类金刚石碳 (DLC) 涂层采用先进的沉积技术,可确保涂层坚固、耐用、性能卓越。最常见的方法包括物理气相沉积 (PVD) 和化学气相沉积 (CVD),以及射频等离子体辅助 CVD (RF PECVD) 和热丝 CVD 等变体。这些方法涉及在真空室中创造受控环境,使碳原子活化并沉积到基底上。方法的选择取决于基体材料、所需涂层特性和应用要求。DLC 涂层通常很薄(0.5 至 2.5 微米),具有出色的耐磨性、低摩擦性和更高的耐用性。
要点说明:
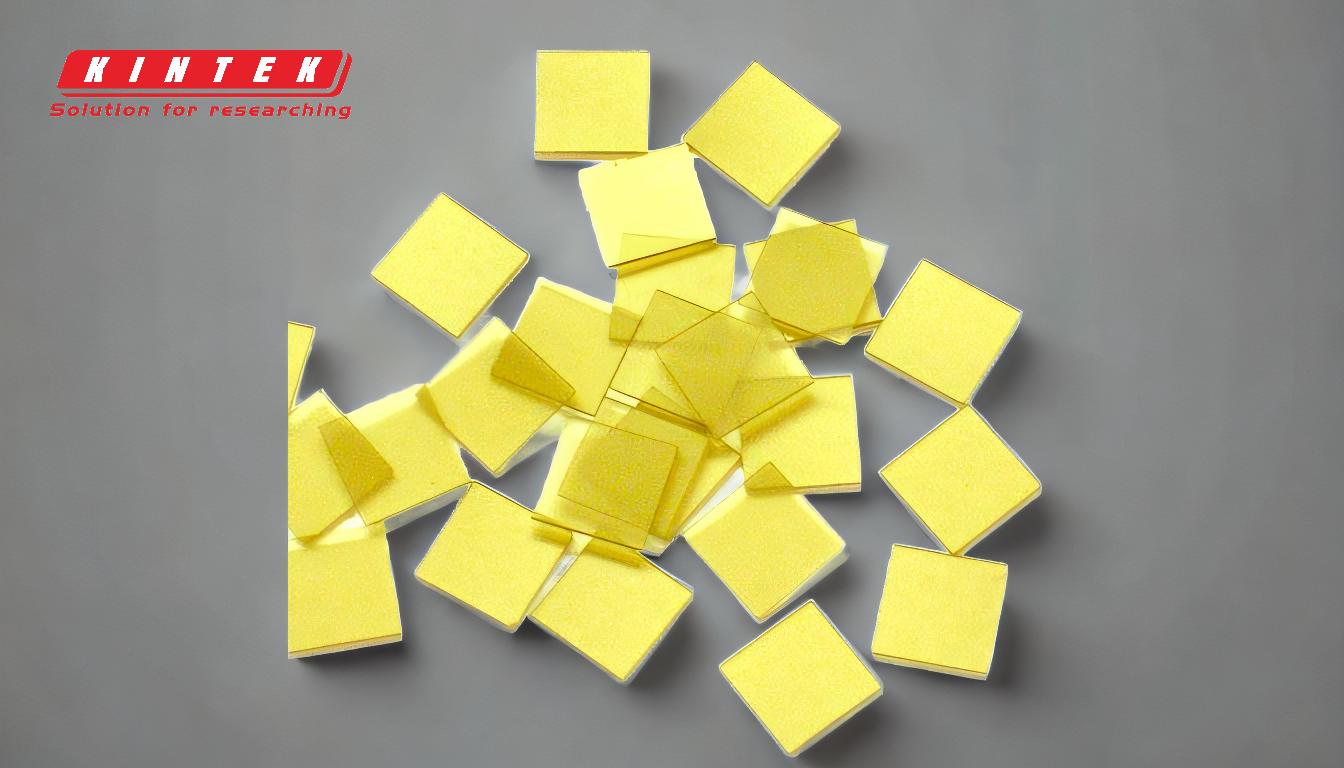
-
DLC 涂层应用概述
- DLC 涂层采用先进的沉积技术,形成一层薄而耐用的碳层,其中sp3 键占很大比例。
- 涂层工艺是根据基材材料和预期应用量身定制的,可确保最佳性能。
-
常见沉积方法
-
物理气相沉积(PVD):
- 包括蒸发源材料并使其凝结在基材上。
- 适用于在硬质合金工具上涂覆 DLC 涂层,涂层厚度一般为 0.5 至 2.5 微米。
- 其优点包括可精确控制涂层厚度和均匀性。
-
化学气相沉积(CVD):
- 包括将气相(如氢气和甲烷)中的碳原子沉积到基底上。
- 常见技术包括热丝 CVD、射频等离子体辅助 CVD(RF PECVD)和微波等离子体 CVD(MPCVD)。
- 需要高温(750°C 以上)激活气体分子并形成金刚石薄膜。
-
物理气相沉积(PVD):
-
CVD 涂层的分步流程
-
准备:
- 对基体(如碳化钨工具)进行清洁和准备,以确保涂层的正确附着。
-
装入真空室:
- 将准备好的工具放入装有氢气和甲烷气体的真空室中。
-
激活气体分子:
- 加热至 2300°C 以上的钨丝可提供分解气体分子的能量,并将工具加热至 750°C 以上。
-
碳原子沉积:
- 活性碳原子在工具表面重新结合,形成纯净的金刚石薄膜。
-
冷却和取出:
- 沉积完成后,冷却工具并将其从腔室中取出,以备使用。
-
准备:
-
不同方法的优势
-
PVD
- 加工温度较低,适用于对温度敏感的基底。
- 涂层厚度精度高且均匀。
-
CVD
- 生产高质量、纯净的金刚石薄膜,附着力极佳。
- 是高温应用和可承受极端条件的基材的理想选择。
-
PVD
-
DLC 涂层的应用
-
切削工具:
- 增强耐磨性,延长刀具寿命。
-
汽车部件:
- 减少发动机部件的摩擦,提高燃油效率。
-
医疗器械:
- 为手术器械提供生物相容性和耐磨性。
-
电子产品:
- 提高硬盘驱动器和传感器等部件的耐用性和性能。
-
切削工具:
-
设备和耗材采购商的注意事项
-
基体兼容性:
- 确保所选方法与基底材料(如硬质合金、钢或陶瓷)兼容。
-
涂层厚度和均匀性:
- 评估特定应用所需的厚度和均匀性。
-
成本和可扩展性:
- 考虑所选方法在大规模生产中的成本效益和可扩展性。
-
环境和安全因素:
- 评估沉积工艺对环境的影响和安全要求。
-
基体兼容性:
通过了解这些关键点,设备和耗材采购人员可以根据自己的具体需求,就最佳 DLC 镀膜方法做出明智的决定,从而确保最佳性能和成本效益。
汇总表:
方面 | 详细信息 |
---|---|
常用方法 | PVD、CVD(射频 PECVD、热丝 CVD) |
涂层厚度 | 0.5 至 2.5 微米 |
主要优点 | 耐磨、低摩擦、经久耐用 |
应用 | 切割工具、汽车零件、医疗设备、电子产品 |
基材兼容性 | 硬质合金、钢、陶瓷 |
温度范围 | PVD:较低温度;CVD:超过 750°C |
环境因素 | 真空室、受控气体环境 |
发现满足您需求的理想 DLC 涂层解决方案 立即联系我们的专家 !