烧结是一种利用热量和压力在不熔化的情况下压实和形成固体材料的工艺,但它也有一些影响其效率和效果的缺点。其中包括与设备耐用性、工艺控制、材料要求和运营成本有关的挑战。例如,烧结炉(如推板)面临严重的热冲击负荷,特别是在快速淬火时,这可能导致材料失效。此外,烧结过程可能比较缓慢,如马弗炉,而且可能需要精确控制温度和压力以确保产品质量。高昂的设备成本和对专业操作的需求进一步增加了烧结的缺点。
要点说明:
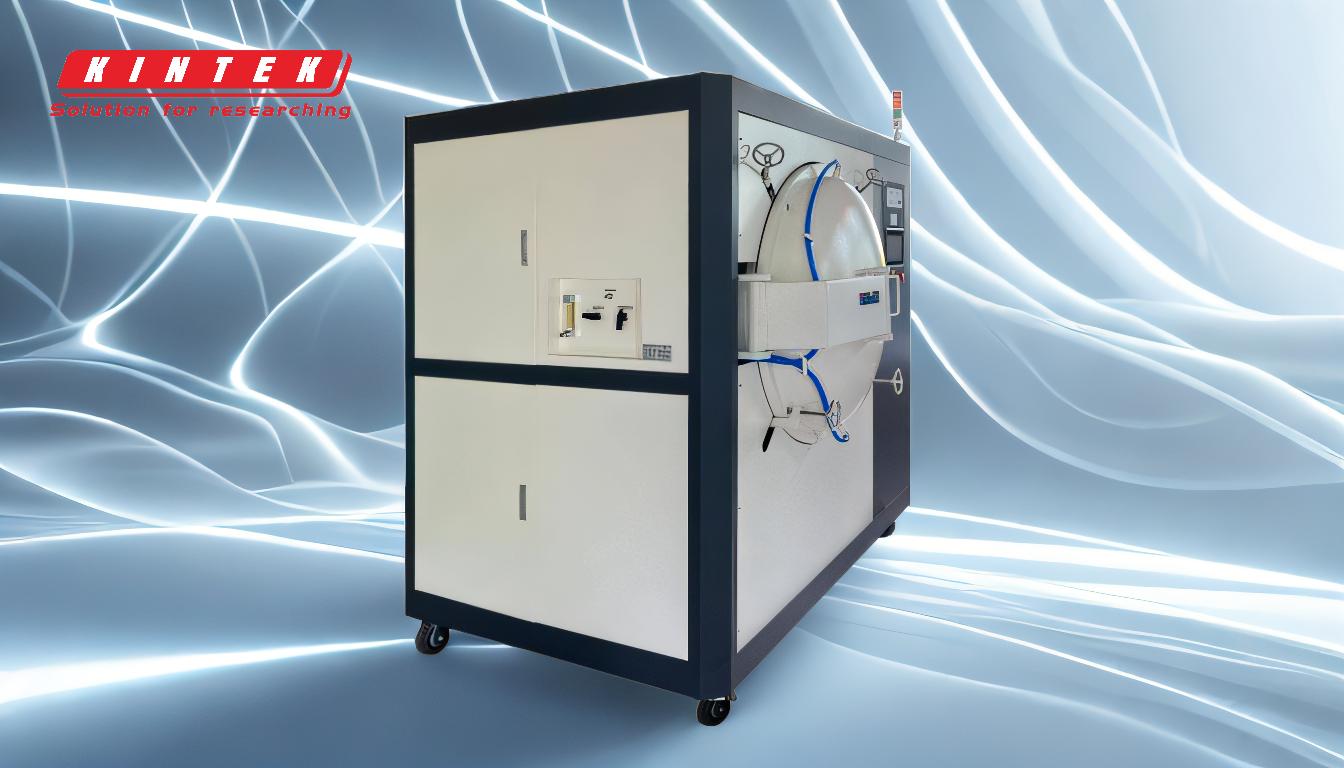
-
烧结炉中的热冲击载荷:
- 烧结炉中的推板 烧结炉中的推板 烧结炉会承受剧烈的热冲击载荷,尤其是当部件在烧结后立即淬火时。这种快速的温度变化会导致材料失效,尤其是在板材由不含二氧化硅的高纯度氧化铝制成的情况下。二氧化硅的缺乏会使材料更脆,对热循环的抵抗力更弱,随着时间的推移会导致裂缝和其他形式的退化。
-
马弗炉中的缓慢加热速率:
- 马弗炉是另一种烧结炉,与明火烧结法相比,马弗炉需要更长的时间才能达到所需的温度。对于需要快速预热和快速加工的项目来说,这种缓慢的加热速度可能是一个很大的缺点。此外,马弗炉的设计使其更难进入内部,需要小心放置材料,并可能使烧结过程复杂化。
-
感应炉缺乏精炼能力:
- 感应炉虽然在许多方面都很高效,但缺乏精炼能力。这意味着所使用的炉料必须不含氧化物且成分已知。任何杂质或未知元素都可能导致最终产品出现缺陷。此外,一些合金元素可能会在烧结过程中因氧化而损失,因此必须重新添加到熔体中,这可能会使工艺复杂化并增加成本。
-
设备和运营成本高:
- 烧结炉,尤其是热压烧结炉的设备成本很高。这些烧结炉需要对温度和压力进行精确控制,以确保均匀性和稳定性,而要做到这一点是非常困难的。此外,专业操作和维护的需求也增加了总体成本,使得烧结工艺比其他制造工艺更加昂贵。
-
材料和工艺控制挑战:
- 烧结需要精确控制各种参数,包括温度、压力和材料成分。任何与最佳条件的偏差都可能导致产品缺陷,如密度不均、裂缝或烧结不完全。这种控制水平很难持续实现,尤其是在大规模生产中,从而导致潜在的质量问题和浪费增加。
总之,虽然烧结是一种制造具有特定性能的固体材料的重要工艺,但它也有一些缺点,会影响其效率和成本效益。这些缺点包括设备耐用性、加热速度慢、缺乏精炼能力、设备和运营成本高以及需要精确的过程控制。了解这些缺点对于在制造工艺中何时以及如何使用烧结技术做出明智决策至关重要。
汇总表:
缺点 | 说明 |
---|---|
热冲击载荷 | 推板面临严重的热冲击载荷,导致材料失效。 |
加热速度慢 | 马弗炉加热时间较长,导致加工速度减慢。 |
缺乏精炼能力 | 感应炉需要纯净材料,增加了复杂性和成本。 |
设备和运行成本高 | 烧结炉价格昂贵,需要专业人员操作。 |
材料和工艺控制 | 精确控制温度和压力既具有挑战性,又成本高昂。 |
需要帮助优化烧结工艺吗? 立即联系我们的专家 获取量身定制的解决方案!