溅射和蒸发都是用于制造薄膜的物理气相沉积(PVD)技术,但两者在机理、优势和应用上有很大不同。与蒸发相比,溅射具有多种优势,包括更好的附着力、更优越的薄膜质量和更精确的薄膜成分控制。蒸发更简单、更快速,而溅射则具有更高的均匀性、可扩展性以及与更多材料的兼容性。本分析探讨了溅射相对于蒸发的主要优势,重点关注附着力、薄膜质量、成分控制和可扩展性等因素。
要点说明
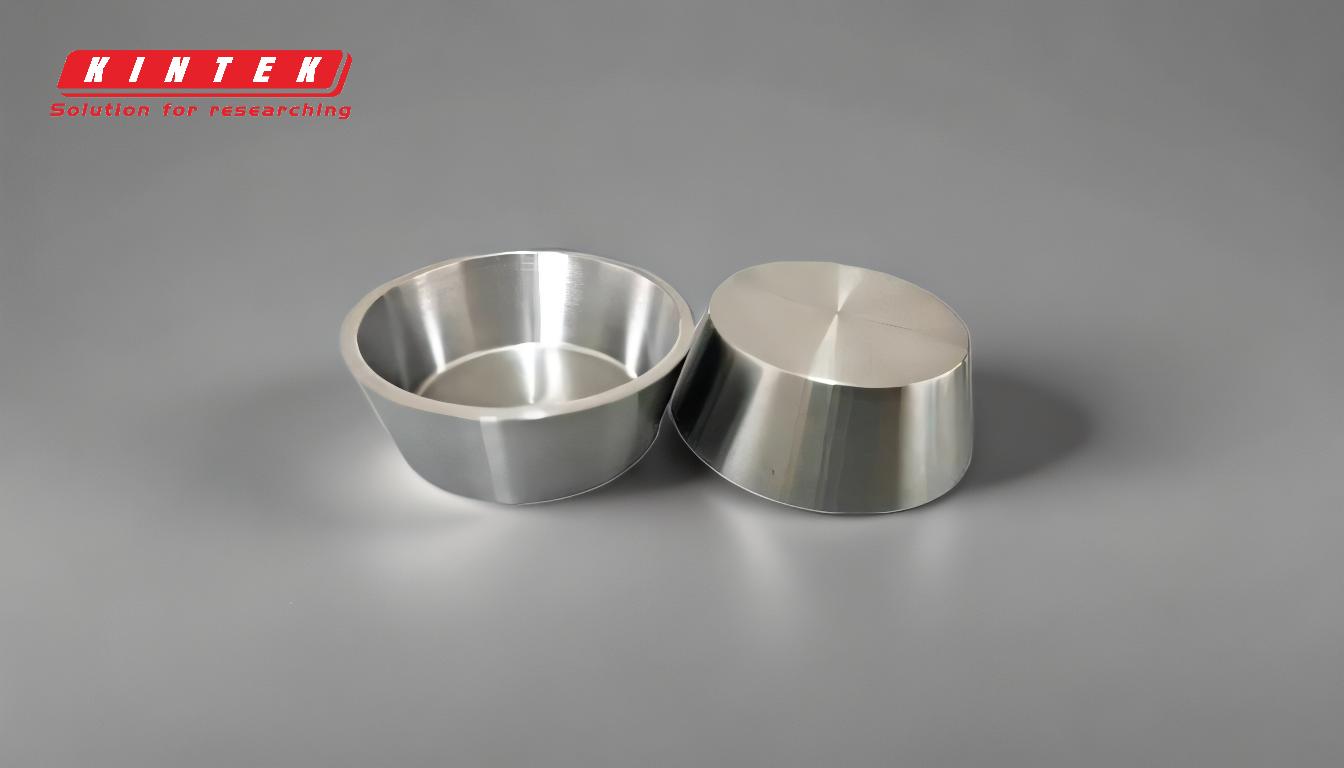
-
更好的粘性
- 与蒸发法相比,溅射法能使沉积薄膜与基底之间产生更强的附着力。这是因为溅射粒子具有更高的动能,使其能够更有效地嵌入基底表面。
- 在蒸发过程中,蒸汽流以较低的能量凝结在基底上,导致粘合和附着力减弱。
- 对于半导体器件或保护涂层等需要持久耐用涂层的应用来说,强大的附着力至关重要。
-
卓越的薄膜质量和均匀性
- 与蒸发法相比,溅射法生产的薄膜均匀性更好,缺陷更少。该工艺可精确控制薄膜厚度和成分,即使是复杂的几何形状也不例外。
- 蒸发虽然速度更快,但由于蒸汽流的方向性,往往导致薄膜的均匀性较差,尤其是在非平面表面上。
- 溅射技术可实现更高的薄膜质量,这对于光学镀膜等应用至关重要,因为在这些应用中,一致性和精确性是最重要的。
-
成分控制
- 溅射可在沉积薄膜中保持源材料的成分,因此非常适合沉积合金和复杂材料。这是因为溅射直接从靶材中喷射出原子,从而保持了原子的化学计量。
- 在蒸发过程中,尤其是合金蒸发过程中,不同元素的蒸发速度可能不同,从而导致沉积薄膜的成分差异。
- 这一优势使溅射成为沉积多组分材料的首选方法,例如在生产薄膜太阳能电池或磁性存储介质时。
-
高能沉积物种
- 与蒸发粒子相比,溅射粒子具有更高的能量,从而提高了薄膜密度并减少了孔隙率。这使得薄膜具有更好的机械和电气性能。
- 蒸发颗粒的能量较低,往往会形成密度较低、晶粒较大的薄膜,这会影响某些应用中的性能。
- 溅射粒子的能量较高,还能提高阶跃覆盖率,使其适用于微电子领域的沟槽和通孔涂层。
-
可扩展性和自动化
- 溅射技术具有很强的可扩展性,易于实现大规模生产的自动化。因此,它适用于需要稳定和高质量涂层的工业应用。
- 虽然蒸发法速度更快、成本效益更高,但其可扩展性较差,通常需要人工干预,限制了其在大批量生产中的应用。
- 溅射工艺自动化的能力可降低劳动力成本,提高可重复性,这对汽车和航空航天等行业至关重要。
-
与更多材料兼容
- 溅射可以沉积更广泛的材料,包括难以蒸发的高熔点金属、陶瓷和合金。
- 蒸发仅限于能在相对较低温度下蒸发的材料,这限制了其适用性。
- 这种多功能性使溅射成为先进应用的首选方法,例如在半导体制造中沉积难熔金属。
-
更低的真空要求
- 与蒸发法相比,溅射法的真空度更低,从而降低了真空系统的复杂性和成本。
- 蒸发需要较高的真空度,以防止污染并确保高效蒸发,这就增加了运营成本。
- 溅射技术对真空度的要求较低,因此更适合较小规模的操作和研究实验室。
-
环境和安全优势
- 溅射通常比蒸发更安全、更环保,因为它不需要将材料加热到极高的温度,从而降低了热分解或有害排放的风险。
- 蒸发,尤其是电子束蒸发需要高温,这可能会带来安全风险和环境问题。
总之,与蒸发相比,溅射在附着力、薄膜质量、成分控制和可扩展性方面具有显著优势。虽然蒸发在某些应用中速度更快、成本效益更高,但溅射是高精度、高性能涂层的首选方法,适用于从微电子到光学等各种行业。溅射技术能够沉积各种具有优异性能的材料,因此是现代薄膜沉积技术中用途广泛且可靠的选择。
总表:
方面 | 溅射 | 蒸发 |
---|---|---|
附着力 | 由于粒子的动能更高,粘附力更强 | 由于蒸汽流的能量较低,粘合力较弱 |
胶片质量 | 卓越的均匀性、更少的缺陷和精确的厚度控制 | 薄膜不太均匀,尤其是在非平面表面上 |
成分控制 | 保持源材料成分,是合金和复杂材料的理想选择 | 不同汽化率导致的成分差异 |
粒子的能量 | 更高的能量可提高薄膜密度并减少孔隙率 | 能量越低,薄膜密度越小,晶粒尺寸越大 |
可扩展性 | 可扩展性强,易于自动化,适合大规模生产 | 可扩展性较差,通常需要人工干预 |
材料兼容性 | 可沉积多种材料,包括高熔点金属 | 仅限于可在低温下汽化的材料 |
真空要求 | 在较低真空度下运行,降低了系统复杂性和成本 | 需要更高的真空度,增加了运行成本 |
环境安全 | 更安全、更环保,无需极度加热 | 温度升高带来安全和环境风险 |
准备好提升您的薄膜沉积工艺了吗? 立即联系我们 了解溅射技术如何满足您的需求!