PVD(物理气相沉积)涂层以其薄度而闻名,通常范围为 0.02 至 5 微米,常见应用通常在 3-5 微米范围内。这种薄度是一个关键优势,因为它可以保持切削刀具的锋利度,减少切削力和热量的产生,并最大限度地降低基材热损坏的风险。该工艺在相对较低的温度(约 500 °C)下运行,这进一步防止了大多数材料的变形。 PVD 涂层在真空条件下涂覆,可确保沉积精确且均匀,并且在冷却过程中形成压应力,有助于防止裂纹形成和扩展。这些特性使 PVD 涂层成为高性能应用的理想选择,例如切削工具、光学涂层和精密部件。
要点解释:
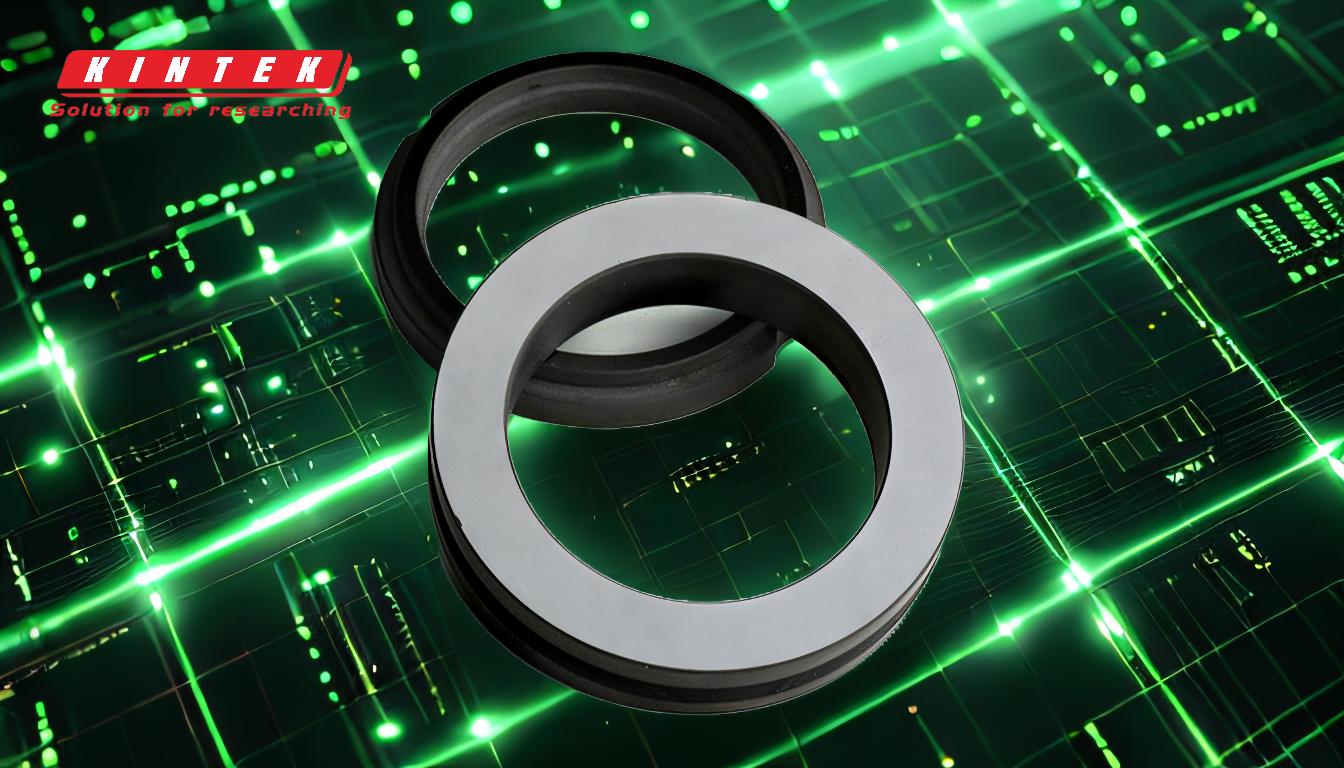
-
PVD涂层厚度范围:
- PVD 涂层非常薄,通常范围为 0.02至5微米 。在保持工具的锋利度和精度至关重要的应用中,这种薄度是一个显着的优势。
- 对于切削刀具,厚度通常落在 3-5微米范围 ,足以增强硬度和耐磨性,而不影响刀具的刃口锋利度。
-
薄 PVD 涂层的优点:
- 保持清晰度 :PVD 涂层很薄,可确保刀片等切削工具保持锋利,从而实现更好的性能和更长的工具寿命。
- 减少切削力和热量 :薄涂层可降低加工过程中所需的切削力,从而最大限度地减少热量的产生和基材热损坏的风险。
- 压应力的形成 :在冷却阶段,PVD 涂层形成压应力,有助于防止裂纹形成和扩展,使其适合断续切削工艺(例如铣削)等要求苛刻的应用。
-
低温沉积:
- PVD 涂层在相对较低的温度下应用,通常约为 500℃ ,明显低于 CVD(化学气相沉积)等其他涂层方法。这种低温工艺降低了基材热变形的风险,使其适用于多种材料,包括热敏材料。
-
真空沉积工艺:
- PVD 工艺是在以下条件下进行的 真空条件 ,保证了涂层材料的沉积精确、均匀。真空环境还可以防止传导和对流,只允许通过辐射进行热传输,这有助于涂层的高质量和一致性。
-
PVD 薄涂层的应用:
- 切削工具 :PVD 涂层广泛用于高速钢 (HSS) 和硬质合金切削刀具,因为它们能够在不影响刀具几何形状的情况下提高硬度和耐磨性。
- 精密零件 :PVD 涂层薄而均匀,使其成为公差严格的零件的理想选择,例如塑料注射成型部件和精冲工具。
- 光学镀膜 :PVD 中薄膜的精确沉积使其适用于均匀性和厚度至关重要的光学应用。
-
环境效益:
- PVD涂层是一种 环保 过程。它不会产生废物或有害气体,也不会改变不锈钢等材料的可回收价值。这使其成为寻求减少环境影响的行业的可持续选择。
-
工艺步骤及特点:
- PVD 工艺包括三个主要步骤:(1) 汽化 涂层材料,(2) 迁移 原子、分子或离子的组成,以及 (3) 沉积 将这些颗粒附着到基底上。该工艺产生纯净、高质量的涂层,通过降低粗糙度来提高表面质量。
-
制造的多功能性:
- PVD 镀膜机是 计算机控制 ,允许高精度并能够处理大批量、大规模制造和小批量生产。这种多功能性使得 PVD 涂层适用于从汽车到航空航天等多种行业。
总之,PVD 涂层的厚度加上其低温沉积、真空精度和环境效益,使其成为提高各行业工具和组件性能和耐用性的高效解决方案。
汇总表:
方面 | 细节 |
---|---|
厚度范围 | 0.02至5微米(常见:切削刀具为3-5微米) |
优点 | 保持锋利度、降低切削力、防止热损坏 |
沉积温度 | ~500 °C(低温工艺) |
过程 | 基于真空,确保沉积精确、均匀 |
应用领域 | 切削工具、精密部件、光学镀膜 |
环境影响 | 环保,无废物或有害气体 |
使用超薄 PVD 涂层增强您的工具 — 今天联系我们 了解更多!