薄膜纳米粒子的制备采用多种沉积技术,可精确控制薄膜的厚度、成分和特性。这些方法大致可分为物理、化学和电学工艺。常见的技术包括物理气相沉积(PVD)、化学气相沉积(CVD)、溅射、蒸发、旋涂和逐层组装。每种方法都有其自身的优势,并根据所需的薄膜特性和用途进行选择。退火或热处理等沉积后工艺也可用于增强薄膜的性能。
要点说明:
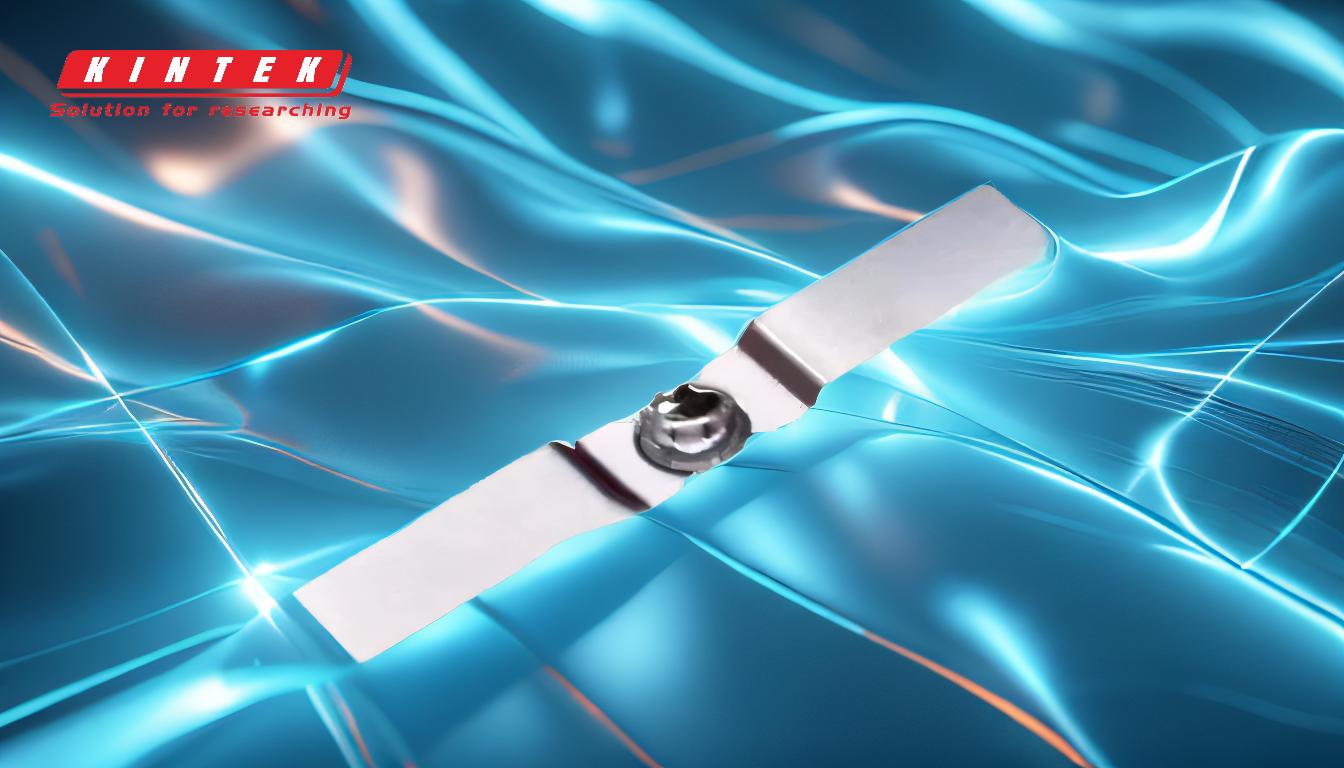
-
选择材料(目标)
- 制备薄膜纳米粒子的第一步是选择合适的沉积材料。这种材料被称为目标材料,可以是金属、半导体、聚合物或其他化合物,具体取决于所需的薄膜特性。
- 材料的选择至关重要,因为它决定了最终薄膜的电气、光学和机械性能。
-
将目标材料运送到基底
- 一旦选定了目标材料,就需要将其传送到形成薄膜的基底上。这可以通过蒸发、溅射或化学反应等各种方法实现。
- 在物理气相沉积(PVD)中,目标材料在真空中气化,然后凝结在基底上。
- 在化学气相沉积(CVD)中,目标材料以气体形式传输,然后在基底上发生化学反应形成薄膜。
-
沉积技术
- 物理气相沉积(PVD): 包括蒸发和溅射等方法。在蒸发法中,目标材料被加热至汽化,然后凝结在基底上。在溅射法中,高能粒子轰击目标材料,使原子喷射出来并沉积在基底上。
- 化学气相沉积(CVD): 这是一种利用化学反应沉积薄膜的方法。前驱气体被引入反应室,在此分解或与其他气体发生反应,从而在基底上形成薄膜。
- 旋转镀膜: 这种技术是将目标材料的液态溶液涂在基底上,然后高速旋转基底,使溶液均匀扩散并形成薄膜。
- 逐层组装(LbL): 这种方法是交替沉积不同的材料层,在精确控制其成分和厚度的情况下形成薄膜。
-
沉积后工艺
-
薄膜沉积后,可能会经过其他工艺来增强其性能。这些工艺包括
- 退火: 将薄膜加热至高温,以提高其结晶度并减少缺陷。
- 热处理: 与退火类似,但可能涉及特定的温度曲线,以达到所需的机械或电气性能。
-
薄膜沉积后,可能会经过其他工艺来增强其性能。这些工艺包括
-
应用和注意事项
-
沉积方法和沉积后工艺的选择取决于薄膜的预期应用。例如
- 半导体: 由于 PVD 和 CVD 能够生产高纯度薄膜并精确控制厚度,因此被广泛使用。
- 柔性电子器件: 旋转涂层和 LbL 组装可在柔性基底上沉积薄膜,因此是首选。
- 光学镀膜: 溅射和蒸发通常用于制造具有特定光学特性的薄膜。
-
沉积方法和沉积后工艺的选择取决于薄膜的预期应用。例如
-
优点和缺点
- PVD 技术: 纯度高、附着力好,但可能需要复杂的设备和高真空条件。
- 化学气相沉积: 可形成均匀的涂层,并可沉积复杂的材料,但可能涉及危险化学品和高温。
- 旋转涂层: 对于小规模生产而言,操作简单,成本效益高,但可能不适合大型或复杂的基板。
- LbL 组装: 这种方法可以很好地控制薄膜的成分和厚度,但耗时较长,而且可能需要专门的设备。
总之,制备薄膜纳米粒子涉及一系列精心控制的步骤,从材料选择到沉积和沉积后处理。技术的选择取决于所需的薄膜特性及其预期应用,每种方法都有其自身的优势和挑战。
汇总表:
沉积技术 | 主要特点 | 应用 |
---|---|---|
物理气相沉积(PVD) | 纯度高、附着力强 | 半导体、光学涂层 |
化学气相沉积 (CVD) | 均匀涂层、复杂材料 | 半导体、电子 |
旋转镀膜 | 简单、经济 | 柔性电子器件 |
逐层 (LbL) 组装 | 精确的成分控制 | 柔性电子器件、传感器 |
沉积后工艺 | 目的 | |
退火 | 提高结晶度,减少缺陷 | |
热处理 | 增强机械/电气性能 |
需要帮助选择适合您项目的沉积技术? 立即联系我们的专家 !