与传统的直流溅射方法相比,射频等离子体(尤其是射频溅射)具有若干显著优势。这些优势包括能够处理绝缘材料、减少电荷积聚和电弧、在较低压力下提高等离子体效率以及改善薄膜质量和均匀性。射频溅射还能最大限度地减少靶材侵蚀,避免阳极消失效应等问题。这些优势使射频溅射成为需要高质量薄膜的应用领域的首选,尤其是绝缘或半导体材料。
要点说明:
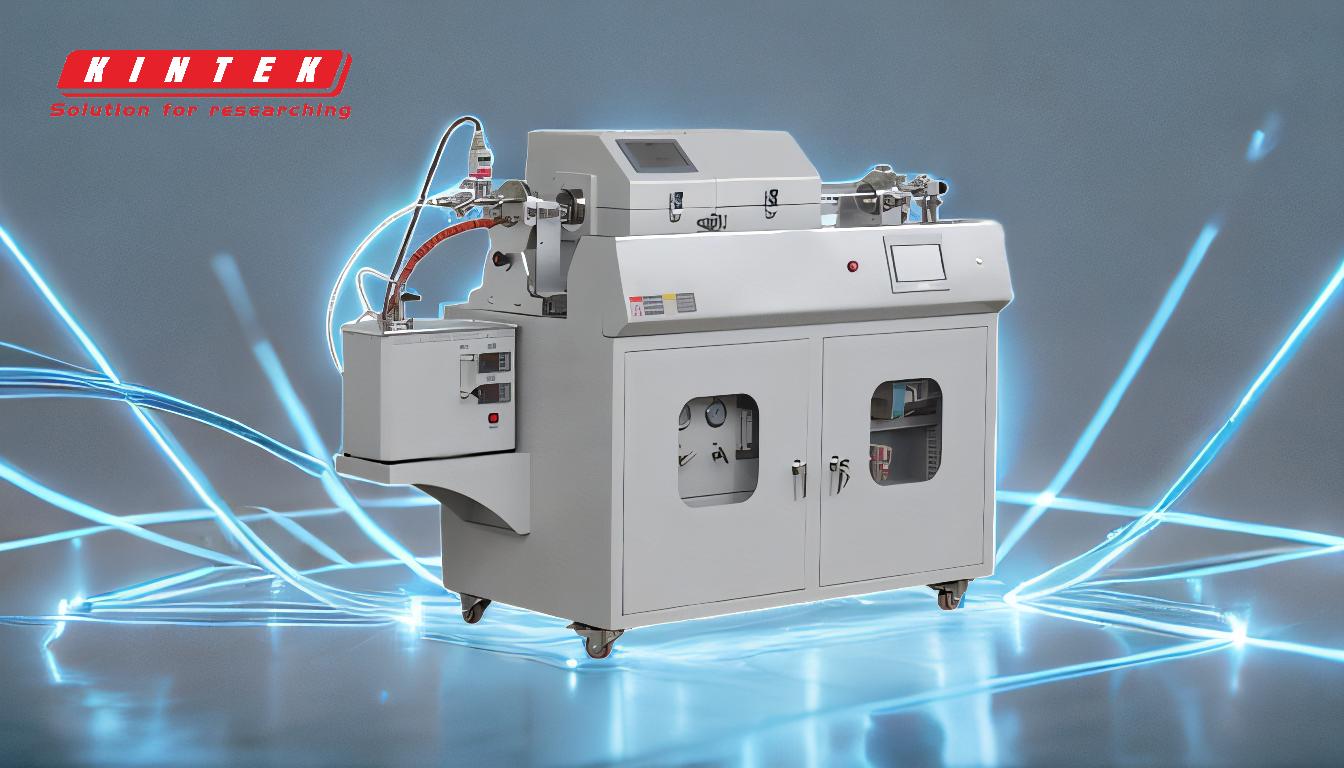
-
溅射绝缘材料的能力:
- 射频溅射可有效沉积氧化铝或氮化硼等绝缘材料,而使用直流方法溅射这些材料具有挑战性。射频溅射中的交变电场可防止靶材表面的电荷积聚,从而使用绝缘靶材时不会产生电弧或等离子体不稳定的风险。
-
减少电荷积聚和电弧:
- 射频场的振荡特性(通常为 13.56 MHz)可确保消除阴极或靶表面的电荷积聚。这降低了电弧产生的可能性,而电弧会损坏靶材并降低薄膜质量。因此,射频溅射能产生更均匀、质量更高的薄膜。
-
在较低压力下运行:
- 与直流溅射(约 100 mTorr)相比,射频溅射的工作压力要低得多(1-15 mTorr)。较低的压力减少了目标材料颗粒与气体离子之间的碰撞,为颗粒到达基底创造了更直接的途径。这就提高了沉积效率和薄膜质量。
-
更高的等离子效率:
- 射频溅射可在较低压力下产生较高的等离子电流,从而增加靶原子的平均自由路径并减少碰撞。这使得溅射过程更加高效,在相同腔室压力下,溅射率比直流溅射高出约 10 倍。
-
目标腐蚀最小化:
- 射频溅射减少了直流溅射中常见的 "赛道侵蚀 "问题,即靶材侵蚀不均匀,形成赛道图案。射频溅射涉及的靶材表面积更大,导致侵蚀更均匀,从而延长了靶材的使用寿命,提高了工艺稳定性。
-
提高薄膜质量和均匀性:
- 与直流溅射相比,射频溅射产生的薄膜具有更好的质量、阶跃覆盖率和微观结构。该工艺更稳定、缺陷更少、均匀性更好,因此适合需要精确薄膜沉积的应用。
-
无阳极消失效应:
- 与直流溅射不同,射频溅射不会出现阳极消失效应,即阳极被绝缘材料覆盖而失去功效。这确保了性能的一致性,并减少了频繁维护的需要。
-
材料沉积的多样性:
- 射频溅射可沉积多种材料,包括绝缘体、金属、合金和复合材料。这种多功能性使其适用于从半导体制造到光学镀膜的各种应用。
-
基片加热更低:
- 与直流溅射相比,射频溅射过程中基片的升温更低,这对温度敏感材料非常有利。这样就能沉积出高质量的薄膜,而不会影响基片的完整性。
-
射频二极管溅射技术的进步:
- 射频二极管溅射技术的最新发展进一步增强了射频溅射的优势。这种方法无需磁约束,可提供最佳的涂层均匀性,并确保非常平整的靶材侵蚀,不会形成赛道或靶材中毒。
总之,射频等离子溅射具有众多优势,包括能够处理绝缘材料、减少电弧和电荷积聚、在较低压力下运行、效率更高以及薄膜质量更好。这些优势使射频溅射成为需要精确和高质量薄膜沉积的应用的上佳选择。
汇总表:
优势 | 描述 |
---|---|
溅射绝缘材料 | 可在不产生电弧的情况下沉积氧化铝等绝缘材料。 |
减少电荷积聚和电弧 | 消除电荷积聚,减少电弧并提高薄膜均匀性。 |
在较低压力下运行 | 工作压力为 1-15 mTorr,可提高沉积效率和薄膜质量。 |
更高的等离子效率 | 产生更高的等离子电流,提高溅射率。 |
靶材侵蚀最小化 | 减少不均匀侵蚀,延长靶材寿命。 |
提高薄膜质量和均匀性 | 生产的薄膜微观结构更好,缺陷更少。 |
无阳极消失效应 | 确保性能稳定,无阳极涂层问题。 |
材料沉积的多样性 | 为各种应用沉积绝缘体、金属、合金和复合材料。 |
降低基底加热 | 减少基片加热,是温度敏感材料的理想选择。 |
射频二极管溅射技术的进步 | 提高涂层均匀性,消除赛道形成。 |
准备好提升您的薄膜沉积工艺了吗? 立即联系我们 了解射频溅射如何为您的应用带来益处!