化学气相沉积(CVD)是一种广泛使用的薄膜沉积技术,具有高纯度、均匀性、可扩展性和多功能性等众多优点,适合电路和复杂表面涂层等应用。然而,它也有局限性,包括设备和前驱气体成本高、操作温度高,以及在大型或复杂材料涂层方面的挑战。下面,我们将详细探讨 CVD 的优缺点。
要点解析:
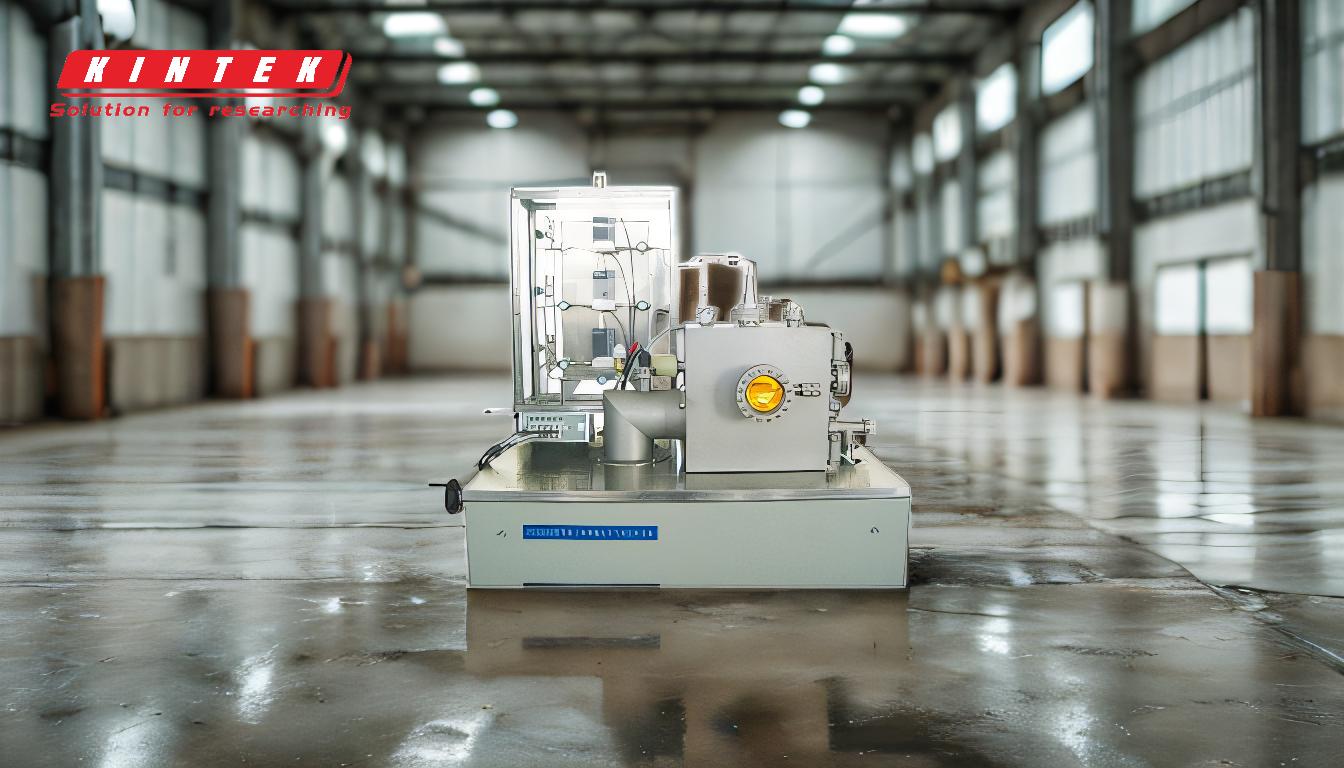
化学气相沉积 (CVD) 的优势:
-
薄膜的高纯度和高密度:
- CVD 可生产纯度和密度极高的薄膜,这对于半导体和光学镀膜等要求精确材料特性的应用至关重要。
- 该工艺依靠化学反应,可确保污染最小和高质量的结果。
-
均匀性和控制:
- CVD 可以精确控制沉积薄膜的厚度、成分和微观结构,为特定应用提供量身定制的特性。
- 薄膜在层内和整个基底表面都是均匀的,因此非常适合大面积涂层。
-
材料和基底的多样性:
- CVD 可以沉积多种材料,包括金属、半导体、陶瓷和聚合物。
- 它与金属、玻璃和塑料等各种基底材料兼容,因此非常适合不同行业。
-
可扩展性和高沉积速率:
- CVD 具有可扩展性,既适用于小规模研究,也适用于大规模工业生产。
- 它具有很高的沉积速率,因此能有效地快速生产大面积薄膜。
-
复杂表面的包覆特性:
- CVD 具有非视线特性,可为不规则或形状复杂的表面均匀镀膜,是精密部件和复杂设计的理想选择。
-
耐用的高性能涂层:
- CVD 生产的涂层经久耐用,可承受高压力环境、极端温度和温度变化。
- CVD 中使用的气体可针对特定性能(如耐腐蚀性或耐磨性)进行优化。
-
简单易操作的设备:
- 化学气相沉积设备的操作和维护相对简单,可减少操作复杂性和停机时间。
化学气相沉积(CVD)的缺点:
-
设备和前驱气体成本高:
- CVD 设备的初始投资很高,工艺中使用的前驱气体也很昂贵,从而增加了总成本。
-
操作温度高:
- CVD 通常需要较高的温度,这可能会限制其与对温度敏感的材料和基底的配合使用。
- 高温还可能导致涂层和基底产生残余应力,因此需要仔细控制沉积参数。
-
有限的现场应用:
- CVD 通常在专门的涂层中心进行,而不是在现场进行,这对某些应用可能不方便。
- 所有部件都必须拆卸成单个组件进行镀膜,增加了工艺的复杂性。
-
真空室的尺寸限制:
- 真空室的尺寸限制了对较大表面进行镀膜的能力,从而限制了其在大规模应用中的使用。
-
全有或全无涂层工艺:
- CVD 是一种 "全有或全无 "的工艺,这意味着很难对材料进行部分涂层或实现选择性覆盖。
-
前驱气体的潜在危害:
- 化学气相沉积过程中使用的某些前体气体可能具有危险性,需要采取严格的安全措施和处理规程。
-
实现完全覆盖的挑战:
- 虽然 CVD 可以对复杂的表面进行涂层,但要实现完全和均匀的覆盖可能具有挑战性,特别是对于复杂的几何形状。
结论
化学气相沉积是一种用途广泛的高效薄膜沉积方法,具有高纯度、均匀性和可扩展性等优点。它能够在复杂的表面上镀膜并生成耐用、高性能的薄膜,因此在电子、光学和航空航天等行业中不可或缺。然而,它的高成本、高工作温度以及在涂覆大型或对温度敏感材料方面的局限性是其明显的缺点。了解这些利弊对于选择 CVD 作为特定应用的合适沉积技术至关重要。
总表:
方面 | 优点 | 缺点 |
---|---|---|
纯度和密度 | 薄膜纯度高、密度大,是半导体和光学镀膜的理想材料。 | 设备和前驱气体成本高。 |
均匀性和控制 | 精确控制厚度、成分和微观结构。 | 工作温度高,限制了对温度敏感的材料的使用。 |
多功能性 | 可沉积多种材料,与各种基底兼容。 | 现场应用有限;需要专门的涂层中心。 |
可扩展性 | 既可用于小规模研究,也可用于大规模生产。 | 由于真空室的尺寸限制,限制了大规模应用。 |
复杂表面 | 均匀涂覆不规则或形状复杂的表面。 | 全涂或不涂工艺;难以实现选择性覆盖。 |
耐久性 | 为极端环境生产耐用的高性能涂料。 | 前驱气体具有潜在危险,需要采取严格的安全措施。 |
易于使用 | 设备简单,易于操作。 | 在实现复杂几何形状的完全覆盖方面存在挑战。 |
准备好探索 CVD 如何提高您的应用水平了吗? 今天就联系我们 获取专家指导!