类金刚石碳(DLC)涂层因其高硬度、低摩擦和耐磨损等优异性能而广受认可。然而,它们也有一些缺点,可能会限制其在某些情况下的适用性。其中包括与沉积工艺、材料兼容性和特定条件下的性能有关的挑战。在考虑将 DLC 涂层用于各种应用时,了解这些局限性对于做出明智的决策至关重要。
要点说明:
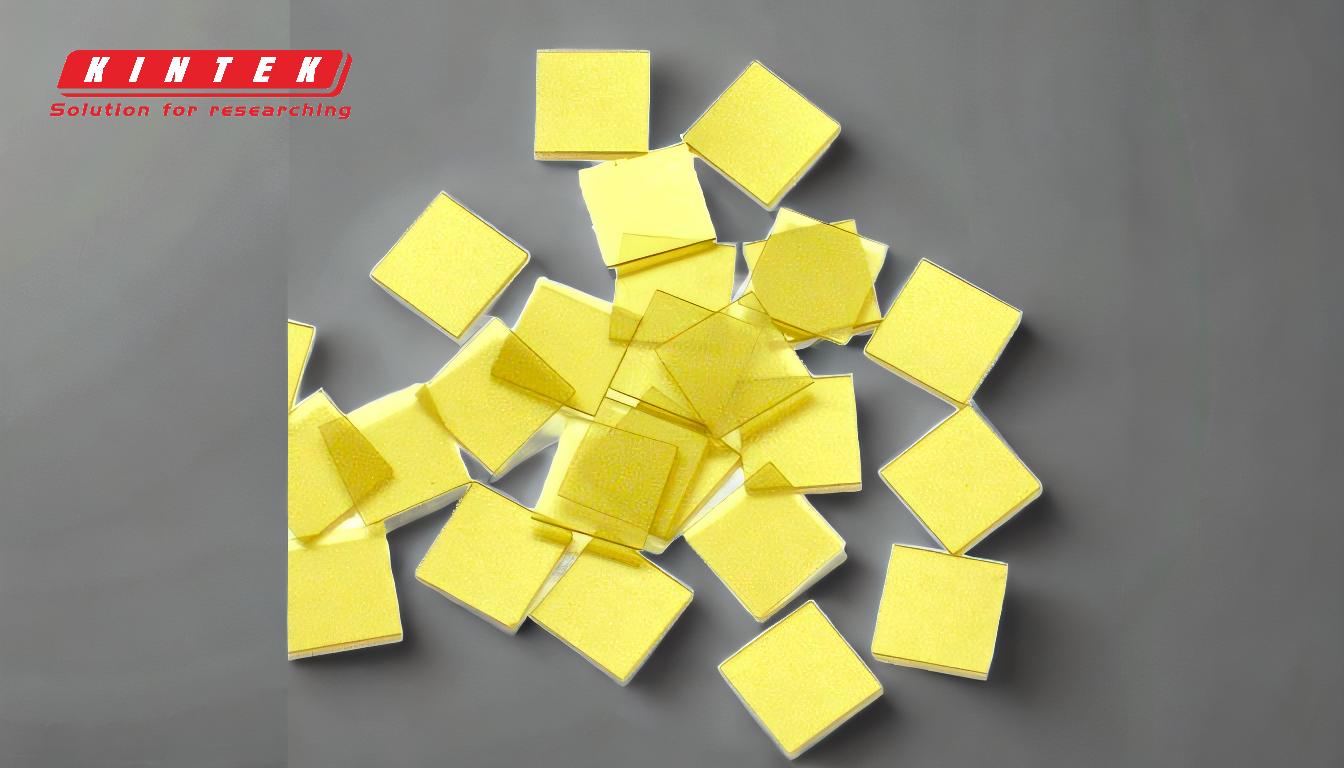
-
沉积过程的限制:
- 高加工温度:DLC 涂层,尤其是通过化学气相沉积 (CVD) 技术进行涂覆的 DLC 涂层,通常需要较高的加工温度(800-1000 °C)。这就限制了它们只能用于能承受这种高温的材料,如硬质合金。许多材料,尤其是聚合物和某些金属,都无法承受这样的温度,从而限制了其应用范围。
- 遮蔽困难:CVD 涂层难以遮蔽,通常会造成全涂或全不涂。这意味着对特定区域进行选择性镀膜具有挑战性,当部件只有某些部分需要镀膜时,这可能是一个重大缺陷。
- 尺寸限制:可喷涂部件的尺寸受到反应室容量的限制。大型或复杂的部件可能需要分解成更小的部件,从而使工艺复杂化并增加成本。
-
涂层厚度和应力问题:
- 厚涂层和拉伸应力:DLC 涂层,尤其是通过 CVD 技术形成的涂层,厚度可能相对较厚(10-20 μm)。在冷却过程中,这些厚涂层会产生拉伸应力,导致细小裂纹。这些裂纹可能会在外部冲击下扩展,导致涂层脱落。这就使得 DLC 涂层不太适合涉及间断切削过程的应用,如铣削,在这种情况下涂层更容易失效。
- 附着力挑战:DLC 涂层在某些基材上的附着力可能存在问题,尤其是在基材材料与高温不兼容或表面处理不当的情况下。附着力差会导致分层和涂层性能降低。
-
特定条件下的性能限制:
- 中断切割过程:DLC 涂层不适合用于铣削等断续切削工艺。在这种加工过程中,反复的冲击和热循环会加剧裂纹的形成,导致涂层失效。这就限制了它们在某些机加工应用中的使用,因为在这些应用中,其他涂层的性能可能会更好。
- 氢含量和稳定性:有些 DLC 涂层含有氢,这会影响其稳定性和性能,尤其是在高温下。氢化 DLC 涂层在高温下可能会降解或失去性能,从而限制了其在高温应用中的使用。
-
成本和复杂性:
- 沉积成本高:沉积 DLC 涂层(尤其是通过 CVD)所需的设备和工艺既复杂又昂贵。这使得 DLC 涂层在某些应用中成本过高,尤其是与其他涂层相比。
- 工艺复杂性:需要高温、专用设备和精确控制沉积参数,增加了工艺的复杂性。这可能会增加生产时间和成本,从而降低 DLC 涂层在大批量或低成本应用中的吸引力。
-
材料兼容性和应用范围:
- 有限的基底兼容性:DLC 涂层并非与所有材料普遍兼容。例如,它们可能不能很好地附着在某些金属或聚合物上,从而限制了它们在这些材料普遍存在的应用中的使用。
- 应用范围受限:由于上述限制,DLC 涂层通常仅限于其独特性能(如低摩擦和高耐磨性)至关重要的特定应用。在其他情况下,替代涂层可能更为合适。
总之,虽然 DLC 涂层在硬度、减少摩擦和耐磨性方面具有显著优势,但也有明显的缺点。其中包括与沉积工艺、涂层厚度和应力、特定条件下的性能、成本和材料兼容性有关的挑战。要为特定应用选择合适的涂层并确保最佳性能和耐用性,了解这些限制因素至关重要。
汇总表:
缺点 | 说明 |
---|---|
加工温度高 | 需要 800-1000 °C,仅限于耐热材料。 |
遮蔽困难 | 选择性喷涂具有挑战性;通常会导致全涂或全不涂。 |
尺寸限制 | 受反应室尺寸限制,使大型或复杂组件变得复杂。 |
厚涂层和拉伸应力 | 厚涂层(10-20 μm)在应力作用下会开裂,导致剥落。 |
附着力挑战 | 与某些基材的粘附性差会导致分层。 |
切割过程中断 | 由于反复冲击会形成裂纹,因此不适合用于铣削。 |
氢含量和稳定性 | 氢化涂层在高温下可能会降解。 |
沉积成本高 | 复杂昂贵的设备增加了总体成本。 |
基底兼容性有限 | 并非与所有材料普遍兼容,限制了应用范围。 |
需要帮助选择适合您应用的涂料吗? 立即联系我们的专家 !