CVD(化学气相沉积)和 PVD(物理气相沉积)是两种广泛使用的薄膜沉积技术,每种技术都有其自身的优点和局限性。 CVD 和 PVD 之间的选择取决于具体应用、材料要求和操作限制。 CVD 更适合在复杂几何形状和高温环境中需要均匀涂层的应用,而 PVD 则非常适合温度敏感材料和需要更快沉积速率的应用。下面,我们探讨这两种方法的主要区别、优点和局限性,以帮助确定哪种方法更适合特定用例。
要点解释:
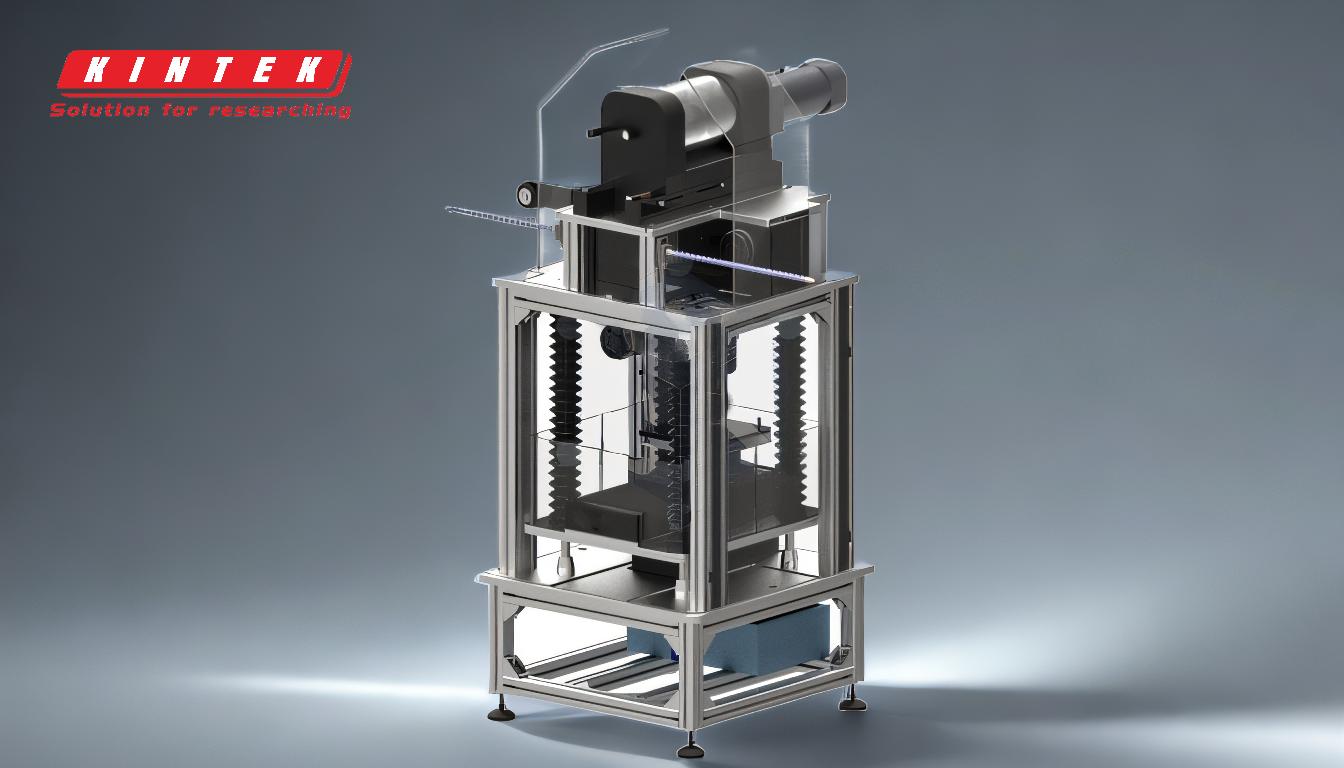
-
沉积机制:
- CVD :涉及气态前体和基材表面之间的化学反应,形成固体涂层。该过程是多方向的,即使在复杂的几何形状和深孔中也能实现均匀的覆盖。
- 物理气相沉积 :依靠溅射或蒸发等物理过程将固体材料沉积到基材上。这是一个视线过程,这意味着它对于涂覆阴影区域或复杂形状的效果较差。
-
工作温度:
- CVD :在较高温度(450°C 至 1050°C)下工作,因此不适合某些聚合物或低熔点基材等温度敏感材料。
- 物理气相沉积 :在较低温度(250°C 至 450°C)下工作,使其成为温度敏感材料的更好选择。
-
涂层材料范围:
- CVD :主要用于沉积陶瓷和聚合物。它可以利用挥发性化合物,使难以蒸发的元素能够沉积。
- 物理气相沉积 :可以沉积更广泛的材料,包括金属、合金和陶瓷,使其更适合各种应用。
-
涂层均匀性和密度:
- CVD :通过化学反应过程产生更致密、更均匀的涂层,即使在复杂的几何形状中也能确保彻底覆盖。
- 物理气相沉积 :涂层密度较低且不太均匀,但可以更快地涂覆,使其适合速度至关重要的应用。
-
视线限制:
- CVD :不受视线影响的限制,允许在深孔、阴影区域和复杂的几何形状中进行涂层沉积。
- 物理气相沉积 :受视线限制,对于涂覆复杂形状或未直接暴露于沉积源的区域的效果较差。
-
能源消耗和热约束:
- CVD :需要高能源成本来加热气相和底物,这在运营费用和环境影响方面可能是不利的。
- 物理气相沉积 :在真空和较低温度下运行,降低能耗,更适合温度敏感的应用。
-
应用领域:
- CVD :常用于半导体制造、光电子以及需要高纯度、均匀涂层的应用。
- 物理气相沉积 :广泛应用于装饰涂料、耐磨涂料以及涉及温度敏感材料的应用。
-
材料浪费:
- CVD :由于仅对加热区域进行涂层,因此产生的材料浪费更少。计算机控制激光器等先进技术可以进一步增强选择性涂层。
- 物理气相沉积 :由于物理沉积过程的性质,可能会导致更多的材料浪费。
-
薄膜厚度和光滑度:
- CVD :通常可生产更厚、更光滑的薄膜,非常适合需要高耐用性和精度的应用。
- 物理气相沉积 :生产平滑度较低的较薄薄膜,适合优先考虑速度和多功能性的应用。
-
成本和复杂性:
- CVD :操作更容易,不需要复杂的设置,但高能源成本和热限制会增加运营费用。
- 物理气相沉积 :需要真空环境,这会增加设置的复杂性和成本,但它提供更快的沉积速率和更低的能耗。
总之,CVD 和 PVD 之间的选择取决于应用的具体要求。 CVD更适合需要均匀涂层的高温、高精度应用,而PVD更适合温度敏感材料和需要更快沉积速率的应用。两种方法都有其独特的优点和局限性,决策应基于对操作和材料要求的彻底评估。
汇总表:
方面 | CVD | 物理气相沉积 |
---|---|---|
沉积机制 | 化学反应,多方位,均匀覆盖 | 物理过程、视线,对于复杂形状效果较差 |
工作温度 | 高(450°C至1050°C),不适合温度敏感材料 | 低(250°C 至 450°C),非常适合温度敏感材料 |
涂层材料范围 | 主要是陶瓷和聚合物 | 金属、合金、陶瓷、更广泛的材料多样性 |
涂层均匀性 | 涂层更致密、更均匀 | 密度较低、均匀性较差,但沉积速率较快 |
视线 | 不限,对复杂几何形状有效 | 有限,对阴影区域效果较差 |
能源消耗 | 高温导致能源成本高 | 能耗低,真空操作 |
应用领域 | 半导体、光电、高纯涂料 | 装饰、耐磨、温度敏感应用 |
材料浪费 | 减少浪费,选择性涂层技术 | 物理沉积过程产生更多浪费 |
膜厚 | 更厚、更光滑的薄膜 | 更薄、不太光滑的薄膜 |
成本和复杂性 | 设置更简单,运营成本更高 | 复杂的真空设置、更快的沉积、更低的能源成本 |
仍然不确定哪种薄膜沉积技术适合您的应用? 立即联系我们的专家 寻求个性化建议!