类金刚石碳(DLC)涂层的厚度变化很大。
从 10 纳米左右的超薄层到 2 至 40 微米的功能涂层不等。
厚度的选择取决于应用和所需的特定性能。
这些特性包括硬度、耐磨性和表面粗糙度。
1.超薄涂层(10 纳米)
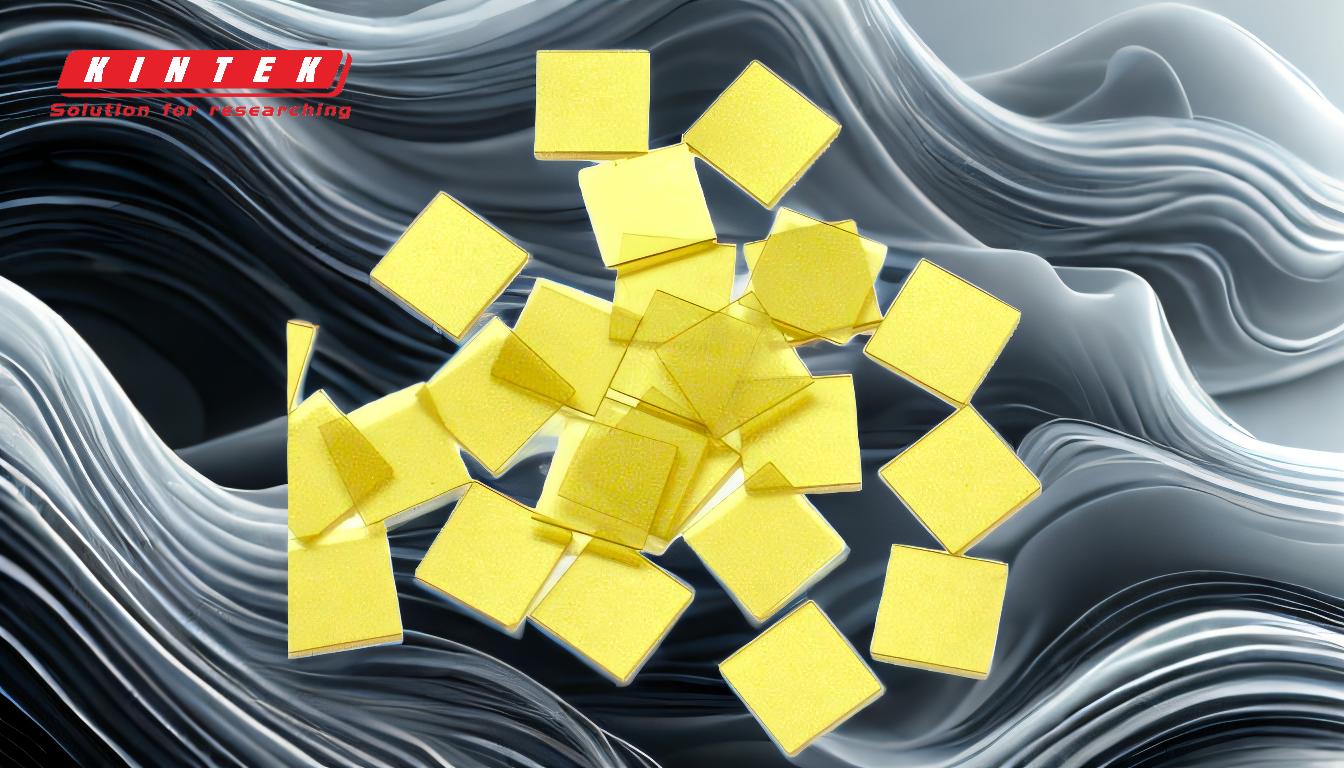
在金刚石薄膜研究的早期阶段,涂层通常很厚。
它们通常超过 1 微米。
然而,合成技术的进步使得生产更薄的涂层成为可能。
这些超薄层对于需要最小厚度而又不牺牲硬度和润滑性等基本特性的应用至关重要。
2.功能涂层(2-40 微米)
对于切削工具等更坚固的应用,需要更厚的涂层。
这些涂层的厚度从 2 微米到 40 微米不等,可增强耐用性和耐磨性。
这种涂层的沉积是一个缓慢的过程。
通常需要一到两天的时间。
因此,与 PVD 等其他涂层方法相比,金刚石涂层工具的成本较高。
3.成核和生长的影响
DLC 涂层的厚度在很大程度上取决于成核密度和核的大小。
为了提高非金刚石基底上金刚石薄膜的密度,已经开发出了改进的成核技术。
这样就能获得更薄但连续的涂层。
金刚石薄膜的初始生长通常遵循 Volmer-Weber 模型。
其特点是孤立金刚石岛的三维生长。
这就要求在非金刚石基底上形成连续薄膜的最小厚度为 100 纳米左右。
4.技术进步
跨学科研究推动了金刚石薄膜合成技术的发展。
这项研究涉及机械工程、化学工程、化学和物理学。
它导致了各种超薄金刚石涂层制造技术的发展。
这拓宽了超薄金刚石涂层的应用范围。
5.表征和质量
金刚石涂层的质量可通过拉曼光谱进行评估。
特定峰值的出现表明了金刚石的纯度和结晶度。
随着金刚石涂层晶粒尺寸的减小,拉曼光谱会出现峰值增宽。
这种额外特征的出现反映了材料结构和特性的变化。
总之,DLC 涂层的厚度可以定制,从 10 纳米的超薄层到高达 40 微米的功能涂层。
这取决于应用和底层基材的具体要求。
合成和沉积技术在不断发展。
这是因为需要在厚度、硬度和其他功能特性之间取得平衡的涂层。
继续探索,咨询我们的专家
发现 KINTEK SOLUTION 的类金刚石碳 (DLC) 涂层的精确性和多功能性!
从超薄到功能层,我们的先进涂层有多种厚度可供选择,可满足您应用的独特需求。
从切削工具到复杂的表面,现在就使用 KINTEK SOLUTION 的尖端 DLC 涂层来提高您的性能!
让我们一起探讨我们的专业解决方案如何优化您项目的成功--现在就联系我们进行免费咨询!