溅射技术在材料沉积过程中具有若干优缺点。
溅射技术的优点
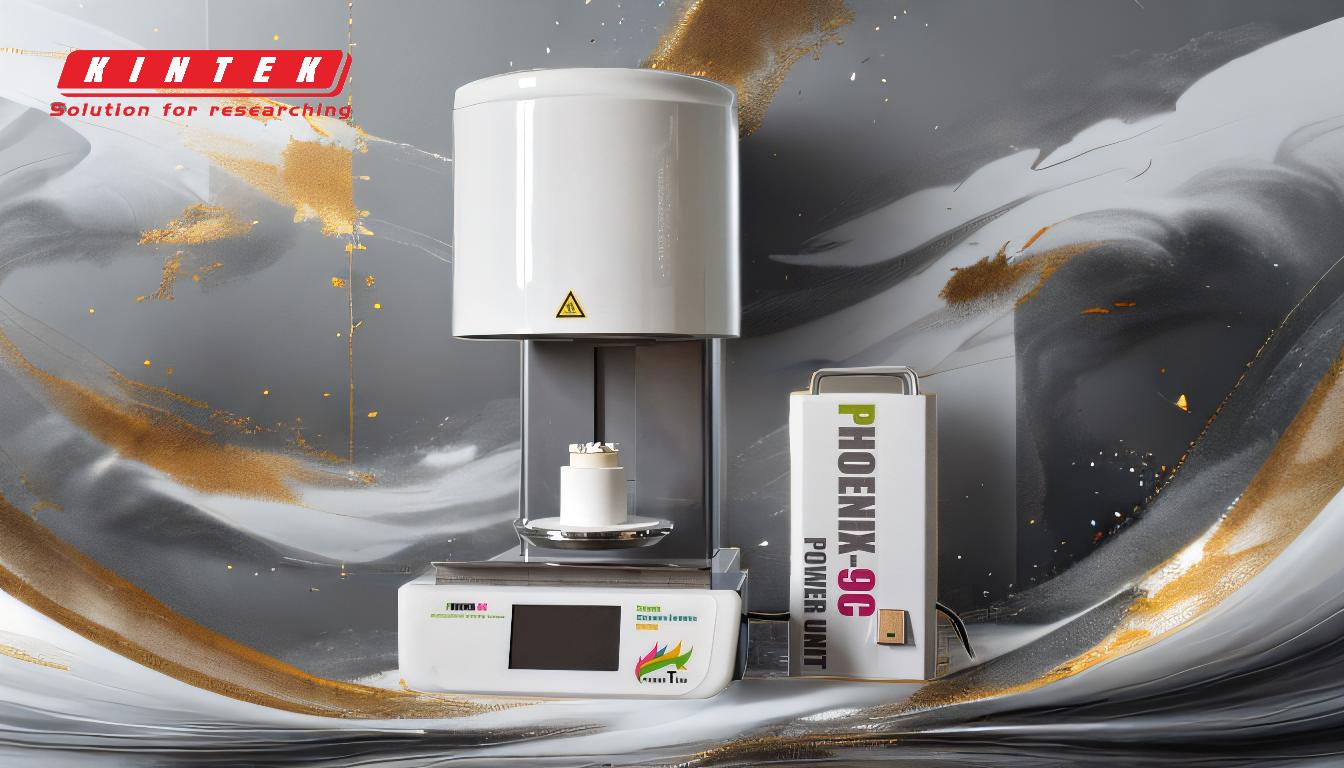
1.材料的多样性
溅射可以沉积多种材料,包括元素、合金和化合物。在需要不同材料特性的各种工业应用中,这种多功能性至关重要。
2.稳定的蒸发源
溅射靶材提供了稳定而持久的汽化源,可确保长期稳定的材料沉积。
3.可配置的溅射源
在某些配置中,溅射源可被塑造成特定的形状,如线条或棒或圆柱的表面,这有利于实现有针对性的沉积。
4.反应沉积
溅射可以使用等离子体中激活的反应性气体物种进行简单的反应沉积,这对于生成特定的化学成分或化合物非常有利。
5.辐射热最小
该工艺产生的辐射热极低,这对温度敏感的基底非常有利。
6.设计紧凑
溅射室可以设计得很小,适合空间有限的应用。
溅射技术的缺点
1.资本支出高
溅射设备的初始设置和维护成本较高,这可能成为小型公司或研究团体的障碍。
2.某些材料的沉积率低
某些材料(如二氧化硅)的沉积率相对较低,这可能会减慢生产流程。
3.材料降解
某些材料,尤其是有机固体,在溅射过程中容易因离子轰击而降解。
4.杂质引入
与蒸发技术相比,溅射技术由于真空度较低,往往会在基底中引入更多杂质。
5.磁控溅射的具体缺点
- 靶材利用率低: 磁控溅射中的环形磁场会导致不均匀的侵蚀模式,从而降低靶材利用率,一般低于 40%。
- 等离子体不稳定性: 这会影响沉积过程的一致性和质量。
- 无法在低温下对强磁材料进行高速溅射: 造成这种限制的原因是无法在靶材表面附近有效地施加外部磁场。
6.难以与升空相结合
溅射的弥散性使其难以与掀离技术相结合来构建薄膜,从而导致潜在的污染问题。
7.主动控制挑战
与脉冲激光沉积等技术相比,溅射技术中的逐层生长控制更为困难,而且惰性溅射气体可能作为杂质嵌入生长的薄膜中。
总之,尽管溅射技术在材料多样性和沉积控制方面具有显著优势,但它在成本、效率和流程控制方面也面临挑战,特别是在磁控溅射等特定配置中。必须根据应用的具体要求仔细考虑这些因素。
继续探索,咨询我们的专家
利用 KINTEK SOLUTION 技术充分挖掘材料沉积工艺的潜力KINTEK SOLUTION 先进的溅射技术!了解我们最先进的设备如何提高您的多功能性、优化沉积速率并最大限度地减少材料降解。利用我们系统提供的精度和控制能力,将您的研究和工业项目提升到新的高度。探索我们全系列的溅射解决方案,亲身体验 KINTEK 的独特之处 - 您的卓越材料沉积之旅从这里开始!