火花等离子烧结(SPS)又称场辅助烧结技术(FAST),是一种先进的粉末冶金工艺,它将压力、电流和快速加热结合在一起,与传统烧结工艺相比,能在更低的温度和更短的时间内获得高密度材料。该工艺包括将粉末放入石墨模具中,施加单轴压力,并通过模具和粉末的高强度电脉冲。这将产生局部高温、等离子体和表面活化,从而促进颗粒粘合和致密化。通过焦耳加热、放电等离子体和塑性变形等机制,材料的密度可达 99% 以上。
要点说明:
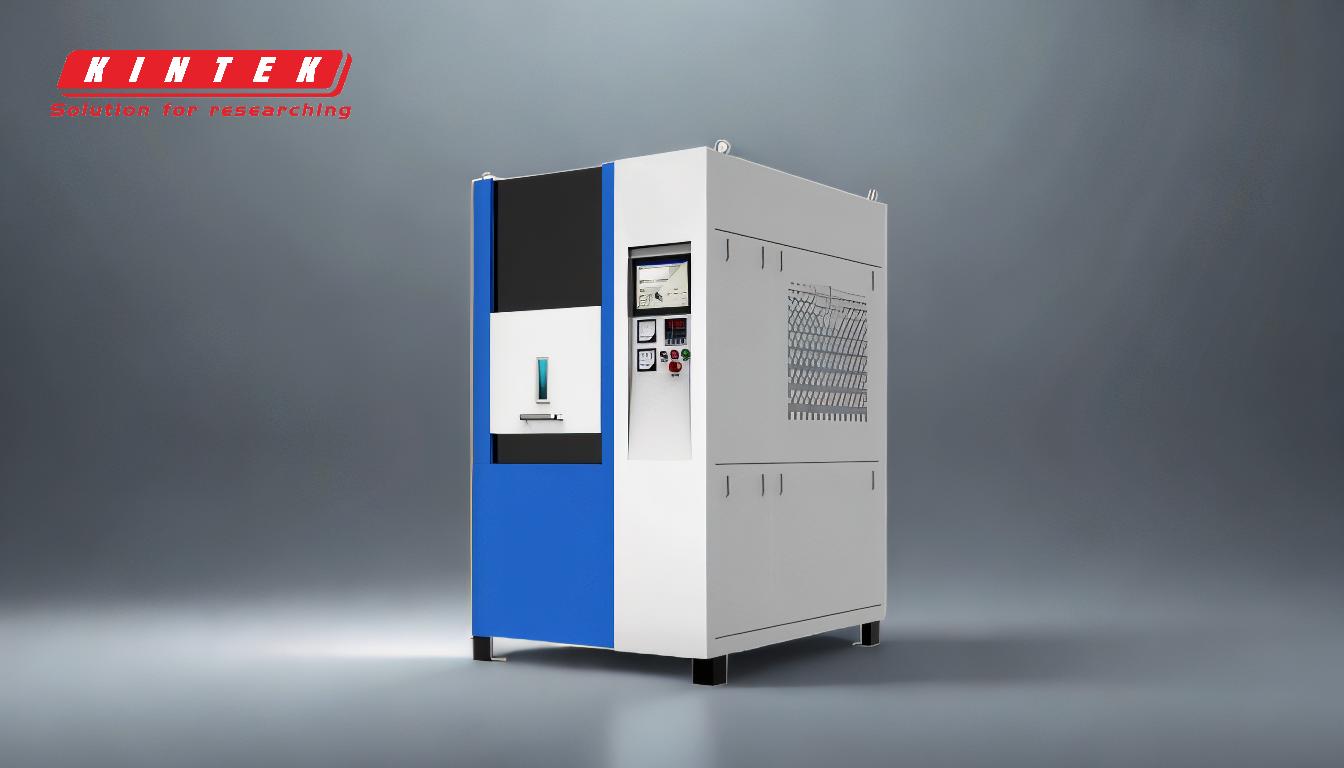
-
设置和初始条件:
- 石墨模具:将粉末放入石墨模具中,石墨模具既是模具又是热源。
- 单轴压力:对粉末密实体施加约 200 兆帕的压力,确保颗粒之间紧密接触。
- 电流:脉冲直流电流通过模具,如果导电,则通过粉末本身。
-
加热机制:
- 脉冲直流电流:高能脉冲电流在粒子间产生局部高温(高达 10,000°C ),导致火花放电和等离子体形成。
- 焦耳加热:粉末和模具对电流的阻抗产生焦耳热,有助于快速加热。
- 快速加热率:加热速度可达每分钟 1,000°C ,明显快于传统烧结方法。
-
颗粒粘结和致密化:
- 表面活化:放电激活颗粒表面,减少表面氧化物和污染物。
- 颈部形成:高温导致颗粒表面熔化,颗粒之间形成颈部。
- 塑性变形:施加的压力和局部加热会引起塑性变形,进一步缩小颗粒之间的间隙。
-
温度和时间控制:
- 高温:模具和样品的温度可高达 2400°C,但烧结温度通常低于传统方法。
- 保温时间短:该工艺在峰值温度下所需的保温时间通常很短,从而减少了能耗和加工时间。
-
致密化和最终性能:
- 高密度:在压力、电流和快速加热的共同作用下,材料的密度超过 99%。
- 微结构控制:快速加热和冷却可对微观结构进行精细控制,通常可获得更细的晶粒和更好的机械性能。
-
系统组件:
- 轴向压力装置:在烧结过程中施加并保持单轴压力。
- 水冷冲压电极:确保在加工过程中稳定的电气接触和冷却。
- 真空室:提供受控气氛,通常在真空或惰性气体下进行,以防止氧化。
- 气氛控制系统:管理炉室内环境,确保最佳烧结条件。
- 直流脉冲和冷却水:提供脉冲电流并管理散热。
- 位移和温度测量:监控浓缩进度和温度控制。
- 安全控制单元:确保系统安全运行,尤其是在高温高压条件下。
-
与传统烧结工艺相比的优势:
- 较低的烧结温度:SPS 所需的温度通常比传统烧结温度低几百度。
- 缩短加工时间:加热速度快,保温时间短,大大缩短了整体加工时间。
- 改进材料性能:精细的微观结构和高密度往往能带来卓越的机械、热和电气性能。
-
应用领域:
- 陶瓷和金属:SPS 广泛用于烧结陶瓷和金属粉末,包括碳化物、氮化物和复合材料等先进材料。
- 纳米材料:该工艺对烧结纳米材料特别有效,因为传统方法可能会导致晶粒过度生长。
- 复杂形状:在烧结过程中施加压力的能力可以生产出具有高尺寸精度的复杂形状。
总之,火花等离子烧结是一种高效、多功能的烧结技术,它利用电流、压力和快速加热来生产具有精细微结构的致密、高质量材料。与传统烧结方法相比,火花等离子烧结的优势使其特别适用于需要精确控制材料特性的先进材料和应用。
总表:
主要方面 | 详细信息 |
---|---|
设置 | 石墨模具、单轴压力(200 兆帕)、脉冲直流电流 |
加热机制 | 脉冲直流电流、焦耳加热、快速加热速率(高达 1,000°C/min) |
粒子粘合 | 表面活化、颈部形成、塑性变形 |
温度控制 | 高温(高达 2,400°C ),保温时间短 |
最终性能 | >密度大于 99%,微观结构精细,机械性能更好 |
优势 | 烧结温度更低、加工时间更短、性能更优越 |
应用领域 | 陶瓷、金属、纳米材料、复杂形状 |
利用火花等离子烧结技术改变您的材料加工工艺--联系我们的专家 立即联系我们的专家 了解更多信息!