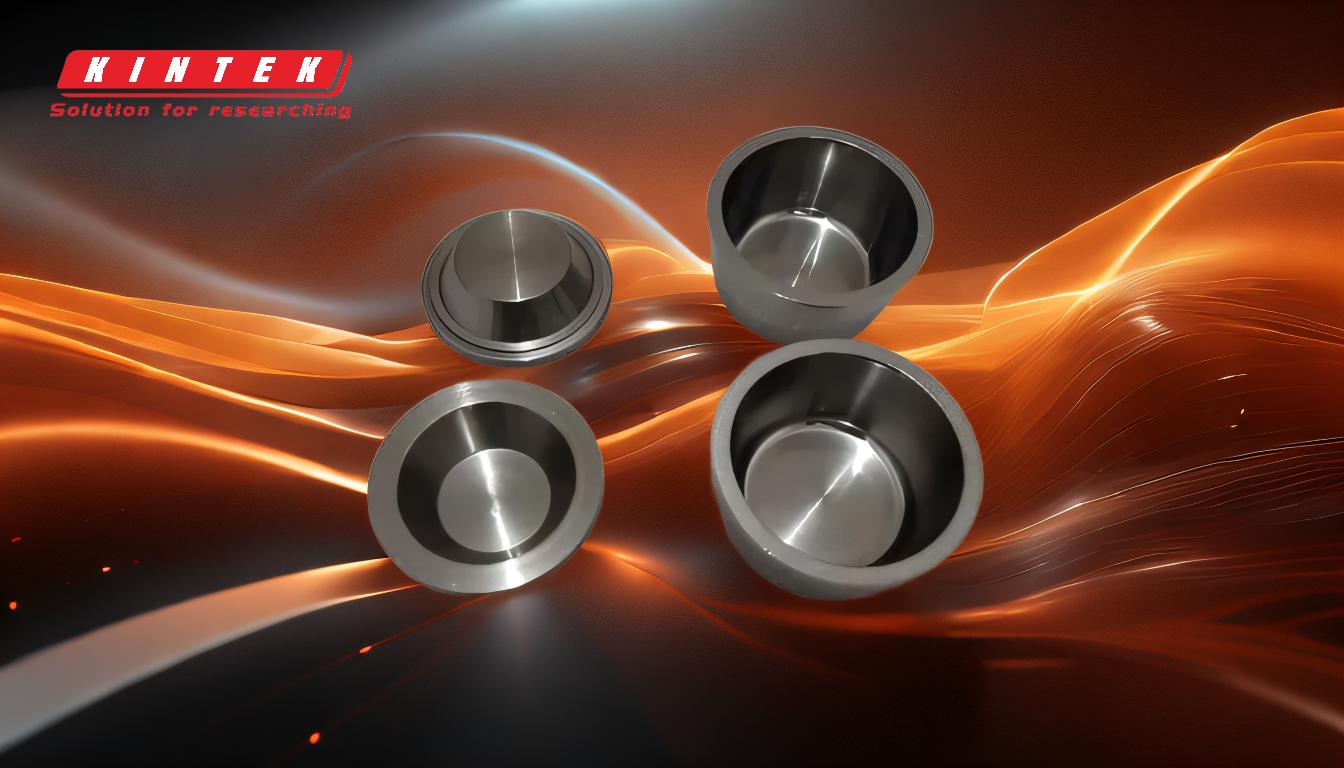
-
沉积机制:
- 喷涂:包括将液态材料(如油漆、涂料溶液)雾化成细小的液滴并沉积到表面。该工艺依靠机械力或气动力来分散材料。
- 溅射:PVD 工艺:高能离子轰击固体靶,从靶表面喷射出原子。然后这些原子沉积到基底上形成薄膜。该过程由等离子体生成和离子加速驱动。
-
材料状态:
- 喷涂:使用液态或半液态材料,通常是溶液、悬浮液或熔融金属。
- 溅射:使用固体目标材料,可以是金属、合金或绝缘体。材料以原子或分子形式射出。
-
能量来源:
- 喷涂:依靠机械能(如压缩空气)或热能(如熔融金属的加热)。
- 溅射:利用电能产生等离子体,并加速离子射向目标材料。
-
沉积速率和控制:
- 喷涂:通常具有较高的沉积速率,但对薄膜厚度和均匀性的控制不够精确。适用于大面积涂层。
- 溅射:可精确控制薄膜厚度和成分,同时降低沉积速率。是半导体和光学镀膜等高精度应用的理想选择。
-
薄膜特性:
- 喷涂:与溅射薄膜相比,生产的薄膜在附着力、密度和均匀性方面可能较低。适合精度要求不高的应用。
- 溅射:生成的薄膜具有更强的附着力、更高的密度和更好的均匀性。溅射薄膜还能更好地抵御氧化等环境因素的影响。
-
应用领域:
- 喷涂:常用于汽车(油漆涂层)、建筑(表面处理)和消费品(装饰涂层)等行业。
- 溅射:广泛应用于电子(半导体制造)、光学(抗反射涂层)和航空航天(保护涂层)。
-
环境条件:
- 喷涂:可在环境条件下或受控环境中进行,具体取决于材料和应用。
- 溅射:需要真空环境,以尽量减少污染并确保对沉积过程的精确控制。
-
材料多样性:
- 喷涂:仅限于可雾化并以液态沉积的材料。
- 溅射:可沉积多种材料,包括金属、合金和绝缘体,并可通过添加反应气体产生复杂的成分。
-
设备和成本:
- 喷涂:一般价格较低,设备简单,因此在大规模应用中具有成本效益。
- 溅射:需要更复杂和昂贵的设备,包括真空系统和等离子发生器,但薄膜质量和精度更高。
-
靶材和基片排列:
- 喷涂:布置灵活性较差,通常要求喷嘴与基底之间有直接视线。
- 溅射:由于溅射颗粒不受重力影响,可在复杂几何形状上均匀沉积,因此可灵活布置靶材和基底。
通过了解这些关键差异,设备和耗材采购人员可以根据其应用的具体要求(如精度、材料兼容性和成本考虑)做出明智的决定。
汇总表:
纵向 | 喷涂 | 溅射 |
---|---|---|
机理 | 将液体雾化成液滴,通过机械/气动力沉积。 | 在 PVD 过程中,利用高能离子将原子从固体目标中喷射出来。 |
材料状态 | 液体或半液体(溶液、悬浮液、熔融金属)。 | 固体目标材料(金属、合金、绝缘体)。 |
能量来源 | 机械能或热能。 | 电能(等离子体生成和离子加速)。 |
沉积速率 | 速率越高,控制越不精确。 | 速率较低,可精确控制厚度和成分。 |
薄膜特性 | 较低的附着力、密度和均匀性。 | 附着力更强、密度更高、均匀性更好。 |
应用领域 | 汽车、建筑、消费品。 | 半导体、光学、航空航天。 |
环境需求 | 环境或受控条件。 | 需要真空环境。 |
材料多样性 | 仅限于可雾化的液体。 | 材料范围广,包括金属、合金和绝缘体。 |
成本 | 设备价格较低,大规模应用成本效益高。 | 设备较贵,适合高精度应用。 |
基底排列 | 需要直接视线。 | 布置灵活,可在复杂几何形状上均匀沉积。 |
需要帮助为您的应用选择正确的涂层工艺吗? 立即联系我们的专家 获取量身定制的建议!