感应加热器虽然高效且用途广泛,但也有一些缺点,会影响其可用性和成本效益。这些缺点包括:需要专用且通常价格昂贵的感应器、高电流密度管理、感应炉缺乏精炼能力、对复杂工件的适应性差、初始投资大以及需要技术熟练的人员。此外,感应加热主要用于表面加热,这可能会限制其在某些热处理工艺中的应用。在考虑将感应加热技术用于特定应用时,了解这些缺点对于做出明智决策至关重要。
要点说明:
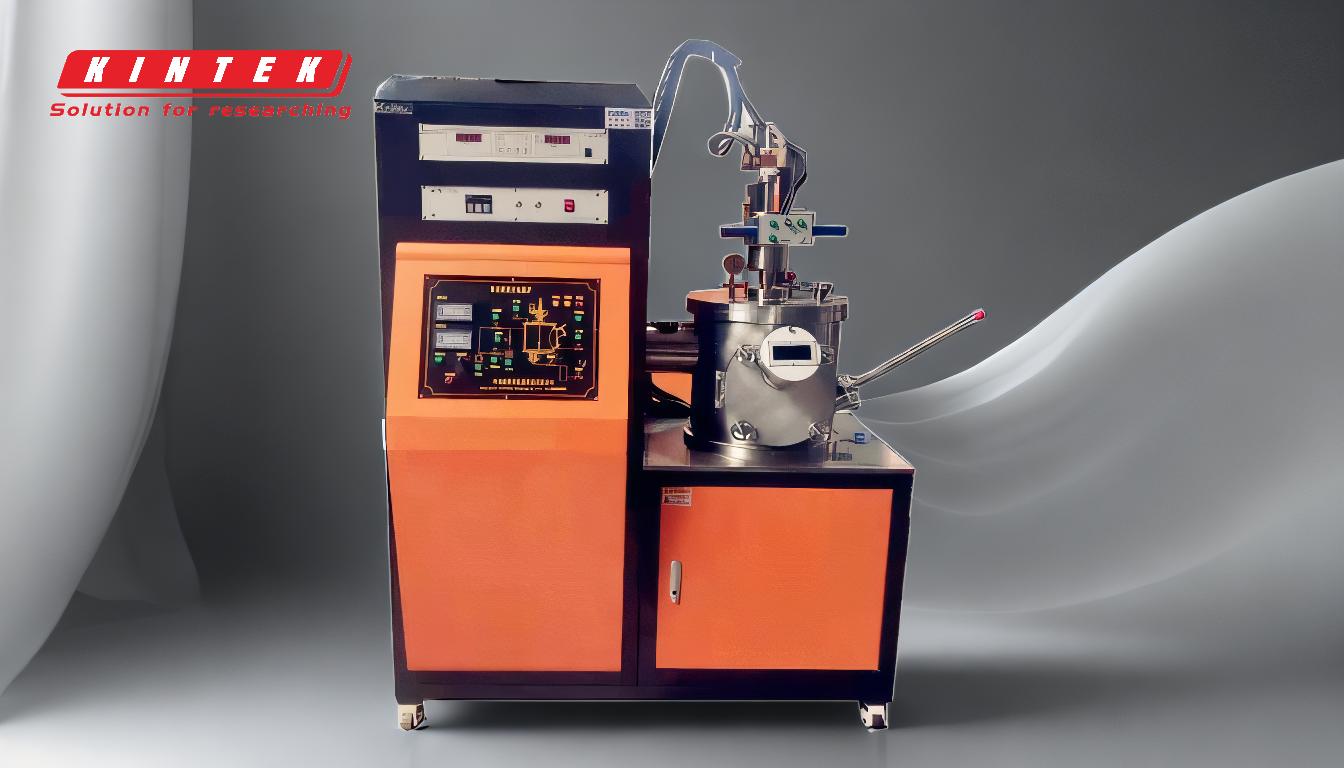
-
需要专用电感器:
- 感应加热需要生产针对特定应用的专用电感器。这种定制既昂贵又耗时,限制了技术的灵活性。
- 举例来说:对于不同形状和尺寸的工件,必须设计和制造独特的电感器,从而增加初始成本和持续成本。
-
高电流密度管理:
- 在小型铜电感器中管理高电流密度是一项重大挑战。这通常需要专门的工程设计和精确的 "铜配",以确保高效运行并防止过热。
- 举例说明:高电流密度会导致感应器磨损加剧,需要经常维护和更换。
-
感应炉缺乏精炼能力:
- 感应炉不具备精炼材料的能力。装料材料必须不含氧化物,且成分已知,这在某些工业流程中可能会受到限制。
- 例如:在金属熔化应用中,炉料中存在的任何氧化物都可能导致合金元素的损失,因此必须在熔体中重新添加合金元素。
-
对复杂工件的适应性差:
- 感应淬火技术不适合复杂的机械零件。它主要适用于装配线生产中的简单工件。
- 举例说明:复杂的几何形状和复杂的设计可能无法实现均匀加热,导致淬火结果不一致。
-
初期投资巨大:
- 建立感应加热系统的初始成本可能很高,包括专用设备和电源的费用。
- 举例来说:购买和安装感应炉以及必要的电源转换器和控制系统需要大量的前期投资。
-
对技术人员的要求:
- 操作感应加热系统需要具备感应加热原理和安全程序专业知识的熟练人员。
- 举例说明:要确保安全高效地操作,必须进行适当的培训并积累经验,这可能会增加总体成本和复杂性。
-
主要用于表面加热:
- 感应加热对表面加热最有效,这可能会限制其在某些要求整个材料均匀加热的热处理工艺中的应用。
- 举例来说:对于需要深层加热的工艺,如厚截面的通透硬化,感应加热可能不是最合适的方法。
-
控制和优化挑战:
- 需要采用可靠的控制算法来管理不同的感应加热负载和工作点。多线圈系统在控制和优化方面面临更多挑战。
- 例如采用具有自适应算法的实时识别控制单元可以提高性能,但会增加系统的复杂性和成本。
了解这些缺点对于评估感应加热技术在特定应用中的适用性以及确保利大于弊至关重要。
汇总表:
缺点 | 说明 | 示例 |
---|---|---|
需要专用电感器 | 定制电感器的生产成本高且耗时。 | 不同工件形状所需的独特电感器会增加成本。 |
大电流密度管理 | 管理小型电感器中的大电流具有挑战性,需要高精度。 | 高电流密度会导致磨损,需要经常维护。 |
缺乏精炼能力 | 感应炉无法精炼材料,需要预先清洗炉料。 | 炉料中的氧化物会导致合金流失,需要重新添加。 |
对复杂工件的适应性差 | 对复杂几何形状的适应性有限。 | 加热不一致导致零件复杂。 |
初始投资巨大 | 设备和电源的安装成本高。 | 感应炉和控制系统需要大量前期费用。 |
对熟练人员的要求 | 安全高效的操作需要熟练的操作人员。 | 培训会增加操作成本和复杂性。 |
主要用于表面加热 | 仅限于表面加热,不适合深度渗透。 | 不适合贯穿硬化厚截面。 |
控制和优化挑战 | 多线圈系统需要复杂的算法。 | 自适应控制单元增加了系统的复杂性和成本。 |
需要帮助确定感应加热是否适合您的应用? 立即联系我们的专家 获取个性化建议!