激光烧结公差对于确保 3D 打印部件的精度和质量至关重要。该工艺涉及使用激光逐层熔化粉末材料,实现严格的公差对于要求高精度的应用至关重要。根据所提供的参考资料,定制烧结技术可将线性和同心度公差控制在一微米以内。通过对激光参数、材料特性和工艺优化的先进控制,可以实现这一精度水平。
要点说明:
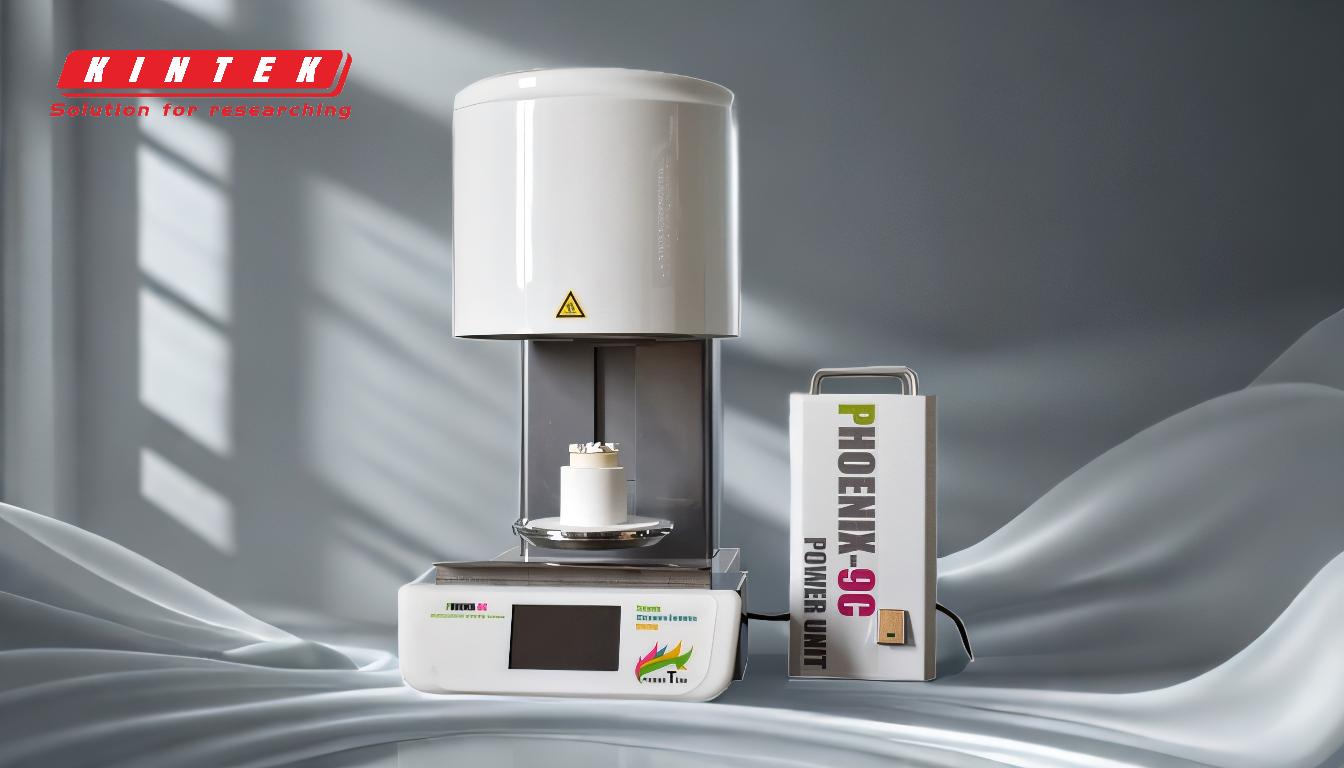
-
激光烧结公差的定义:
- 公差是指制造部件与指定尺寸或几何形状之间的允许偏差。
- 在激光烧结中,公差受激光功率、扫描速度、层厚度和材料特性等因素的影响。
-
实现一微米以内的公差:
- 参考文献指出,定制烧结技术可确保线性度和同心度在一微米以内。
-
这种精度水平是通过以下方式实现的:
- 先进的激光控制:精确控制激光功率和扫描速度,最大限度地减少变化。
- 材料优化:使用粒度和分布一致的材料,确保烧结均匀。
- 工艺监控:实时监控和调整烧结过程,以保持严格的公差。
-
影响公差的因素:
- 激光参数:激光的强度、聚焦和扫描模式对烧结部件的精度有很大影响。
- 层厚:较薄的层通常可以获得更高的精度,但可能会增加制造时间。
- 材料特性:材料的导热性、熔点和粒度会影响其烧结程度和最终尺寸精度。
- 机器校准:定期校准激光烧结机对保持性能稳定至关重要。
-
需要严格公差的应用:
- 医疗器械:植入物和手术工具等部件要求高精度,以确保适当的配合和功能。
- 航空航天:飞机和航天器部件必须满足严格的公差要求,以确保安全和性能。
- 微电子:电子设备中的小型复杂元件通常需要几微米以内的公差。
-
保持公差的挑战:
- 热失真:烧结过程中产生的热量会导致零件翘曲或变形,影响尺寸精度。
- 材料收缩:有些材料在冷却时会收缩,这必须在设计和烧结过程中加以考虑。
- 表面光洁度:在保持严格公差的同时实现光滑的表面光洁度是一项挑战。
-
提高公差的策略:
- 工艺优化:微调激光参数和烧结策略,尽量减少偏差。
- 后处理:可以使用机械加工或抛光等技术来实现所需的公差和表面光洁度。
- 增材制造设计(DfAM):在设计零件时考虑烧结公差,例如考虑收缩或变形。
总之,通过先进的技术和对工艺参数的精心控制,激光烧结可以实现线性度和同心度公差在一微米以内。然而,要保持如此严格的公差,需要将优化的材料、精确的激光控制和全面的过程监控结合起来。这些公差对于医疗、航空航天和微电子等行业的高精度应用至关重要。
汇总表:
主要方面 | 详细内容 |
---|---|
公差定义 | 激光烧结零件与规定尺寸之间的允许偏差。 |
实现 1 微米精度 | 先进的激光控制、材料优化和实时过程监控。 |
影响因素 | 激光参数、层厚度、材料特性和机器校准。 |
应用领域 | 医疗设备、航空航天和微电子。 |
挑战 | 热变形、材料收缩和表面光洁度。 |
改进策略 | 工艺优化、后处理和增材制造设计 (DfAM)。 |
您的项目需要精密激光烧结? 今天就联系我们的专家 了解更多信息!