压缩成型是一种广泛用于生产高质量零件的制造工艺,尤其是在汽车、航空航天和消费品等行业。所使用的模具类型对最终产品的质量起着至关重要的作用。闪模因其简单和成本效益高而最常用,但根据所生产零件的具体要求,也会使用其他类型的模具,如正模、落地正模和半正模。每种模具类型都有其优势和局限性,选择取决于材料特性、零件复杂性和所需公差等因素。了解每种模具类型的细微差别及其在不同应用中的适用性,对于实现压模成型零件的一致质量至关重要。
要点说明:
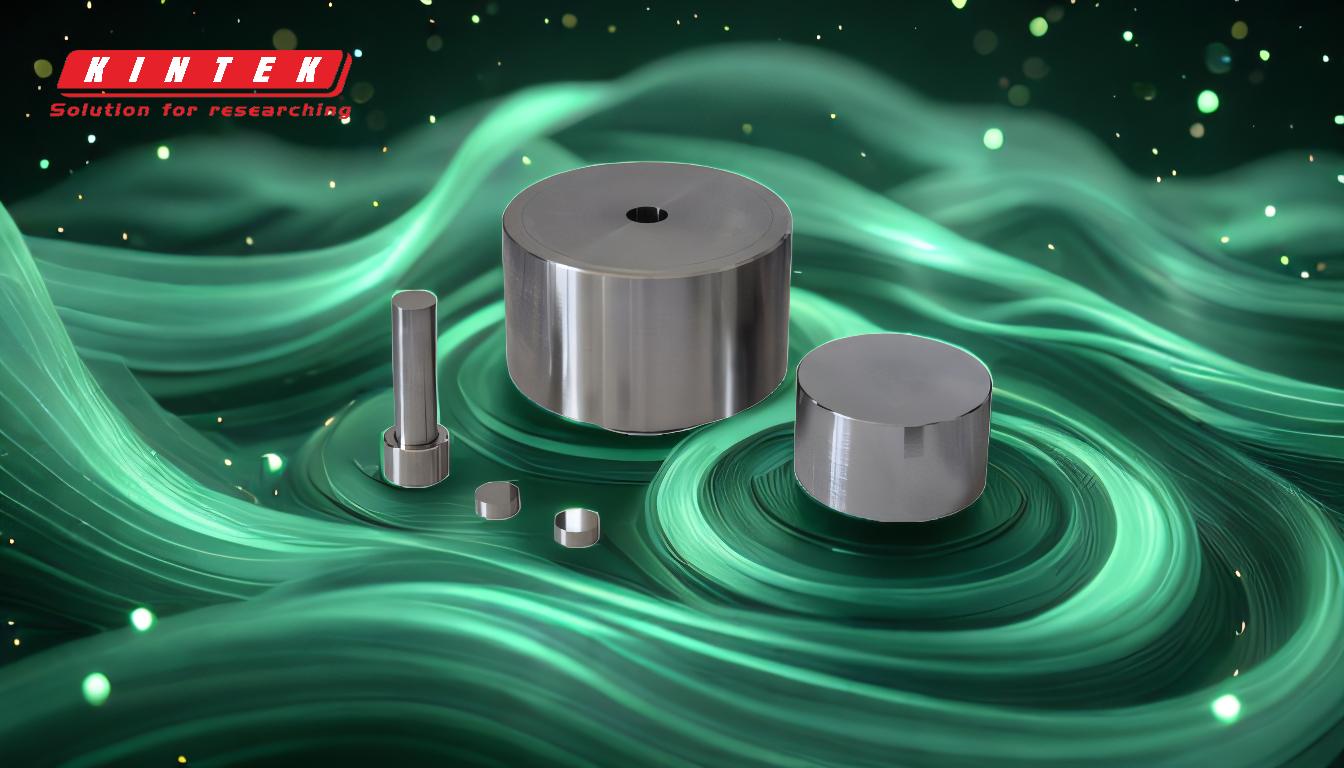
-
压缩模具的类型:
-
闪光模具:
- 最常用的模具类型,因其简单和成本效益高。
- 具有较小的溢流区(飞边),允许多余的材料溢出,确保型腔的适当填充。
- 适用于尺寸要求不严格的零件。
-
正模:
- 设计用于将所有材料容纳在型腔内,不会溢出。
- 非常适合生产公差小、飞边少的零件。
- 需要精确测量材料以避免缺陷。
-
落地正模:
- 闪模和正模的混合体。
- 在保持严格公差的同时,还包括一个控制飞边的小区域。
- 适用于既要求精度又要求尽量减少废料的零件。
-
半正模:
- 结合了闪模和正模的特点。
- 允许一定程度的溢流,同时更好地控制材料分布。
- 适用于公差适中、需要尽量减少材料浪费的零件。
-
闪光模具:
-
材料考虑因素:
-
批量成型:
- 包括填料、催化剂、稳定剂、颜料和纤维增强剂的混合物。
- 适用于生产机械性能更强的部件。
-
板材成型:
- 使用预先切割好的材料片,将其放入模腔。
- 非常适合需要均匀厚度和一致材料分布的零件。
-
批量成型:
-
压缩成型的挑战:
-
材料测量:
- 准确切割或称量橡胶原料至关重要。
- 材料不足会导致流线、起泡或未填充部件等缺陷。
-
材料放置:
- 不正确的放置会导致材料分布不均,造成缺陷。
-
材料过多:
- 材料过多会造成严重的飞边,难以去除,并影响零件的外观和功能。
-
材料测量:
-
选择正确的模具类型:
-
部件复杂性:
- 具有复杂细节的复杂零件可能需要正模或落地正模,以确保精确的材料分布。
-
公差要求:
- 公差要求严格的零件最好使用正模或落地正模生产。
-
材料特性:
- 所用材料的类型(块状或片状)会影响模具类型的选择。
-
产量:
- 大批量生产可能更青睐闪模,因为闪模操作简单,成本较低。
-
部件复杂性:
-
质量控制:
-
预防缺陷:
- 正确的材料测量和放置是避免缺陷的关键。
-
闪光管理:
- 管理闪光灯对于保持零件质量和减少后处理工作量至关重要。
-
一致性:
- 稳定的材料分布和模具设计是生产高质量零件的关键。
-
预防缺陷:
通过了解不同类型的压缩模具及其各自的优势和挑战,制造商可以做出明智的决定,从而高效地生产出高质量的零件。模具类型的选择应基于零件的具体要求,包括其复杂性、公差要求和材料特性。正确的材料处理和模具设计对于实现压塑成型零件的稳定质量至关重要。
汇总表:
模具类型 | 关键功能 | 最佳使用案例 |
---|---|---|
闪模 | 简单、经济、溢流面积小,可容纳多余材料 | 尺寸要求不严格的零件 |
正模 | 无溢流,需要精确的材料测量 | 零件公差小,飞边少 |
正极着地 | 混合设计,控制闪光的占地面积小 | 要求精确的部件,尽量减少浪费 |
半正向 | 兼具闪光和正向特征,允许一定程度的溢流 | 零件公差适中,材料浪费最小 |
材料类型 | 散装模塑:增强机械性能; 板材成型:厚度均匀 | 根据零件要求和材料特性进行选择 |
需要帮助为您的压缩成型工艺选择合适的模具? 立即联系我们的专家 获取量身定制的解决方案!