渗氮和渗碳都是用于提高金属表面性能的表面淬火工艺,但它们在应用、优缺点方面有明显的不同。氮化虽然具有提高硬度、耐磨性和疲劳寿命等优点,但与渗碳相比也有一些缺点。这些缺点包括对表面深度、材料兼容性、加工温度和后处理要求的限制。下面,我们将详细探讨渗氮与渗碳相比的主要缺点。
要点说明:
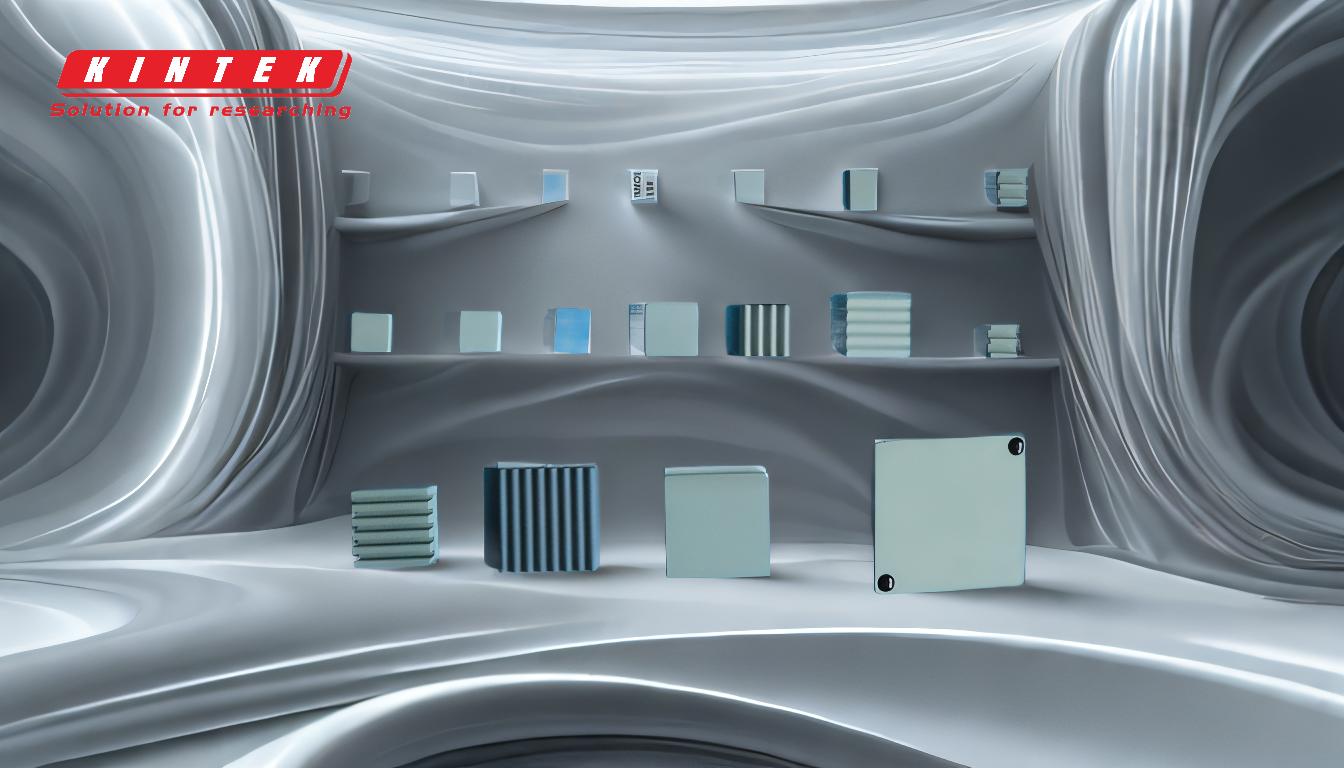
-
有限的表面深度
- 与渗碳相比,氮化的表面深度通常较薄。
- 渗碳的表面深度可从 0.5 毫米到 2 毫米甚至更深,具体取决于加工时间和材料。
- 而氮化处理的表面深度通常在 0.1 毫米到 0.6 毫米之间,这对于需要较深硬化层的应用来说可能是不够的。
- 这种限制使得氮化不太适合需要较厚淬硬层的高磨损或重载零件。
-
材料兼容性
- 氮化主要对特定合金钢有效,如含铬、钼和铝的合金钢,这些合金钢会形成硬氮化物。
- 而渗碳可用于更广泛的低碳钢和合金钢,因此用途更广。
- 渗氮对材料兼容性的限制限制了它在使用多种钢材的行业中的应用。
-
工艺温度较低
- 与渗碳(通常为 850°C 至 950°C)相比,氮化的温度相对较低(通常为 500°C 至 570°C)。
- 虽然较低的温度可以减少变形和能耗,但同时也限制了氮气向金属中的扩散,导致渗氮深度较浅。
- 渗碳的温度较高,碳扩散较深,因此对于需要显著表面硬化的应用更为有效。
-
后处理要求
- 渗氮不需要在加工后进行淬火,这降低了变形的风险。
- 但是,与渗碳零件相比,氮化零件不需要淬火,这意味着氮化零件的芯部硬度可能较低,因为渗碳零件需要经过淬火和回火才能获得坚硬的表面和坚韧的芯部。
- 这种限制会影响氮化部件的整体机械性能,尤其是在高应力应用中。
-
表面光洁度和美观
- 氮化处理有时会形成脆性 "白层"(氮化铁化合物层),导致表面光洁度降低,影响美观。
- 这一层可能需要额外的后处理,如研磨或抛光,才能达到理想的表面质量。
- 渗碳后再进行淬火和回火,通常会产生更光滑、更均匀的表面光洁度,从而减少了额外精加工步骤的需要。
-
成本和复杂性
- 氮化工艺,如气体氮化或等离子氮化,与渗碳相比可能更加复杂和昂贵。
- 由于需要精确控制含氮气氛或等离子环境,因此增加了设备和操作成本。
- 渗碳作为一种更成熟、应用更广泛的工艺,通常更具成本效益,也更容易在大规模生产环境中实施。
-
特定应用的限制
- 渗氮主要是对表面进行硬化,对于需要通过硬化或承受高冲击载荷的零件效果较差。
- 渗碳具有更深的表面深度,能够同时硬化表面和芯部,因此更适合此类应用。
- 此外,氮化零件的韧性可能会降低,因此不太适合动态或高冲击环境。
总之,氮化虽然具有减少变形和提高耐磨性等优点,但其缺点--如有限的表面深度、有限的材料兼容性和较高的成本--使得渗碳在许多工业应用中成为更通用、更有效的选择。氮化和渗碳的选择最终取决于零件的具体要求,包括预期用途、材料成分和所需的机械性能。
汇总表:
方面 | 氮化 | 渗碳 |
---|---|---|
渗氮深度 | 0.1 至 0.6 毫米(较薄) | 0.5 毫米至 2 毫米或以上(较深) |
材料兼容性 | 仅限于特定合金钢(如铬、钼、铝) | 与多种低碳钢和合金钢兼容 |
工艺温度 | 500°C 至 570°C(较低) | 850°C 至 950°C(较高) |
后处理 | 无需淬火(芯部硬度较低) | 淬火和回火(芯部硬度较高) |
表面处理 | 由于脆性 "白层",可能需要额外的表面处理 | 表面更光滑、更均匀 |
成本和复杂性 | 成本和复杂性更高(如气体/等离子氮化) | 成本效益更高,更容易实施 |
应用 | 对高冲击或贯穿硬化应用效果较差 | 更适合高冲击和贯穿硬化应用 |
需要帮助选择适合您应用的表面硬化工艺吗? 立即联系我们的专家!