热压是一种制造工艺,它将热量和压力结合起来,使材料(通常是陶瓷或金属)致密成形,形成接近理论密度的结构。它包括将粉末状材料放入模具中,施加单轴压力(10-30 兆帕),同时加热至烧结温度。与传统的冷压和烧结法相比,这种方法可加速致密化、缩短加工时间并改善材料性能。该工艺包括装填粉末、抽真空以去除杂质、加热以熔化粉末、施加压力以熔化材料、冷却以固化最终产品等步骤。热压工艺对于生产高密度、高性能且缺陷极少的材料尤为有效。
要点说明:
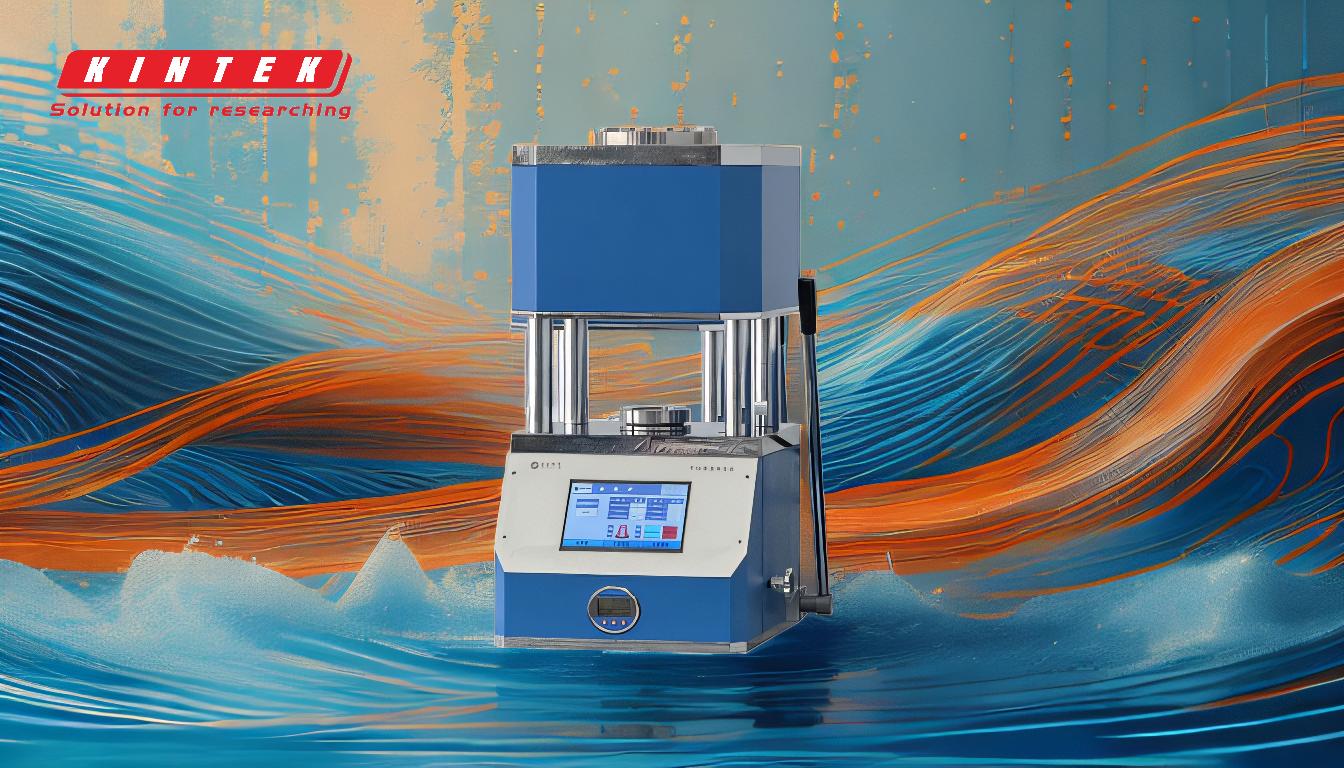
-
同时应用热量和压力:
- 热压工艺与传统的压制和烧结分离工艺不同,热压工艺将热量和压力结合在一个步骤中。这种同时进行的工艺大大缩短了相变和合金形成所需的时间。
- 该工艺包括将粉末状材料放入石墨模具,同时施加热量和压力。这可确保材料均匀致密,并达到接近理论密度的程度。
-
单轴压力:
- 通过一个简单形状的模具施加 10-30 兆帕的单轴压力。这种压力有助于压实粉末,提高致密化率。
- 施加的压力有助于减少孔隙率,改善最终产品的机械性能,使其更致密、更坚固。
-
热压工艺的步骤:
- 充电:将陶瓷或金属粉末装入熔炉或模具。
- 抽真空:炉内抽空,形成真空,除去可能导致最终产品缺陷的气体和杂质。
- 加热:温度升高到烧结温度,使粉末颗粒熔化并粘合在一起。
- 加压:施加压力,使粉末颗粒融合成致密的固体结构。
- 冷却:材料逐渐冷却至室温,使结构凝固,防止热应力。
-
与传统方法相比的优势:
- 缩短处理时间:与传统的冷压和烧结相比,热压结合了压制和烧结,大大缩短了整体加工时间。
- 改善材料性能:同时施加热量和压力可使材料具有更高的密度、更好的机械性能和更少的缺陷。
- 接近理论密度:热压使材料的密度接近理论最大值,这是其他方法难以达到的。
-
应用:
- 热压工艺广泛应用于高性能陶瓷、先进复合材料和特种金属的生产。在要求材料具有高强度、耐磨性和热稳定性的行业中,热压成型尤其有用。
- 常见应用包括航空航天部件、切削工具和电子基板。
-
环境条件:
- 热压可以在真空或惰性气体正压下进行。这种环境可以防止氧化和其他可能降低材料质量的化学反应。
- 真空或惰性气体的使用还有助于清除粉末中的残留气体或杂质,进一步提高最终产品的质量。
-
材料考虑因素:
- 模具材料(通常为石墨)的选择至关重要,因为它必须能够承受高温和高压,而不会变形或与粉末发生反应。
- 所用粉末的粒度分布必须均匀,以确保均匀致密化,避免最终产品出现缺陷。
了解了这些关键点,我们就能体会到热压工艺在生产具有优异性能的高质量致密材料方面的效率和效果。对于要求材料具有优异机械性能和热性能的行业来说,这种方法尤其具有优势。
汇总表:
主要方面 | 详细信息 |
---|---|
工艺流程 | 将热量和压力结合起来,使陶瓷或金属致密化。 |
压力 | 施加 10-30 兆帕的单轴压力。 |
步骤 | 装料、抽真空、加热、加压、冷却。 |
优点 | 缩短加工时间,提高材料性能,接近理论密度。 |
应用领域 | 航空航天部件、切削工具、电子基板。 |
环境 | 在真空或惰性气体中进行,以防止氧化。 |
材料考虑因素 | 石墨模具,粉末粒度分布均匀。 |
了解热压工艺如何提高您的材料产量 今天就联系我们 获取专家指导!